The fascinating world of welding opens its doors to myriad possibilities for crafting and fixing metal structures. One of the most sought-after components in TIG (Tungsten Inert Gas) welding is the 5/32 TIG rod. This vital component is the unsung hero in creating robust and precise welds for both hobbyists and professional welders. An exploration into this particular size of TIG rod reveals its unique applications, benefits, and usage tips that can enhance your welding projects profoundly.
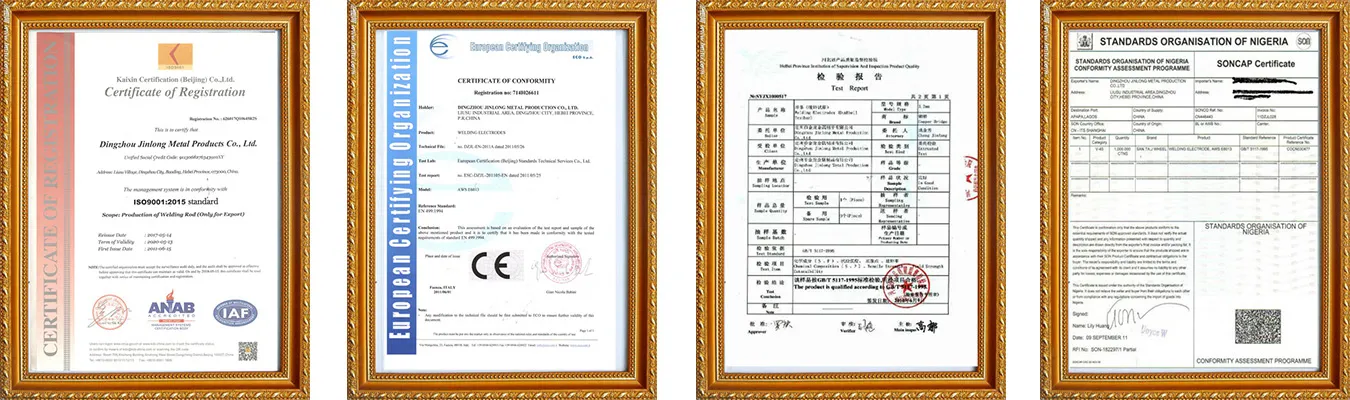
The 5/32 TIG rod, being larger compared to other rod sizes, serves a distinctive purpose in the welding ecosystem. It is often the preferred choice for heavy-duty applications where structural integrity is not just important, but essential. Welders working with thicker materials like heavy steel or aluminum find this rod size indispensable for its capability to deposit more filler material quickly. This rod size is particularly beneficial in industries such as automotive manufacturing, heavy machinery repair, and shipbuilding where the strength of the weld is paramount.
Experience plays a crucial role in fully leveraging the advantages of the 5/32 TIG rod. Experienced welders appreciate its ability to provide a stable arc with sufficient filler metal, leading to stronger, more reliable joints. The process requires a nuanced understanding of heat control to prevent burn-through, especially given the thickness of materials involved. Sharing personal experiences, welders have found that striking the right balance with current settings and travel speed is vital for optimal weld quality. With its heavy-duty nature, the rod helps to achieve deeper penetration which is critical in ensuring that the weld does not fail under stress.
