When it comes to welding, a crucial component in ensuring the quality and durability of the metalwork is the welding rod utilized. Among the various types available, the 7018 welding rod stands out for its versatility and reliability. This article delves into the unique characteristics of 7018 rods, their applications, and the experiences of seasoned welders who swear by their performance.
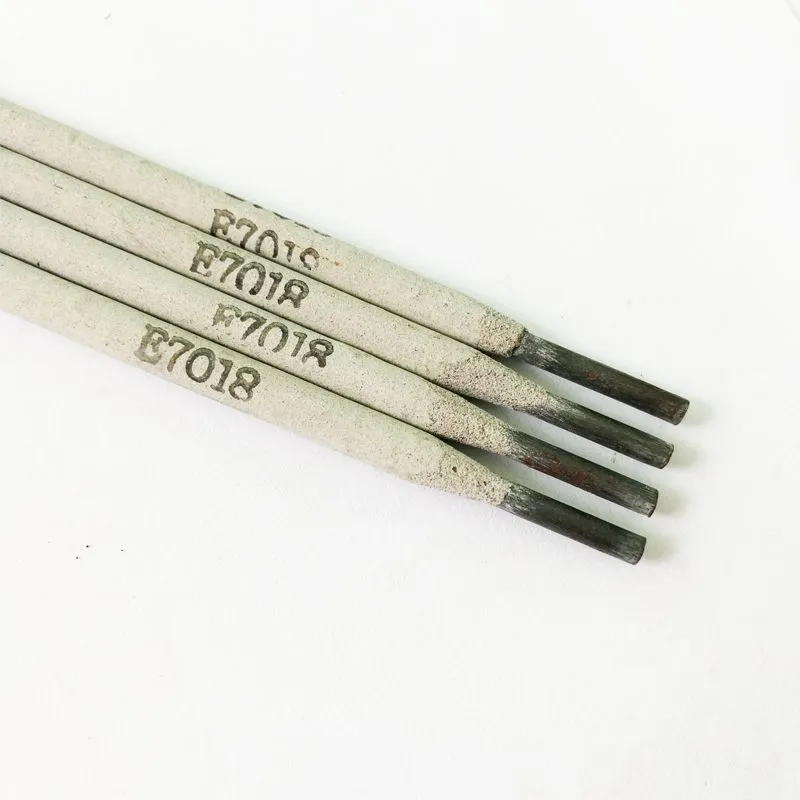
The 7018 welding rod, often referred to as a low-hydrogen electrode, is renowned for its exceptional tensile strength and elongation properties, making it suitable for a wide range of industrial applications. With a strength of 70,000 psi, these rods are engineered to handle substantial stress, ensuring a robust weld on critical structures like bridges, high-rise buildings, pipelines, and pressure vessels. This characteristic empowers industry professionals to maintain high safety standards and meet rigorous quality specifications.
A unique feature of the 7018 welding rod is its ability to produce a smooth, aesthetically pleasing weld that requires minimal post-weld cleanup. The flux coating on these electrodes generates a protective gas shield and slag coverage during welding, both of which contribute to the excellent appearance of the finished weld. This results in significant time savings and increased efficiency, as the need for extensive refinishing is minimized.
