The 7018 stick weld rod has long stood as a hallmark of welding for professionals seeking high-quality results. Known for its robust performance, durability, and versatility, the 7018 rod is often referred to as the low hydrogen electrode. It’s essential to grasp the ins and outs of this welding staple to fully appreciate what it brings to the table regarding skill requirements and project suitability.
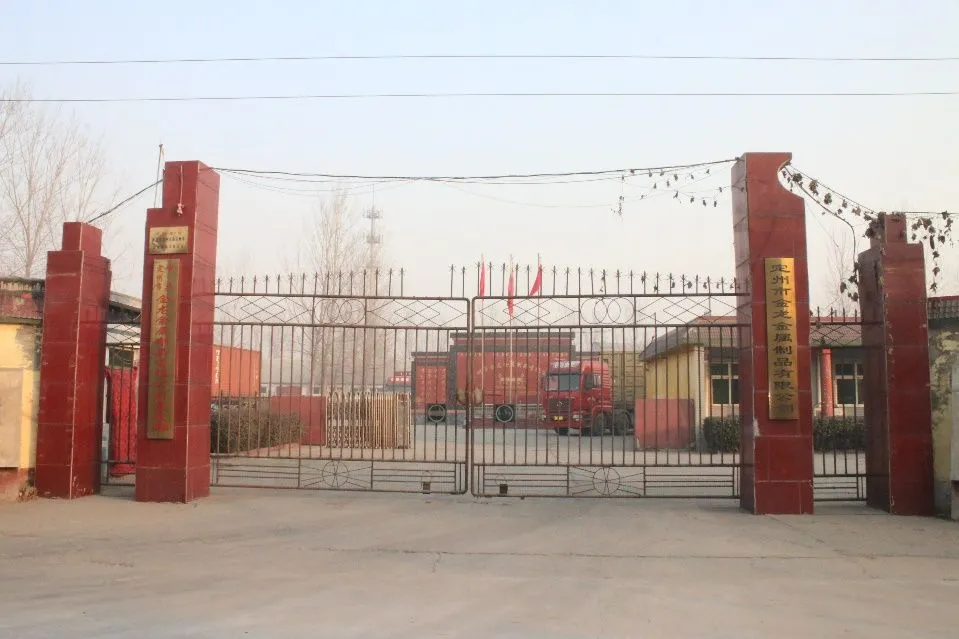
First, diving into the specifics, the 7018 designation provides significant insight into its capabilities. The ‘70’ signifies a tensile strength of 70,000 psi, which is critical information for welders working on projects requiring high structural integrity. The ‘1’ indicates its all-position capabilities, making it adaptable for flat, horizontal, vertical, and overhead welding tasks. The final digit, ‘8,’ points to the rod’s coating and welding current. The low hydrogen potassium coating ensures minimal hydrogen-induced cracking, while its compatibility with AC and DC currents adds further flexibility.
Achieving optimal performance with the 7018 rod requires more than just an understanding of its specifications. Real-world experience suggests an emphasis on pre-weld preparation. Unlike other rods, 7018 electrodes must be stored in a moisture-controlled environment. This is critical because moisture on the rod can lead to hydrogen inclusion in the weld, consequently increasing the risk of weld defects. Professional welders often advocate for storing these rods in an electrode oven at temperatures around 250°F-300°F until use.
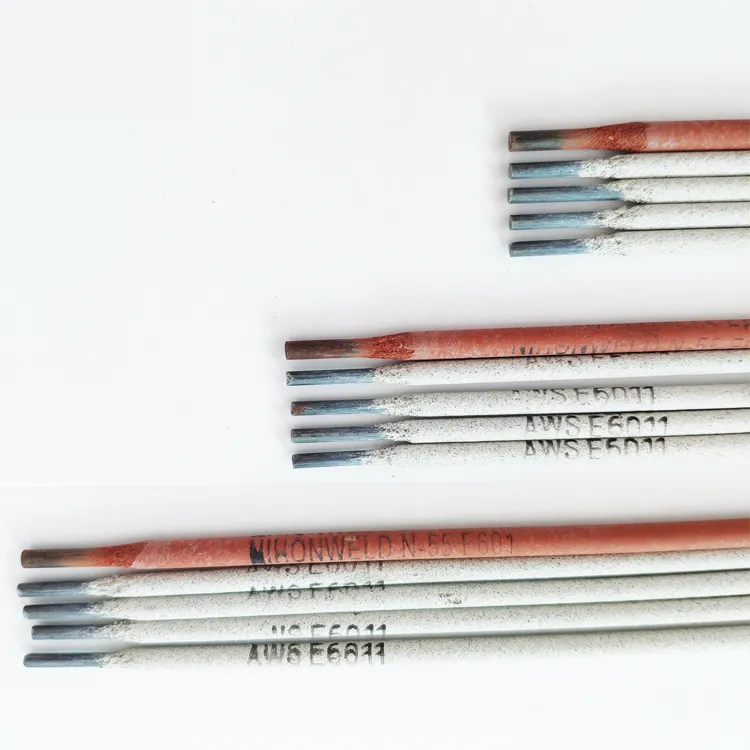
For beginners, mastering the use of the 7018 rods involves practice with puddle control due to its tendency to produce a smooth and fluid arc. This characteristic is beneficial for professional-looking welds but can also be challenging for novices to manage. Moreover, maintaining the correct angle and travel speed is vital to avoid issues such as slag inclusions or undercutting. Practice, therefore, should focus on technique refinement, ensuring the ability to produce clean, strong welds consistently.
In terms of professional application, the 7018 rod is favored in industries where weld integrity is non-negotiable. Structural steel work, including bridges, buildings, and pipelines, relies heavily on the performance reliability of 7018 welds. The rod’s ability to yield high-strength and ductile welds makes it indispensable when weld quality cannot be compromised.
7018 stick weld
End-users in these fields often choose the 7018 stick weld not just for performance, but also for compliance with industry standards. The rod’s adherence to stringent guidelines, such as those outlined by the American Welding Society (AWS), supports its position as a go-to electrode in critical applications. Professionals in these areas understand that when integrity and safety are priorities, the choice of electrode can make a significant difference.
Another aspect of the 7018 rod that underscores its expert-level use is weld appearance. Due to its low hydrogen characteristics and stable arc, the weld bead is typically visually appealing, boasting a smooth, flat, and even surface. This level of aesthetic quality makes the 7018 a preferred choice in projects where the visual presentation of the weld is as crucial as its functional strength.
Trust in the 7018 stick weld is not just theoretical but grounded in extensive field use and testing. Welding professionals and experts frequently share testimonials of its unparalleled reliability in both routine and demanding conditions. This dependability, reinforced by a blend of scientific principles and practical application, offers peace of mind for welders striving for excellence in their work.
In conclusion, the 7018 stick weld rod embodies a pinnacle of welding expertise, demanding a combination of skill, precision, and understanding of its unique properties and requirements. Whether the need is for structural resiliency, industry compliance, or consistent quality, the 7018 continues to be a staple for experts who demand the best for their projects. Through precise handling and informed use, it remains a cornerstone of reliable and effective welding practices across the globe.