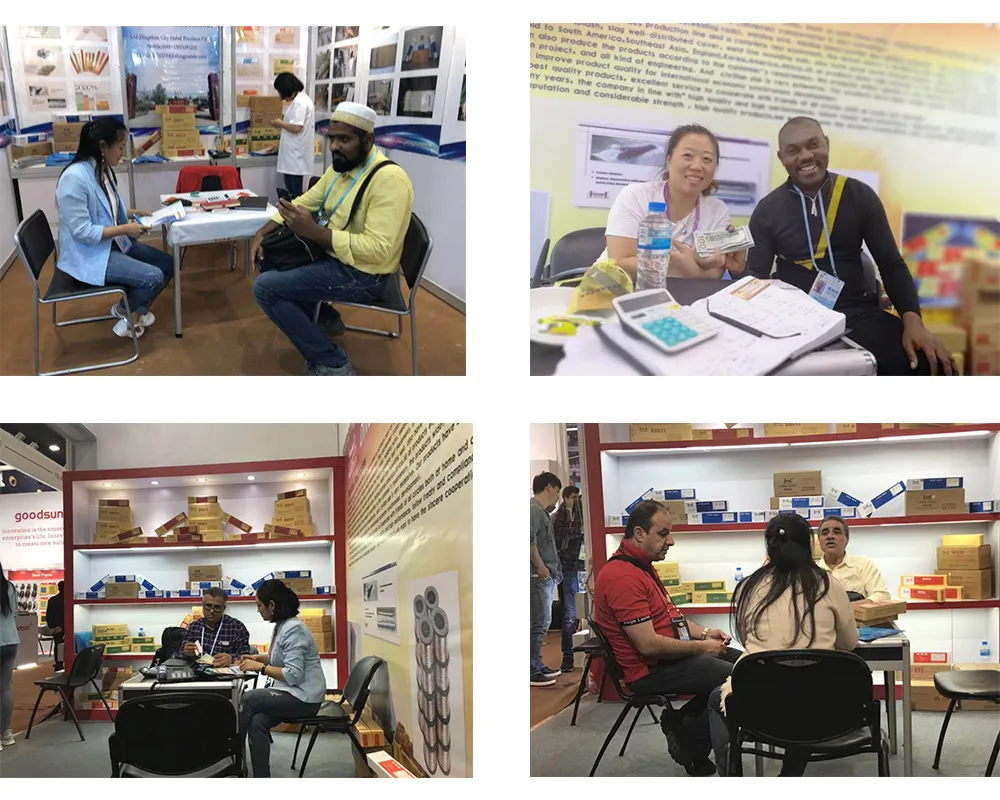
From the expertise perspective, the 5/32 TIG rod appeals to professionals who demand not just a tool, but a partner in their craft.
Understanding the properties of the metals being joined is essential. This rod works exceptionally well with metals such as stainless steel, where corrosion resistance and durability are crucial. Welders familiar with metallurgical principles can leverage the specific composition of the 5/32 TIG rod to complement the properties of the base metals, ensuring that the weld is not a weak point.
5 32 tig rod
On the front of authoritativeness, manufacturers provide detailed specifications about their 5/32 TIG rods which users should diligently review. Factors such as the alloy composition, melting temperature, and tensile strength are crucial to making informed choices for specific applications. Authority figures in welding, such as product engineers and seasoned professionals, often highlight the importance of selecting the right rod size and type based on the precise requirements of the project.
Trustworthiness in using the 5/32 TIG rod comes from the assurance of consistency and quality in its performance. Leading brands offering these rods maintain stringent quality controls and standards. Welders need to be mindful of purchasing from reputable sources to avoid inferior products which may lead to poor weld quality and potential structural failures.
In achieving the highest standard of welding integrity, utilizing the 5/32 TIG rod effectively requires a combination of skills, knowledge, and reliable resources. Practical tips for success include preheating thicker materials to aid in even heat distribution and minimizing contamination by keeping the work environment and materials clean. Additionally, proper equipment maintenance, such as ensuring that the TIG torch setup is optimal, plays a critical role in achieving consistent results.
The real-world applications and benefits of the 5/32 TIG rod reaffirm its standing as an indispensable tool within the welding community. Whether you are involved in complex industrial applications or meticulous, intricate projects, the rod’s ability to foster strong, precise, and durable welds cannot be overstated. As the gateway to achieving welding excellence and craftsmanship, the insights derived from industry experience, combined with expert advice and reliable product quality, form the bedrock of successful welding endeavors.