Choosing the right amperage for welding with a 7018 rod is paramount for achieving high-quality welds, especially when dealing with critical applications. Understanding the intricate dynamics of welding with the 7018 electrode requires a blend of personal experience, professional expertise, authoritative knowledge, and a trustworthy approach to deliver the best outcomes every time.
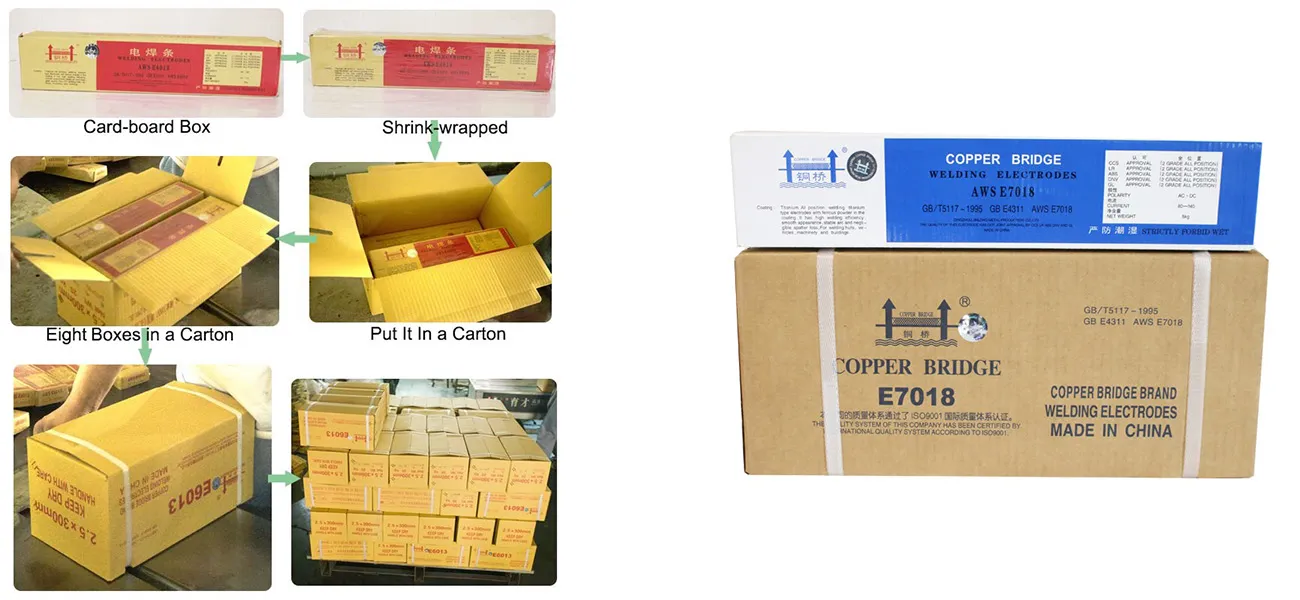
The 7018 welding rod is a low-hydrogen electrode, prized for its ability to produce welds with high tensile strength and ductility. These characteristics make it a favorite for welding carbon and low-alloy steels, where the elimination of moisture is critical to avoid hydrogen-induced cracking. For those seeking to optimize their welding projects, understanding how amperage settings affect the outcomes when using a 7018 rod is a crucial step.
Experience plays a significant role in mastering the art of welding with the 7018 rod. Many seasoned welders share that, through trial and error, they have found the ideal amperage ranges for different scenarios. For example, a 1/8-inch 7018 rod typically requires an amperage setting between 90 to 160 amps, but this can vary based on the position of the weld, the material's thickness, and the specific project requirements. Novice welders may begin at a mid-range setting and adjust higher or lower based on the feel and appearance of the weld bead. This hands-on approach helps refine skills as welders notice how subtle changes in amperage affect penetration and bead formation.
