The 7018 low hydrogen electrode is a cornerstone in the world of welding, a domain where both precision and expertise are crucial. Known for its reliability and robust performance, the 7018 electrode is favored by professionals across various industries, particularly where quality and durability are essential. This type of electrode falls under the category of low hydrogen electrodes, which are designed specifically to minimize the amount of hydrogen in the weld area.
This reduction is pivotal in preventing cracking and other hydrogen-related issues in the welded metal.
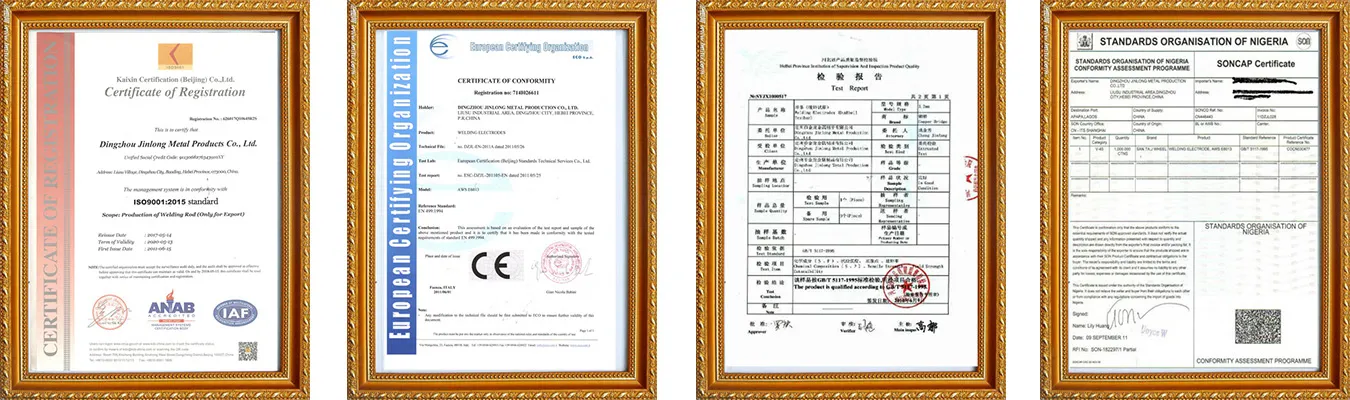
Experience has shown that welders who utilize the 7018 electrode appreciate the quality of welds it produces. Its superior strength and clean finish make it ideal for industrial applications, especially in structural steelwork, shipbuilding, and pipeline welding. The electrode’s composition plays a significant role in its effectiveness. It typically consists of an iron powder coating enveloped in a low hydrogen compound, which considerably reduces the risk of hydrogen embrittlement.
In terms of expertise, using the 7018 electrode requires a deep understanding of its characteristics and the conditions under which it performs best. Welders often need to maintain the electrodes at specific temperatures to prevent moisture absorption, which could increase hydrogen levels. Storage and handling are, therefore, crucial; electrodes should be kept dry and preheated if they have been exposed to humidity. Mastering the use of the 7018 electrode enhances a welder’s capability to produce x-ray quality welds, which is vital in high-pressure and high-stress applications.
