Understanding the correct amperage for a welding rod is crucial for achieving optimal results in welding projects, especially when dealing with the 1/8 inch (3.2 mm) electrodes. This article delves into the technical intricacies of using a 1/8 inch welding rod, offering insights grounded in expert experience and backed by authoritative references.
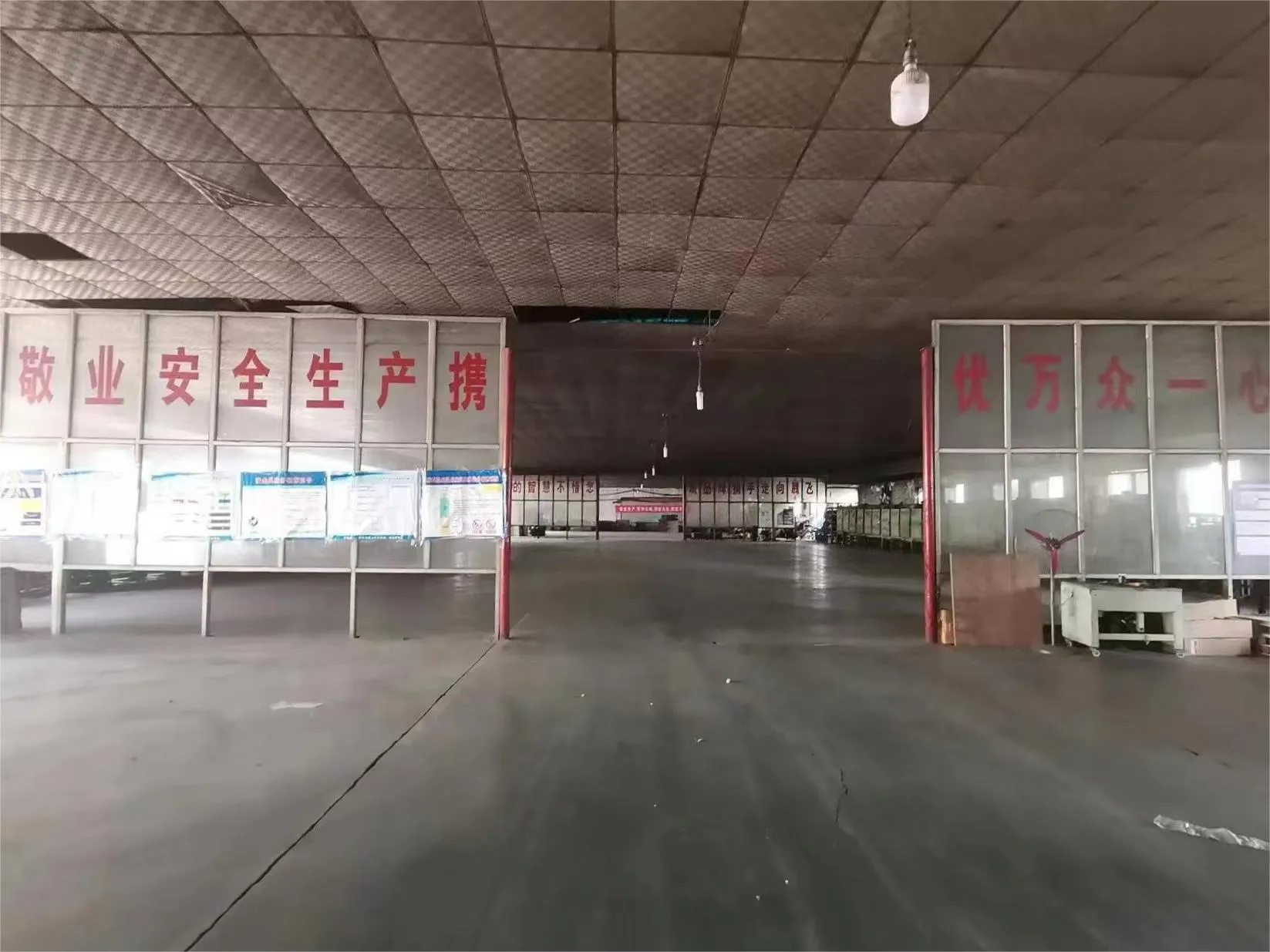
When embarking on a welding project, selecting the appropriate amperage is paramount. Too little amperage results in a weak weld, while too much can lead to burn-through and imperfections. The 1/8 inch welding rod is a popular choice among welders for its versatility, used widely in structural work and projects requiring substantial metal thickness.
