Understanding the intricacies of welding requires a good grasp of the tools at your disposal. One key component that often puzzles both novice and experienced welders is the appropriate amperage for different welding rods. Particularly, the 5/32 inch welding rod is frequently used in various industrial and personal welding projects. This guide provides a comprehensive look at how to optimize amperage settings for these rods, enhancing your welding results through expert insights and reliable data.
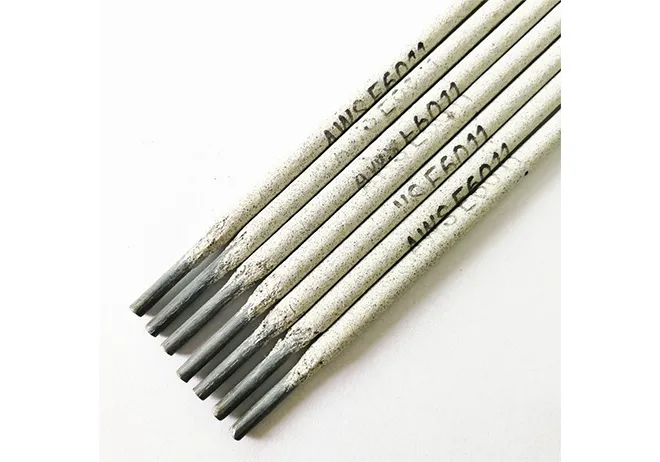
Selecting the correct amperage for the 5/32 welding rod is vital to achieve the desired weld penetration, bead uniformity, and material fusion. Typically, the 5/32 welding rod is used for medium to heavy-duty tasks, supporting materials such as carbon steel, stainless steel, and sometimes cast iron. Understanding the appropriate amperage settings not only improves the quality of your welds but also extends the longevity of your welding equipment.
The first step to mastering your amperage settings is knowing your welding environment and the specifics of your materials.
The 5/32 inch welding rod usually requires a range of 110 to 180 amps. However, the exact amperage depends on several factors, including the type of base material, the welding position, and the desired welding speed. For instance, welding in a flat position allows slightly higher amperage, but when tackling overhead or vertical positions, it's advisable to reduce amperage to prevent weld metal from dripping.

Equally important is the consideration of how electrode type affects amperage needs. The most common 5/32 rods, such as E6010 or E6011, each have distinct characteristics. The E6010 is renowned for its deep penetration and is well-suited for root pass applications in pipe welding, typically requiring a higher amp setting within the range. Conversely, E6011 is adaptable to different power supplies and situations, often performing better at slightly lower amp levels due to its cellulose-based flux coating.
Beyond the technical specifications, real-world practice reveals additional insights. Welders with years of field experience highlight the critical balance between adequate penetration and control over spatter. During field operations, adjustments in amperage are often necessary as conditions such as ambient temperature, humidity, and weld material thickness shift. Expert welders recommend setting up test welds on scrap material before engaging in critical projects to fine-tune the amperage.
5 32 welding rod amperage
Furthermore, expert-level understanding encompasses not just ideal amperage but also welding techniques. Proper electrode manipulation plays a significant role in managing heat input and achieving optimal weld quality. Techniques such as stringer beads or weaving affect how heat spreads along the weld path and should be considered when setting up your equipment, highlighting the need for comprehensive training and practice to perfect these methods.
Authoritative guidance from industry professionals emphasizes regular maintenance and inspection of welding equipment, especially when frequently changing amperage settings. Ensuring that cables are in good condition, connections are secure, and machines are regularly calibrated can prevent common issues like inconsistent arc stability or overheating, which tend to occur with neglect.
Trust in your equipment and skills is bolstered by continuous learning and adaptation of best practices. Informative resources, such as manufacturer manuals and certification courses, help welders stay abreast of new technologies and methodologies. This, combined with field experience and a willingness to experiment within safe parameters, fosters a credible and authoritative approach to welding tasks.
While the 5/32 welding rod's amperage settings might pose challenges, they are surmountable with informed strategies and a proactive mindset. Expert welders know that success in welding is a balance of art, science, and skill, all underpinned by a thorough understanding of the tools and materials at hand. By maintaining a focus on meticulous preparation and continual learning, welders can produce high-quality, reliable welds that stand the test of time.