Selecting the right welding rod is integral to achieving the perfect weld, and among the vast array of options, the 1/8 welding rod holds particular prominence for both professionals and hobbyists. Its functionality, versatility, and efficiency make it a preferred choice in numerous applications. Here, we dissect the reasons behind its popularity and provide insights into making the best use of this welding rod.
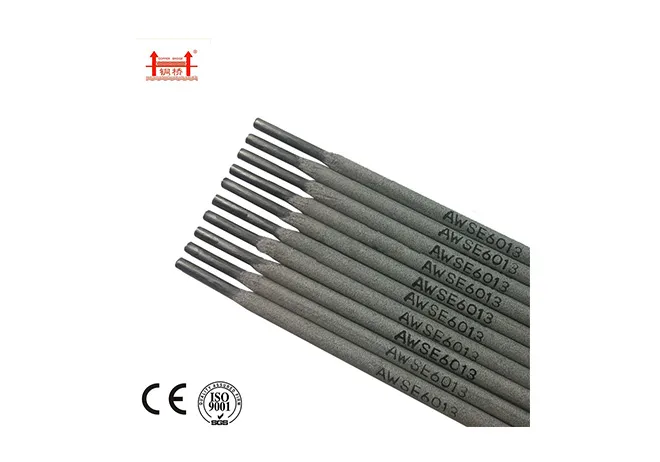
A 1/8 welding rod, often referred to as a workhorse within the welding community, is heralded for its optimum size, allowing it to handle a wide variety of welding tasks with efficiency. One of the fundamental characteristics of the 1/8 welding rod is its excellent amperage range—usually between 70 to 130 amps—which makes it incredibly versatile in handling different thicknesses of metal. This particular size strikes a balance, allowing for both detailed work on thinner metals and structural integrity on thicker pieces.
Expert welders often choose the 1/8 welding rod when working on projects that require precision and strength. The size of the rod is convenient for creating strong, sound joints in both ferrous and non-ferrous metals. Whether crafting an intricate metal sculpture or constructing robust steel frameworks, the 1/8 welding rod delivers consistency and reliability.
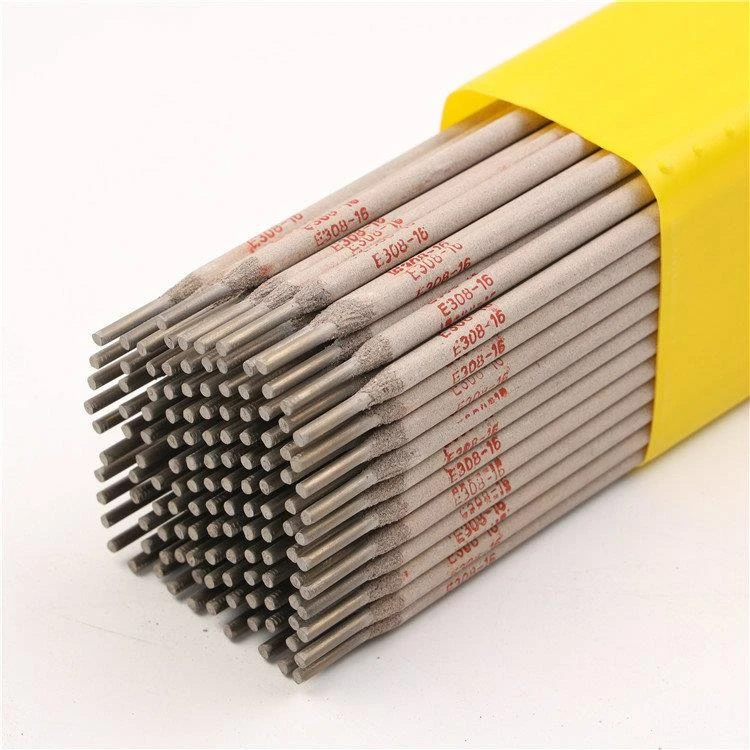
A real-world experience shared by welding experts is related to its skill enhancement potential. Beginners can greatly benefit from the manageable size and forgiving nature of the 1/8 welding rod. It allows for a smoother welding experience, decreases the likelihood of common mistakes such as undercutting or lack of fusion, and ultimately builds confidence for novice welders. From an expert standpoint, having a reliable rod like the 1/8 size in the toolkit is invaluable due to its adaptability across various welding positions, whether horizontal, vertical, or overhead.
The expertise dimension of choosing a 1/8 welding rod delves into its suitability for different types of welding processes. Whether performing Shielded Metal Arc Welding (SMAW), Gas Metal Arc Welding (GMAW), or Flux-Cored Arc Welding (FCAW), this rod performs exceptionally well. Particularly in SMAW, often referred to as stick welding, the 1/8 rod is a staple due to its capability to withstand differing electrical currents and maintain thermal balance, ensuring quality welds even under conditions that are less than ideal.
1 8 welding rod
Furthermore, the coatings on 1/8 welding rods have evolved to improve performance outcomes. Whether it's cellulose, rutile, or basic coatings, each variation can dramatically affect arc stability, penetration depth, and the final appearance of the weld. Professional welders often recommend testing various coated 1/8 rods to determine the best performance for specific projects, a practice that enhances both expertise and the final product quality.
From an authoritative stance, leading manufacturers of welding rods, such as Lincoln Electric and ESAB, have consistently underscored the importance of the 1/8 size in their product lines. These companies invest heavily in testing and development, ensuring that the 1/8 welding rods produced under their brands meet rigorous standards of reliability and excellence. Reviews and tests from independent welding institutes further reinforce the trustworthiness of the 1/8 welding rod, citing consistent results in weld integrity and operator satisfaction.
Trustworthiness is also a key factor when procuring welding rods. Ensuring that the 1/8 rods are sourced from reputable suppliers minimizes risks associated with inferior material quality, which can lead to weld failures and potentially hazardous situations. Welders are advised to check certifications and standards compliance when purchasing welding rods to guarantee safety and reliability.
In summary, the 1/8 welding rod serves as a quintessential element for successful welding, combining practicality with exceptional performance. Its adaptability across various applications and welding techniques, supported by real-world experience, expertise from professionals, and endorsements from authoritative bodies, illuminates why it remains a dominant choice. Through consistent innovation and rigorous quality assurance, these rods offer a trustworthy tool that meets the diverse needs of the welding industry.