For those venturing into the use of a 1/8 inch welding rod, understanding its amperage range is key. Typically, the optimal amperage setting for a 1/8 inch electrode falls between 90 to 140 amps. However, it's critical to understand that this range is not absolute—several factors influence the precise amperage needed. The type of metal, the welding position, and the desired penetration all play a role.
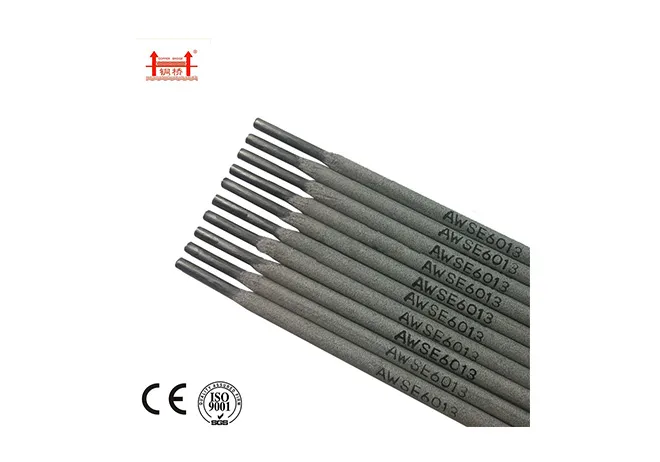
An expert welder will tell you that welding steel with a 1/8 inch rod requires a refined balance. For instance, welding on horizontal or flat positions often necessitates a lower amperage within the range, such as 90 to 110 amps, allowing for a controlled bead without excessive heat input. In contrast, overhead or vertical positions might need higher settings nearing the upper limit of 140 amps to counteract gravitational effects and ensure proper penetration.
Different welding machines also influence the required amperage settings. Notably, an AC machine might function optimally at the lower end of the amperage scale compared to a DC machine. This is because AC current requires less heat to produce a stable arc with a 1/8 inch rod compared to DC, which tends to be smoother and more stable but demands higher energy.
Moreover, the type of coating on the electrode impacts amperage requirements. For example, electrodes with a cellulose coating are suited to high penetration and fast-freezing conditions, which can reduce the necessary amperage. Conversely, low-hydrogen rods, known for producing high-quality welds with minimal splash, typically require settings closer to the upper amperage limit to maintain a stable arc.
1 8 welding rod amperage
For professional welders aiming for precision and high-quality output, the depth of weld penetration and bead appearance are critical. The ideal amperage ensures not just strength, but the aesthetic quality of the weld bead. Poor settings result in uneven, brittle, or aesthetically unpleasing welds, indicating insufficient heat or excess spatter due to excessive current.
To promote trustworthiness and authoritative guidance, referencing manufacturer data and welding industry standards is vital. Leading electrode manufacturers like Lincoln Electric or ESAB provide detailed amperage guidelines readily available for most of their products. Following these specifications ensures that your practices align with industry standards, guaranteeing not just success but also safety.
Additionally, practical workshops and consultations with certified welding experts provide learning experiences that cannot be substituted by online tutorials. Engaging with professionals who operate in industrial settings offers exposure to real-world applications of these amperage guidelines.
Finally, establishing a routine of proper maintenance and calibration of welding equipment impacts the effective use of a 1/8 inch rod. Regular scheduler checks and calibrations enhance machine performance, promoting consistent outputs at selected amperages. This upkeep fosters reliability, a critical component in delivering quality work.
Through practiced application, adherence to detailed industry standards, and an understanding of the influencing variables, mastering the optimal amperage for a 1/8 inch welding rod transforms novice efforts into professional-grade welding excellence.