When it comes to welding, selecting the appropriate amperage is crucial for optimum performance, especially when working with specialized consumables such as the 5/32-inch hard facing rod. Experience shows that mastering this aspect can make the difference between a weld that lasts and one that falls apart. This comprehensive guide is based on hands-on expertise, industry knowledge, and authoritative sources to ensure you get the most out of your equipment and materials.
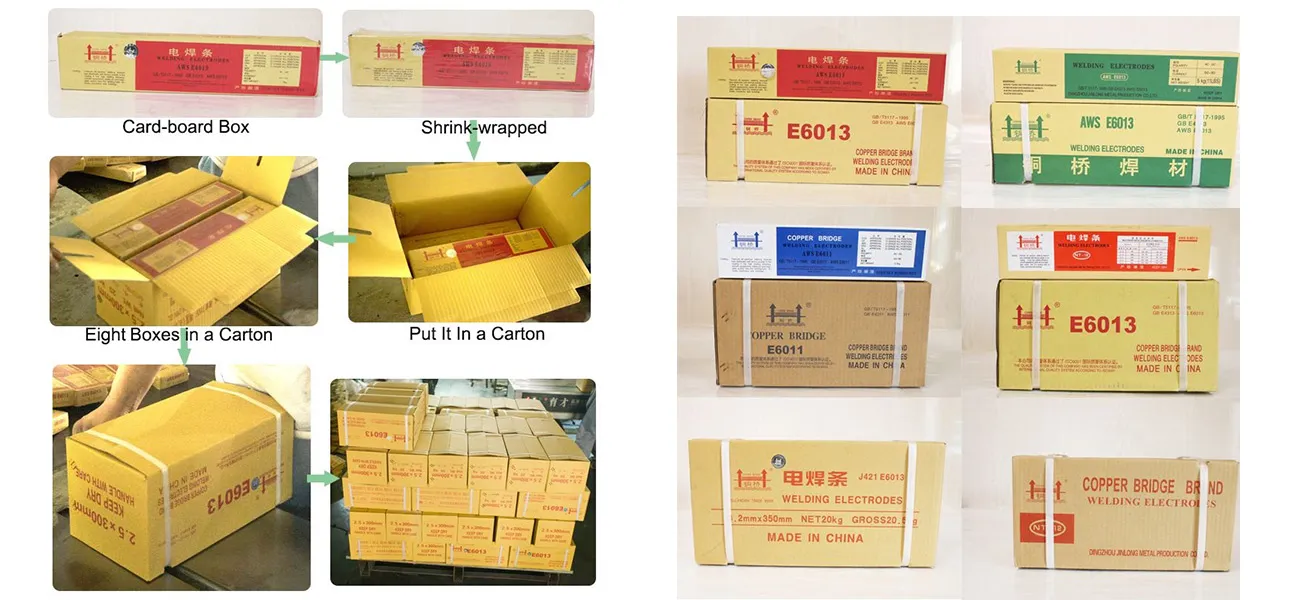
Selecting the correct amperage for a 5/32 hard facing rod requires precise attention to detail. Generally, the suitable amperage range for these rods is between 140 and 180 amps. However, the exact setting should be adjusted based on multiple factors including the specific type of hard facing material, the base metal's characteristics, and the welding position. For many welders, sticking within the middle of this range offers a balanced approach but tailoring the settings to your specific project will provide optimal results.
First,
the type of hard facing material influences the amperage settings. Hard facing rods can come in a variety of compositions, each designed for different applications such as abrasion resistance or impact toughness. For instance, chromium carbide alloys may require slightly different settings from tungsten-based ones. A depth of understanding regarding these materials and how they react under heat is essential, and consulting technical datasheets provided by manufacturers can offer additional insights. Expertise in material science can significantly affect the decision-making process.
