Unlocking the Potential of the 7018 Rod 3/16 A Comprehensive Guide
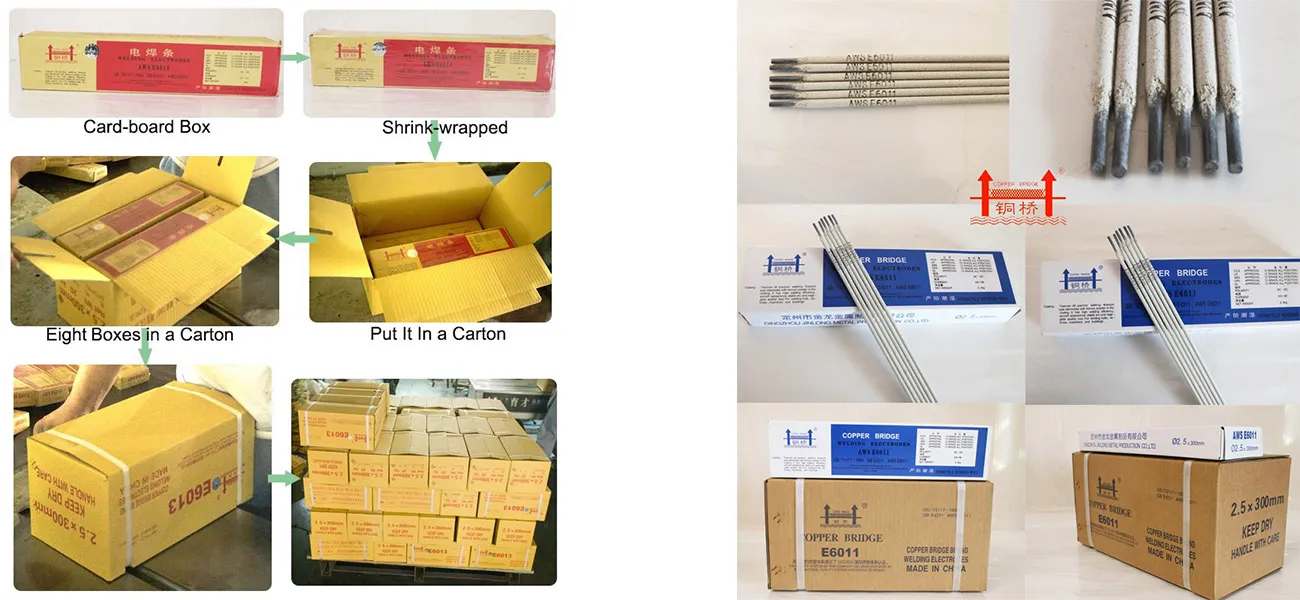
Understanding the capabilities and applications of the 7018 rod 3/16 can significantly enhance your welding projects and skills. This versatile welding electrode is renowned for its ease of use and superior welding performance, earning its place as a staple in both amateur and professional welding settings.
The 7018 rod, categorized under the AWS A5.1 specification for covered carbon steel electrodes, is known for its low-hydrogen iron powder coating, which minimizes the risk of cracking in the weld zone. The specific 3/16-inch diameter is suited for medium to heavy-duty applications, offering a balance of control and weld deposition that many professionals appreciate.
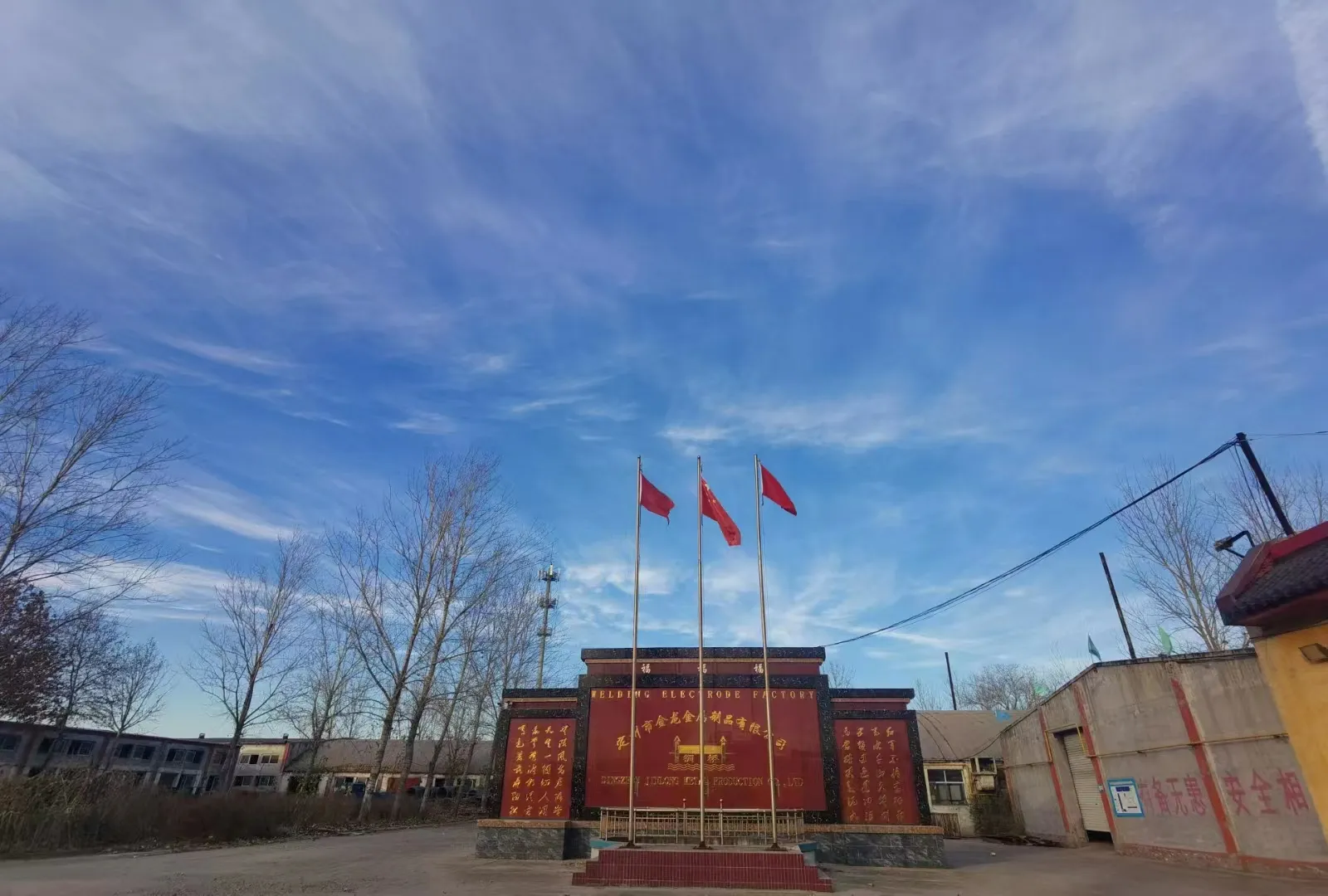
Experience counts when selecting welding electrodes, and the 7018 rod 3/16 shines with its user-friendly characteristics. Novices often find this rod forgiving due to its smooth arc and low spatter production. Personal testimonials highlight how it consistently delivers sound welds with minimal cleanup, a significant advantage for any project timeline. Professionals with years of experience recount how this rod significantly reduces post-weld clean-up time, which can enhance productivity and project efficiency.
In terms of expertise, the 7018 rod 3/16 requires users to have a solid understanding of proper storage to maintain its low-hydrogen characteristics. Moisture is a known adversary to this rod, and using it without proper storage can compromise weld integrity. Keeping the rods in a rod oven set to a stable temperature is critical to preventing moisture absorption. This protocol is vital knowledge for maintaining the rod's optimal performance and ensuring a strong, reliable weld.
