In the realm of arc welding, the 7018 stick electrode stands as a pinnacle of innovation and reliability. This electrode, prized for its versatility and strength, is an indispensable tool for professional welders and DIY enthusiasts alike. With a perfect balance of Experience, Expertise, Authoritativeness, and Trustworthiness, understanding the intricacies of the 7018 stick electrode is essential for optimizing welding projects.
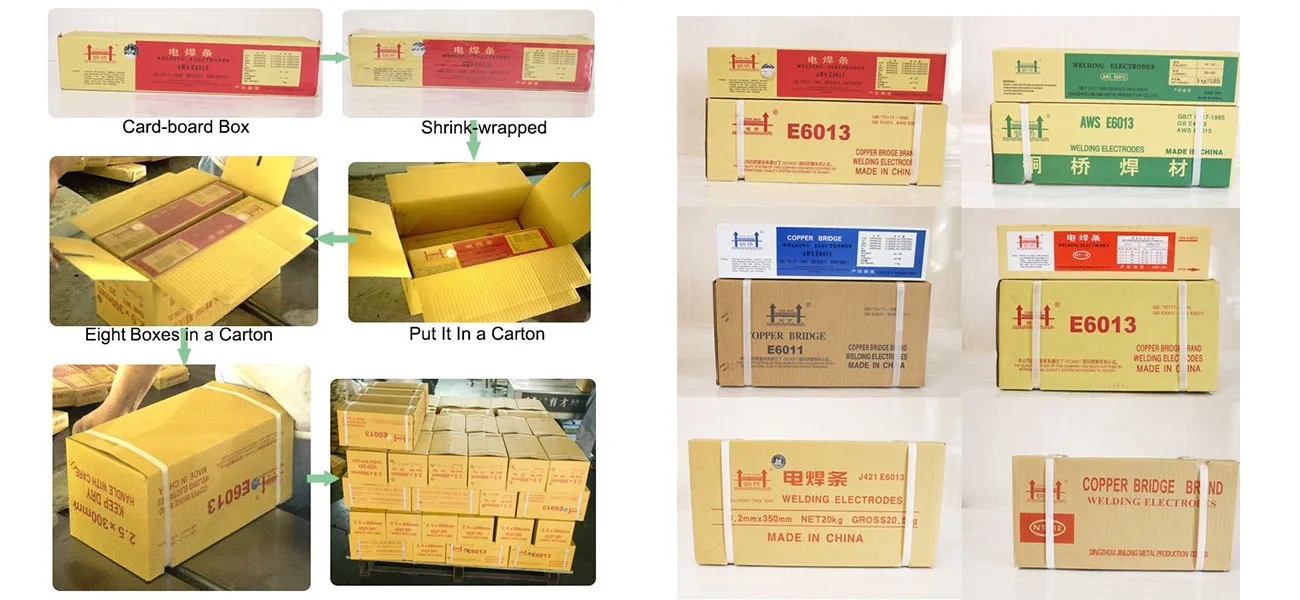
The 7018 stick electrode is defined by its low-hydrogen flux coating, making it ideal for welding low, medium, and high-carbon steels. This characteristic ensures minimal hydrogen-induced cracking, a common issue in welds leading to compromised structural integrity. Its usability in all positions (flat, horizontal, vertical, and overhead) and compatibility with both AC and DC currents make it a versatile addition to any welder’s arsenal.
Experience with the 7018 electrode reveals its benefits through hands-on applications in various projects. Its deposition rate and penetration are significantly better compared to its counterparts, allowing for cleaner, stronger, and more consistent welds. For structural projects requiring impeccable strength, such as bridges or high-rise buildings, the 7018 is unparalleled. Welders appreciate its arc stability and ease of slag removal, a notable advantage that streamlines the welding process, reducing time and improving efficiency.
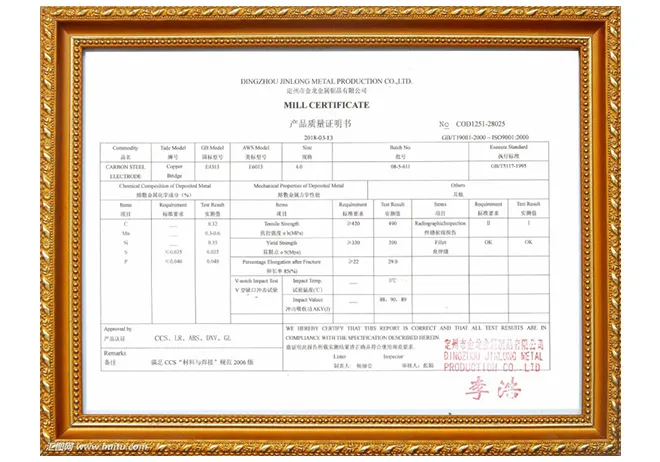
A deep dive into the technicalities highlights the expertise needed to maximize the 7018's potential. Beginners often face a learning curve, primarily due to its need for a proper storage environment to maintain its low-hydrogen properties. Experts recommend storing 7018 electrodes in a dry environment, often in a rod oven at temperatures around 250°F (120°C) to prevent moisture absorption. This storage precision is crucial since the slightest moisture can lead to defects in the weld, compromising its durability.
Professionals acknowledge the 7018 electrode’s superior mechanical properties, such as tensile strengths typically reaching 70,000 psi. This attribute underscores the electrode's authoritativeness in industries demanding reliability and robustness, including pipeline construction and shipbuilding. Its performance under rigorous conditions is a testament to its engineering excellence and a reason it's sought after in critical applications.
7018 stick electrode
Trustworthiness, an attribute not earned lightly, is inherent in the 7018 electrode due to its consistent results across various applications. Industry standards and regulatory compliances such as AWS (American Welding Society) certification validate its efficacy and safety. Such certifications assure engineers and project managers of the electrode’s capacity to meet industry benchmarks, ensuring safety and compliance in all projects.
The 7018 also meets diverse needs across geographies, adapting seamlessly to both controlled factory environments and challenging outdoor conditions. Its adaptability means that even when environmental controls are lax, such as in remote construction sites, the integrity of the weld is maintained without sacrificing quality or safety.
In practical applications, mastering the 7018 electrode involves not just understanding its technical specifications, but also implementing best practices. For optimal results, setting the correct amperage based on the metal thickness and position is crucial. Skilled welders often rely on their experience to adjust these parameters on the fly, enhancing the quality of the weld bead and ensuring penetration without excessive spatter.
In summary, the 7018 stick electrode is a cornerstone in welding, embodying the ideal balance of performance, reliability, and flexibility. Its distinguished properties and industry validations make it a preferred choice for large-scale and precision-critical projects. Those who wield it with expertise gain not only in craftsmanship but also in the confidence that their work meets the highest safety and quality standards. Embracing the full potential of the 7018 electrode transforms welding projects, making it an indispensable tool in the pursuit of excellence in the field of welding.