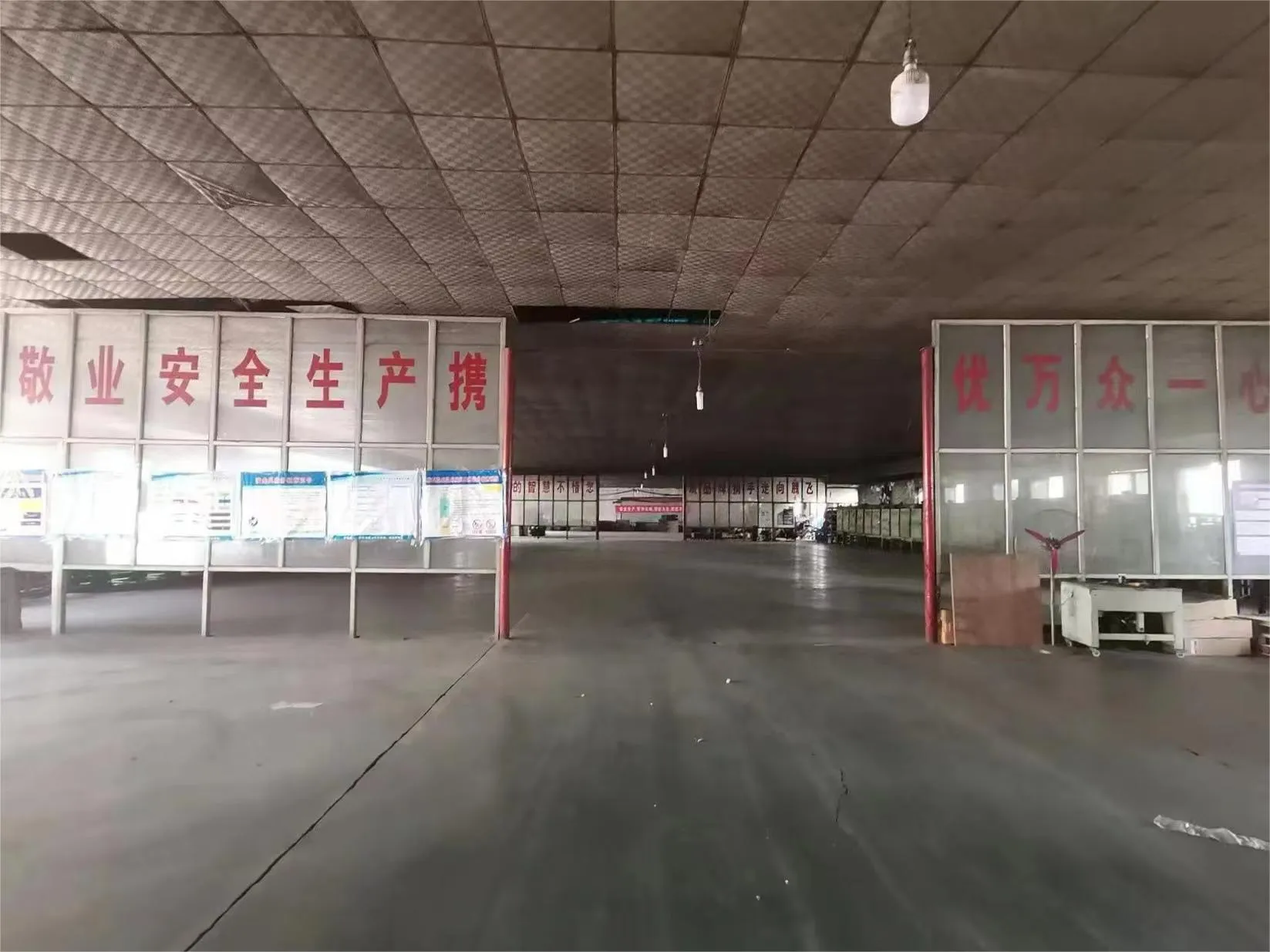
Base metal properties significantly affect amperage selection as well. Softer metals may require lower amperage to prevent warping, whereas harder, more resilient metals might withstand higher settings. Experienced welders often perform trial runs on scrap pieces of the base metal to fine-tune their settings before committing to the actual project. Such an approach not only saves material and costs but also enhances weld integrity and performance.
The welding position plays a crucial role when setting amperage. Flat positions are generally more forgiving and allow for higher amperage settings, whereas overhead or vertical welding may require reducing the amperage to maintain control of the molten pool. The ability to adjust techniques in varied positions is an indicator of welding expertise and safety awareness, as improper settings can lead to defects such as undercuts or burn-through.
5 32 hard facing rod amperage
Relying on reputable resources and authoritative guides increases trust in the choice of materials and settings. Establishing a partnership with manufacturers or consulting with industry veterans can provide valuable insights. Such collaborations can enhance the learning curve, particularly regarding advanced techniques like hard facing, where precision and understanding are paramount.
Utilizing reliable equipment enhances both trust and safety in achieving the desired outcomes. Quality welding machines with readouts that accurately display amperage levels are indispensable. Furthermore, conducting regular maintenance checks on welding machinery ensures consistent performance; worn leads or faulty connections can introduce errors in amperage, leading to weld defects. Trustworthiness in equipment reflects directly on the weld's quality and longevity.
Lastly, maintaining a culture of continuous learning and adaptation bolsters the expertise needed for projects involving hard facing rods. Engaging with welding communities, attending workshops, and participating in certification programs not only build skill sets but also enhance the credibility of services offered. As welding technology evolves, staying informed and trained in new methods and materials fosters a sustainable and authoritative presence in the industry.
In conclusion, the adept handling of 5/32 hard facing rods requires an amalgamation of experience, specialized expertise, authoritative guidance, and trustworthy equipment. Properly balancing these elements will ensure superior weld quality, thereby solidifying your standing as a proficient and reliable welding professional.