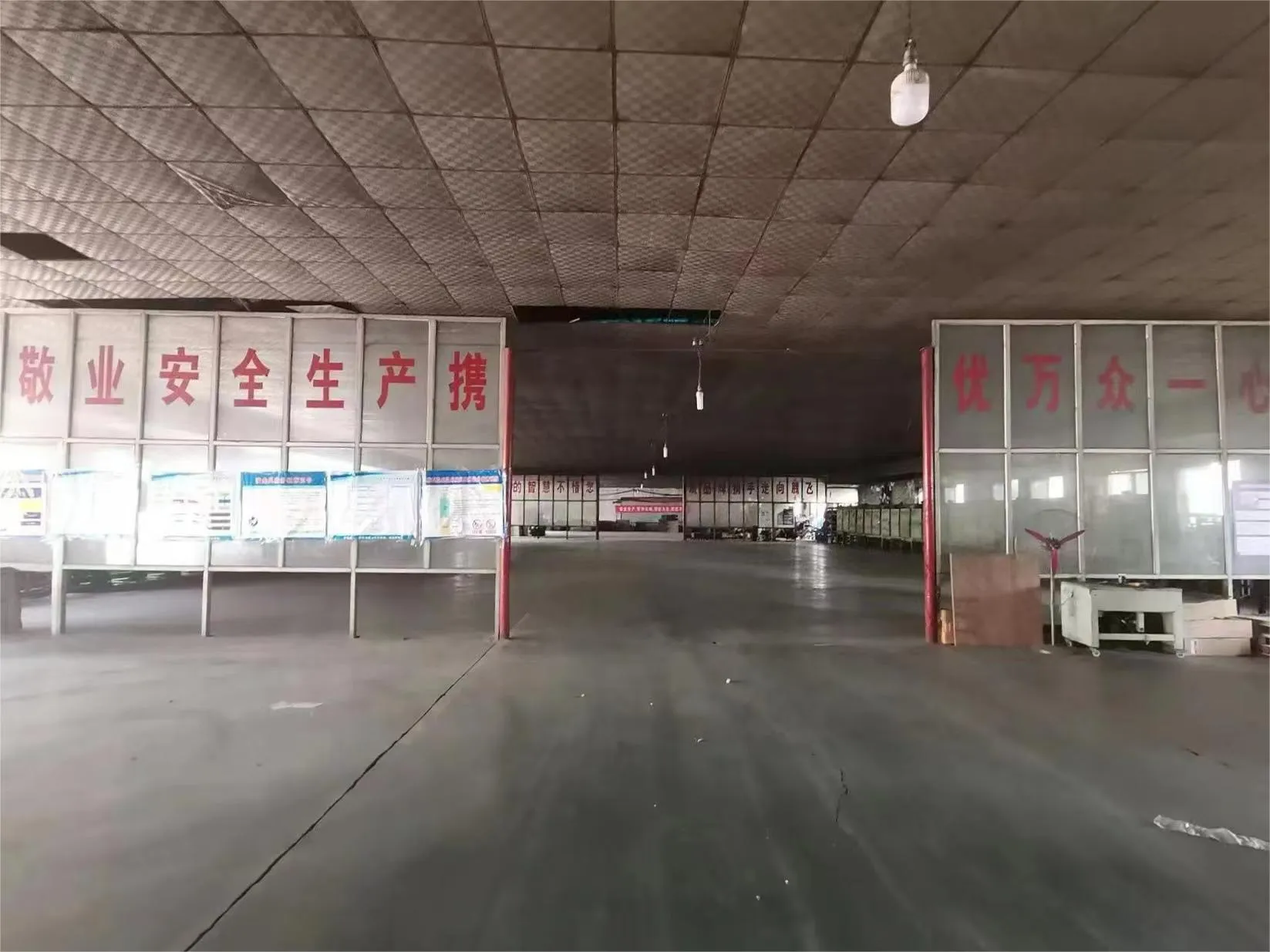
In terms of expertise, knowing the technical specifications of the 7018 electrode and matching them with suitable amperage ranges can dramatically enhance the welding process. The coating of the 7018 rod contains a chemical composition that requires a higher starting amperage to initiate arc stability. Typically, a slightly higher amperage is needed compared to other rods like the 6010 or 6011, as 7018 demands sufficient heat to create a smooth, strong arc and prevent sticking to the workpiece. The rod's coating also influences the bead, making it crucial to keep the rod dry and handle it appropriately. Any moisture retained can disrupt the amperage settings and compromise the weld quality.
1 8 welding rod 7018 amperage
Authoritativeness in the realm of welding with a 7018 rod comes from backing choices with specifications from reputable sources like the American Welding Society (AWS). These standards recommend benchmark amperage settings and provide guidelines for various welding processes, ensuring welders align their practices with tested and verified data. For instance, AWS standards advise that for vertical or overhead welding positions, amperage might need to be adjusted slightly downwards to prevent excessive heat that can cause molten metal to drip and result in poor bead control.
Trustworthiness is built through consistency and reliability in applying welding techniques. For professionals and hobbyists alike, ensuring that their welding equipment is well-maintained and calibrated to deliver accurate amperage settings is fundamental. Many experienced welders emphasize the importance of keeping electrodes dry, since moisture can alter their effective performance by impacting how amperage is transferred through the rod. Moreover, investing in high-quality electrodes and equipment that provide stable arc performance can dramatically influence the success of the welding process.
Lastly, the convergence of experience, expertise, authoritativeness, and trustworthiness equips welders to experiment safely while exploring optimal settings tailored to their specific projects. Documenting alterations in amperage settings and their correlation to weld quality creates a valuable resource that bolsters professional development and cultivates a deeper understanding of how to manipulate welding variables.
In conclusion, selecting the right amperage for a 1/8-inch 7018 welding rod transcends basic settings and delves into a holistic understanding of weld dynamics. The amalgamation of field experience, technical know-how, compliance with authoritative standards, and a steadfast commitment to best practices will guide welders in producing quality welds. Whether it’s structural work or delicate repairs, mastering the amperage requirements for the 7018 rod is essential, empowering welders to undertake ambitious projects with confidence and precision.