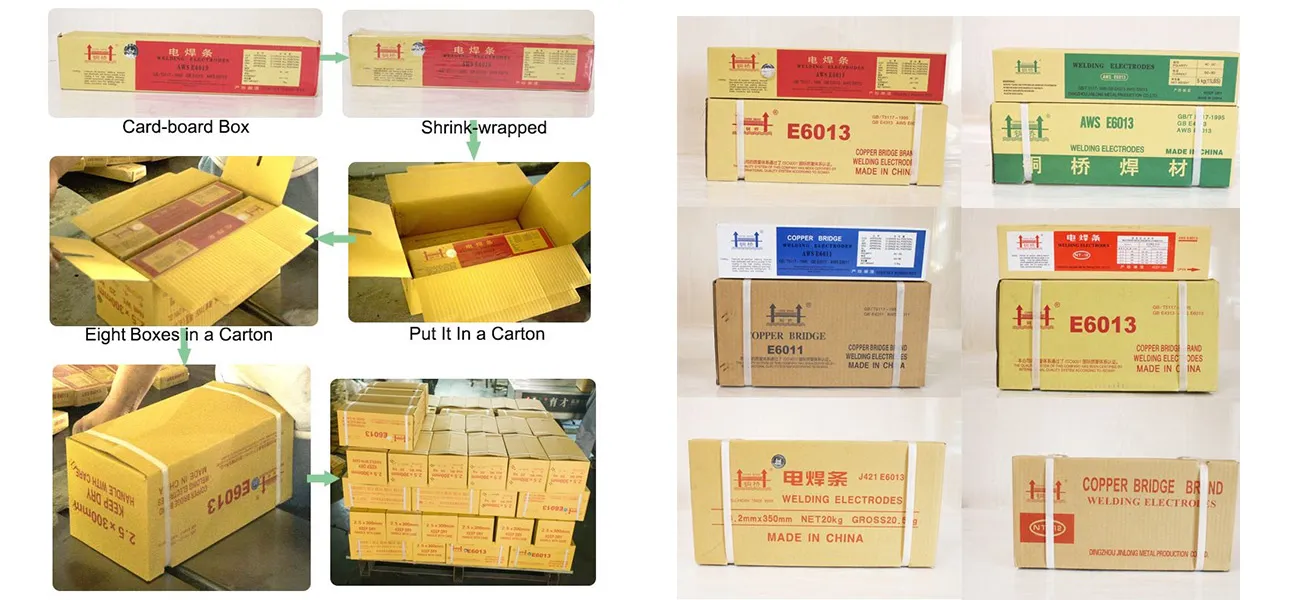
For welders, maintaining a consistent arc is paramount for achieving optimal results. The 7018 rod is celebrated for its stable arc, providing welders with better control and precision, even in less-than-ideal environments. This stability is attributed to the low moisture content of the electrode coating, which reduces the risk of hydrogen-induced cracking — a common issue that can compromise the integrity of the weld. By using 7018 rods, welders can achieve greater assurance in the quality and longevity of their work.
The professionalism involved in using 7018 rods extends to their storage and handling. These electrodes require specific care to preserve their low-hydrogen properties. They must be stored in a dry environment, often in an electrode oven, to prevent moisture absorption. Industry experts recommend re-baking the rods in an oven set at temperatures between 500°F to 800°F if any exposure to moisture occurs. While some might view this as an inconvenience, experienced welders recognize it as a necessary step to ensure the highest quality welds.
1 8 welding rod 7018
One experienced welder, John H. from Texas, shares his insights Using 7018 rods has been a game-changer in my welding projects. The stability and clean finish they provide have elevated the standard of my work, especially in structural applications where safety and reliability are non-negotiable. Investing in proper storage solutions has paid dividends by preventing defects and rework.
The expertise and authoritative insights of welding professionals continually highlight the 7018 welding rod's role as an industry staple. It is endorsed by certification bodies such as the American Welding Society (AWS) and is compliant with industry specifications, reinforcing its position as a go-to electrode for critical welding tasks.
Moreover, an emerging trend in welding practice involves integrating technology with traditional methods. Innovative welding machines equipped with advanced settings specifically for 7018 rods are available, allowing welders to optimize settings dedicated to the nuances of these electrodes. Such technology advancement reflects an increased focus on efficiency and quality, aligning perfectly with the attributes of the 7018 rods.
In conclusion, the 7018 welding rod remains a pillar of welding excellence across various sectors. Its superior strength, reliable arc, and visually appealing results make it an indispensable tool for professional welders committed to quality and safety. The emphasis on proper storage and handling techniques further underscores its significant role in achieving incredible welds that stand the test of time. By leveraging their expertise with the right technology and maintaining diligent practices, welders can fully realize the potential of 7018 rods in delivering unparalleled outcomes.