In the realm of metalworking, the welding rod stands as a cornerstone, bridging components with precision and strength. These essential tools, typically composed of various metal alloys, transform under the heat, forming bonds that are critical for structural integrity in a myriad of applications. Many professionals in construction, automotive, and manufacturing fields rely on welding rods not just for their utility, but for their role in ensuring safety and durability.
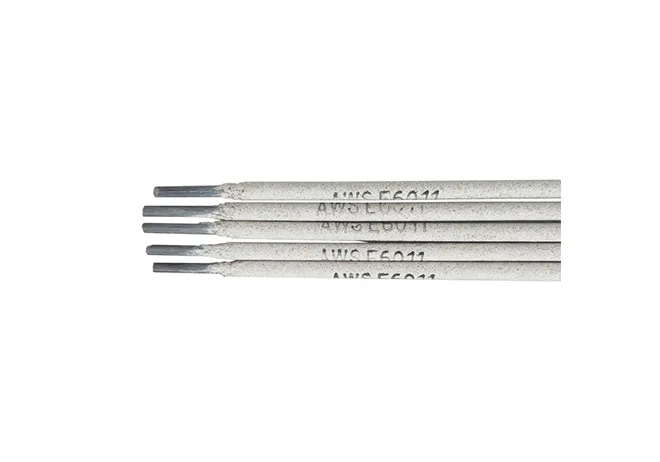
When selecting a welding rod, understanding the types and compatibility with base metals becomes crucial. Common varieties include mild steel, stainless steel, and aluminum, each serving distinct purposes. For instance, mild steel rods are favorable for their versatility in general repairs and maintenance tasks. They often feature in projects where flexibility in the weld is necessary, providing robust connections without being overly brittle.
Stainless steel rods, on the other hand, cater to environments requiring superior corrosion resistance. They are quintessential in the food and chemical industries where cleanliness and durability under acidic or corrosive conditions are paramount. Their unique alloy composition allows welded joints to maintain corrosion-resistant properties, extending the lifespan of equipment and structures.
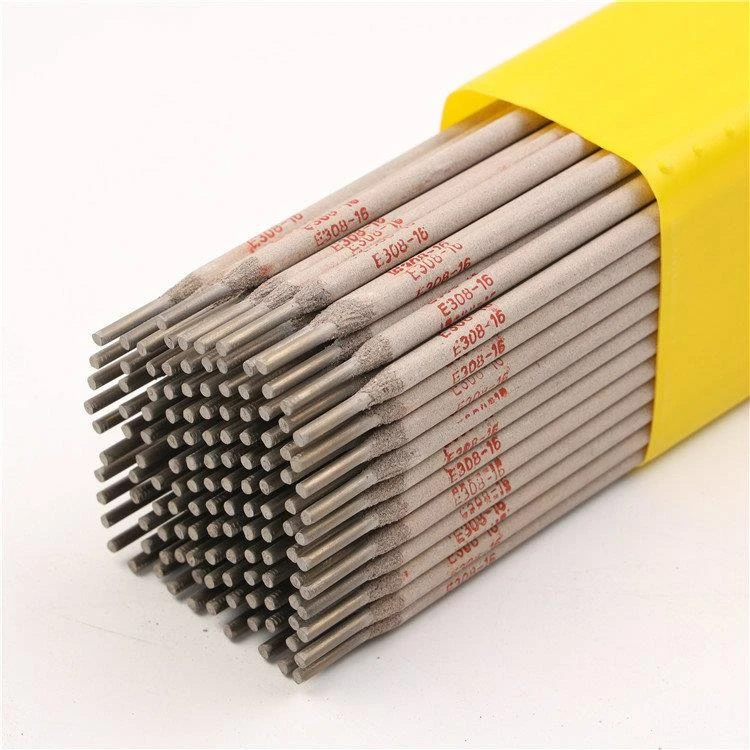
For projects involving lighter materials, such as those found in aerospace or vehicle production, aluminum welding rods are indispensable. These rods offer exceptional tensile strength and a lightweight solution, vital for applications where minimizing weight without sacrificing strength is critical.
Beyond the types, understanding the technical specifications of welding rods enhances project outcomes. Factors like tensile strength, elongation percentage, and impact resistance correlate with the rod’s performance under stress and temperature variations. Mastering these nuances increases the efficacy of the welds, affording both stability and longevity.
welding rod metal
Expert welders emphasize the importance of adhering to best practices during the welding process. Techniques such as maintaining optimal temperatures and controlling the speed of the weld help prevent common issues like porosity or unwanted spatter. Furthermore, utilizing quality welding machines and protective gear significantly influences the weld quality and safety.
Trust in your welding rods is not merely a matter of brand reputation but aligns closely with performance outcomes. Products from esteemed manufacturers undergo rigorous testing and quality control measures, ensuring consistent chemical composition and physical properties. This attention to detail fosters reliability, allowing artisans and engineers to execute projects with confidence.
Sourcing and inventory management of welding rods also play a vital role in operational efficiency. Engaging with suppliers who offer a diverse range of rods, along with expert guidance, can streamline procurement processes, ensuring the right materials are always at hand. This proactive approach minimizes downtime and supports continuous project development.
In conclusion, the welding rod is more than just a tool; it is a symbol of precision and reliability in the metalworking industry. Its significance cannot be overstated, providing an essential function in every welded creation. By understanding the intricacies of welding rod selection, application, and maintenance, professionals not only safeguard the quality of their work but also foster innovation in their industries. Embrace the value of knowledge in welding, where each rod holds the potential to transform raw metal into enduring frames and forms, shaping the future of craftsmanship and engineering.