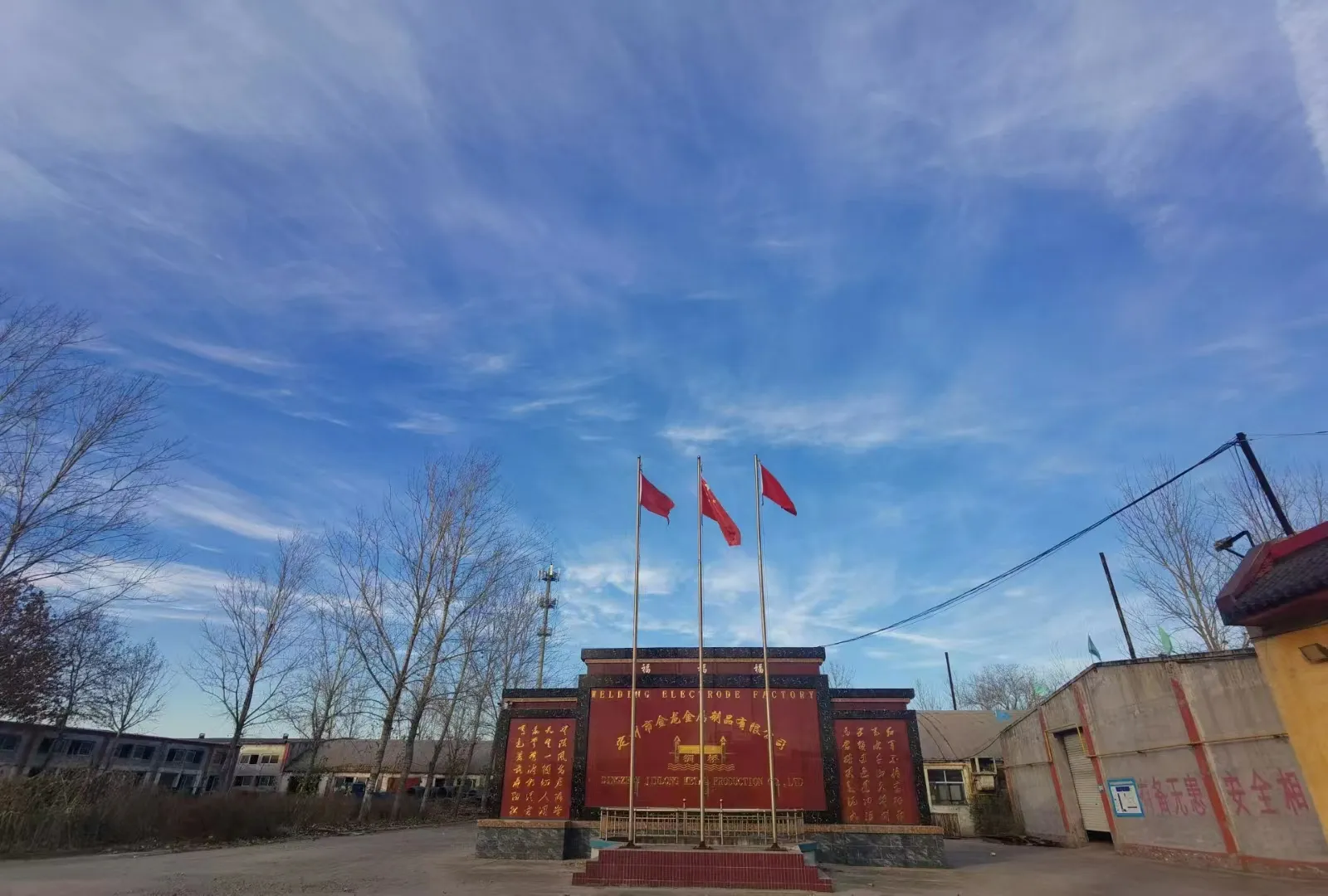
7018 low hydrogen electrode
Authoritativeness in the use of 7018 electrodes is demonstrated by the widespread endorsement by welding certification bodies and manufacturers. This type of electrode is often recommended in building codes and engineering standards due to its mechanical properties and ease of use. Professionals in the field recognize that employing a 7018 electrode can meet rigorous quality standards, ensuring the structural integrity of the constructions.
Trustworthiness is built upon the consistent results the 7018 electrode delivers. Feedback from field experts confirms that when used correctly, it minimizes the risks associated with post-welding defects. The electrode’s ability to produce welds that withstand extreme environmental conditions is repeatedly validated in industry applications. Furthermore, its compatibility with a range of power sources adds to its versatility, making it a reliable choice for both AC and DC welding setups.
In conclusion, the 7018 low hydrogen electrode stands out as a preferred choice among welders due to its exemplary performance rooted in cutting-edge metallurgical engineering. Its consistent results and adaptability to varying welding conditions underscore its reputation for quality and reliability. By ensuring proper storage and proficient handling, welders can leverage the full potential of this electrode, thus achieving optimal outcomes in their projects. For those in the industry, understanding and using 7018 electrodes is not just a matter of skill but also a testament to professional integrity and commitment to excellence in welding practices.