Navigating the complexities of welding in the modern era, the role of 7018 low hydrogen electrodes cannot be overstated. This unique welding component has revolutionized practices across numerous industries, showcasing unparalleled efficiency in ensuring structural integrity and reliability.
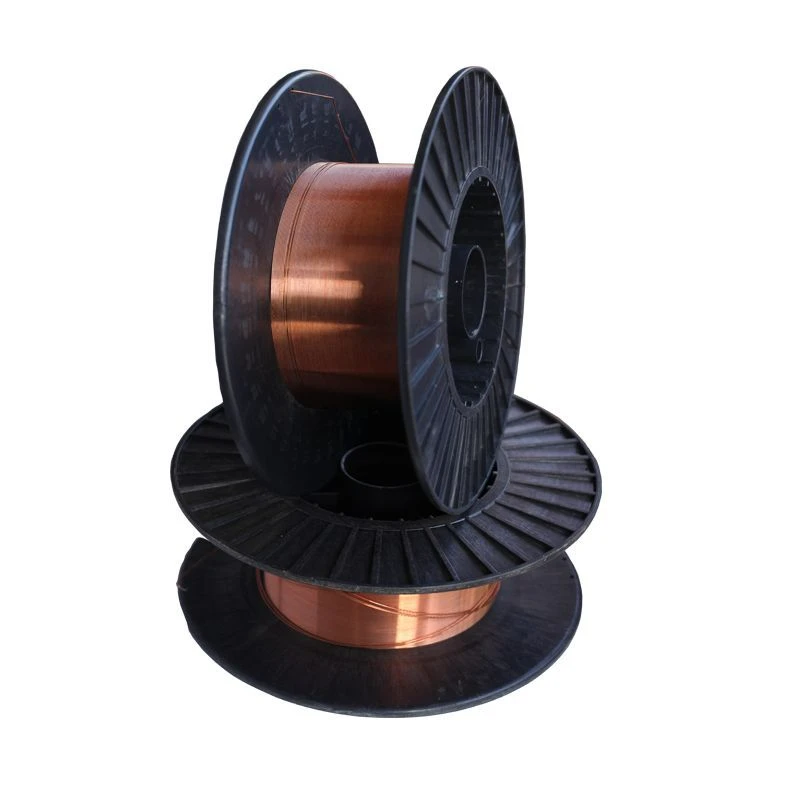
7018 low hydrogen electrodes are engineered with a distinct chemical composition that significantly reduces hydrogen levels in the welding process. This reduction is critical in preventing hydrogen-induced cracking, a notorious issue that can compromise the strength and durability of welded joints. By utilizing 7018 low hydrogen electrodes, professionals benefit from an enhanced weld quality, which is particularly vital in structural applications such as bridges, high-rise buildings, and pressure vessels.
Drawing from years of field experience, it's noticeable how 7018 electrodes outperform other options on the market in terms of ease of use and adaptability. Even under less-than-ideal conditions, such as high humidity environments or where preheating is impractical, the 7018 electrodes show remarkable resilience and maintain impeccable deposition rates.
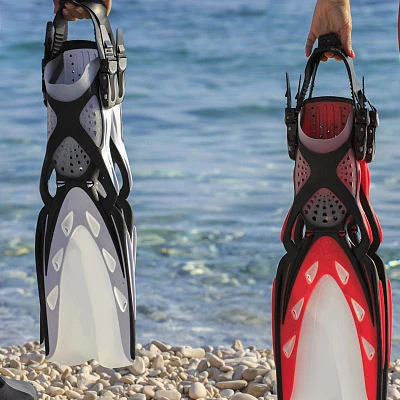
The professional consensus endorses 7018 low hydrogen electrodes not just for their mechanical advantages, but also for the refined microstructure they impart to the weld metal. This microstructure not only provides superior mechanical properties but also enhances toughness and ductility, which are critical in environments subjected to dynamic or cyclic loads.
Industry experts often highlight the electrodes’ compatibility with various welding machines and their suitability for multiple welding positions—flat, horizontal, vertical, and overhead. This versatility makes them an invaluable tool in a welder’s arsenal, capable of adapting to a wide array of projects and challenges.
Furthermore,
7018 electrodes are enveloped in a low moisture coating, which plays a pivotal role in shielding the electrode from environmental contamination. Maintaining their moisture-protective layer ensures consistent low hydrogen levels, as even minor contamination can lead to significant weld defects. For professionals aiming to optimize their welding output, storing these electrodes in a dry, stable environment is non-negotiable.
7018 low hydrogen
In terms of expertise, it's critical for welders to be familiar with the specific operational parameters of 7018 electrodes. Optimal performance is achieved at specific amperage settings, which vary depending on the thickness of the workpiece and welding position. Adjustments might be necessary to fine-tune these settings, highlighting the importance of skill and experience in achieving the highest quality welds.
Authoritativeness in the domain of welding also encompasses a thorough understanding of regulations and standards. The use of 7018 low hydrogen electrodes is often dictated by industry standards such as AWS (American Welding Society) and ASME (American Society of Mechanical Engineers) codes. Professionals must ensure compliance with these guidelines to meet safety and performance criteria.
Trustworthiness in advocating for 7018 electrodes comes from the consistent testimonies of seasoned welders who attest to their reliability and performance under strenuous conditions. Years of usage across various sectors underline their role as a trusted component in accomplishing structurally sound welds.
To ground these insights in practical application, consider the case study of a recent infrastructure project where 7018 low hydrogen electrodes were pivotal. Engineers faced unpredictable weather conditions, making moisture control challenging. By employing these electrodes, welders not only maintained structural integrity but also adhered to the timeline and safety standards, validating their indispensable role in modern welding.
In conclusion, 7018 low hydrogen electrodes epitomize the blend of advanced material science and practical welding expertise. Their utilization not only elevates the standard of welds produced but also instills confidence in the structural robustness. For industry professionals seeking to amplify their productivity and weld quality, these electrodes remain a cornerstone of effective welding solutions.