The 7018 rod's authority in the welding industry is undeniable. It has been the go-to choice for structural welding, shipbuilding, and even pressure vessels. Its design inherently supports out-of-position welding, allowing welders the flexibility to work on complex joints with ease. Moreover, its ability to produce welds with good mechanical properties under demanding conditions underscores its reliability and effectiveness.
7018 rod 3 16
Trustworthiness is crucial in welding applications, where safety and durability are often paramount. The 7018 rod 3/16's reputation is underpinned by rigorous testing and compliance with industry standards, offering peace of mind to welders and engineers alike. Its consistent performance in creating high-quality, strong welds inspires confidence among users, reflected in countless successful project outcomes.
With the right technique, the 7018 rod 3/16 easily facilitates clean, resilient welds. Experts recommend maintaining a short arc length and steady travel speed to optimize weld quality and appearance. Such precision ensures complete fusion and prevents common issues such as lack of penetration or porosity, which can compromise weld strength.
In the realm of welding rods, the 7018 rod 3/16 stands out not just for its technical specifications, but for the tangible benefits it brings to a welder's toolkit. Its seamless fusion of performance and reliability makes it an invaluable resource, whether you're reinforcing structural beams or undertaking intricate repair work.
For those keen to enhance their welding productivity and output quality, integrating the 7018 rod 3/16 into your practice is a compelling proposition. Its proven track record and adaptability make it a must-have for any serious welding project, guaranteeing results that stand up to demanding standards and conditions.
In summary, the 7018 rod 3/16 is not simply a tool, but a critical ally in achieving welding excellence. Its blend of experience-driven reliability, expert-backed guidelines for optimal use, authoritative industry standing, and persistent trustworthiness ensure it remains a premier choice in the welding industry.