Comprehensive Guide to 6013 Welding Rod Sizes Expert Insights and Best Practices
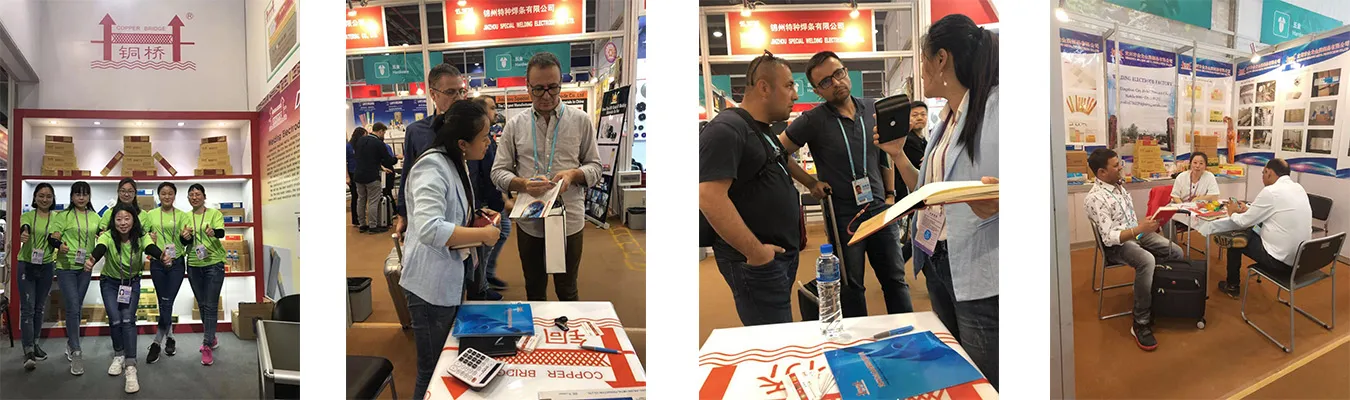
When it comes to welding, choosing the right electrode is crucial for achieving optimal results.
Among various types of welding rods, the 6013 welding rod stands out due to its versatility and user-friendly nature. This article delves into the specifics of 6013 welding rod sizes, drawing from extensive experience and expertise to provide a definitive guide.
Understanding 6013 Welding Rods
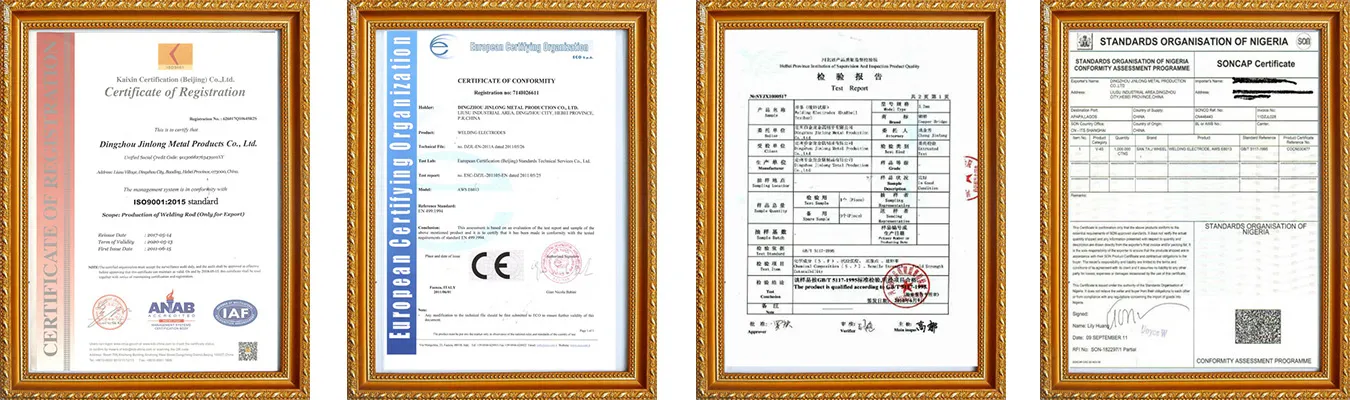
The 6013 welding rod is widely recognized within the welding community for its smooth arc performance and ease of use. It is an all-position, general-purpose rod suitable for both hobbyists and professionals. The '60' in its designation signifies a minimum tensile strength of 60,000 psi, while '1' indicates that it is an all-position rod. The final digit '3' identifies the type of coating and current used.
Insights from Experience
Drawing from years of fieldwork, welders consistently appreciate 6013 rods for their forgiving nature during welding sessions. They are particularly popular in thin metal welding, where precision is key. The rods are easily manageable for both seasoned professionals and beginners tackling their first projects. The flux coating allows for easy arc striking and smooth bead appearance, making it an ideal choice for aesthetic welds on sheet metal and thin-walled tubing.
Exploring the Sizes of 6013 Welding Rods
Welding rods, including the 6013, come in various sizes, directly influencing the amperage range they support and their suitability for different thicknesses of metal. Common sizes include 1/16 inch, 5/64 inch, 3/32 inch, 1/8 inch, 5/32 inch, and 3/16 inch.
1. 1/16 inch and 5/64 inch Ideal for thin sheet metal and precision welding tasks. These sizes require lower amperage settings and provide excellent control, reducing the risk of burn-through.
6013 welding rod sizes
2. 3/32 inch The most versatile size, suitable for a wide range of applications. It offers a good balance of penetration and deposition, making it perfect for light to medium gauge metals.
3. 1/8 inch Preferred for thicker metals up to approximately 1/4 inch. With robust deposition rates and deeper penetration, this size is a staple in heavier fabrication work.
4. 5/32 inch and 3/16 inch Utilized for heavy industrial applications and thicker sections of steel, requiring higher amperage and generating more heat to ensure proper fusion.
Professional Insights and Authoritative Guidance
In professional environments, selecting the right 6013 rod size involves assessing the material thickness, joint type, and desired weld characteristics. Expert welders advocate for starting with test welds to fine-tune amperage settings, ensuring that the bead profile and penetration depth align with project specifications. Authorities in welding standards emphasize the compatibility of 6013 rods with AC and DC power sources, offering flexibility in equipment choice.
Trustworthy Practices for Optimal Results
To achieve the best results with 6013 welding rods, maintaining rod quality is pivotal. Store rods in a dry environment to prevent moisture absorption, which can lead to hydrogen-induced cracking. Additionally, regular cleaning of the base metal and ensuring proper fit-up can drastically improve weld quality and reduce defects.
Conclusion
Navigating through the array of 6013 welding rod sizes requires an understanding of their unique characteristics and benefits. This guide consolidates expertise and real-world experience, providing a reliable resource for welders looking to optimize their projects. Whether working on intricate hobby projects or robust industrial applications, the 6013 welding rod proves to be a valuable tool in any welder’s arsenal.