Welding cast iron using a 7018 rod presents a unique set of challenges, yet it also offers distinct advantages when approached correctly. This type of welding requires careful preparation, a thorough understanding of metallurgical properties, and expert knowledge in adjusting techniques to ensure strong, durable welds.
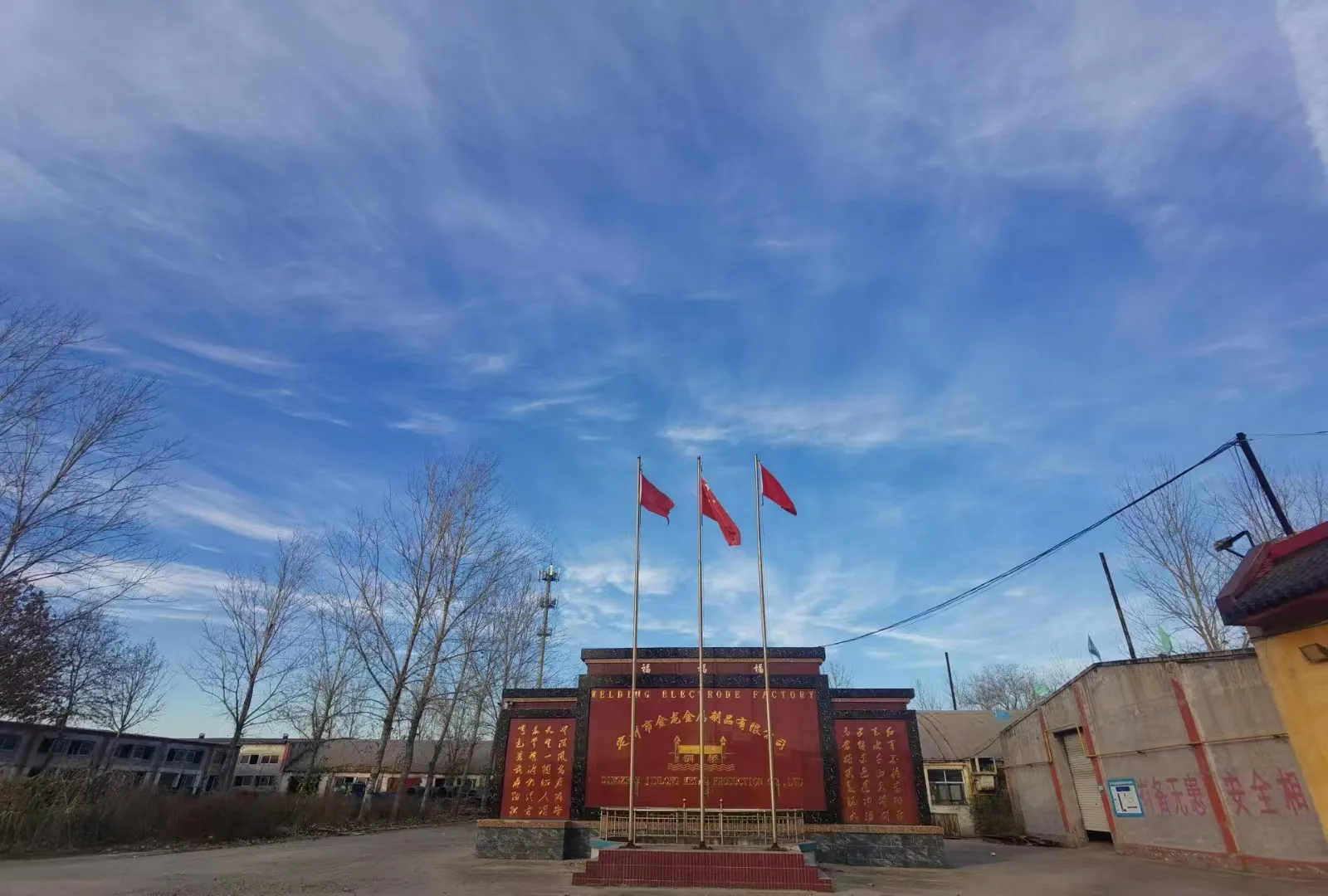
The primary allure of using a 7018 rod for welding cast iron lies in its versatility and stability. While cast iron is notoriously difficult to weld due to its high carbon content, which can lead to cracking, the 7018 rod, typically used for mild steel, provides a reliable alternative when managed with expertise. It requires specific attention to preheating, interpass temperature control, and post-weld cooling procedures.
Experienced welders recognize the importance of preheating the cast iron part. Preheating between 500°F to 1200°F (260°C to 650°C) is crucial, depending on the thickness and complexity of the cast iron. This step reduces the thermal shock applied to the metal and minimizes the chances of cracking. Over the years, professionals have developed an authoritative guideline for preheating based on empirical data and successful projects.
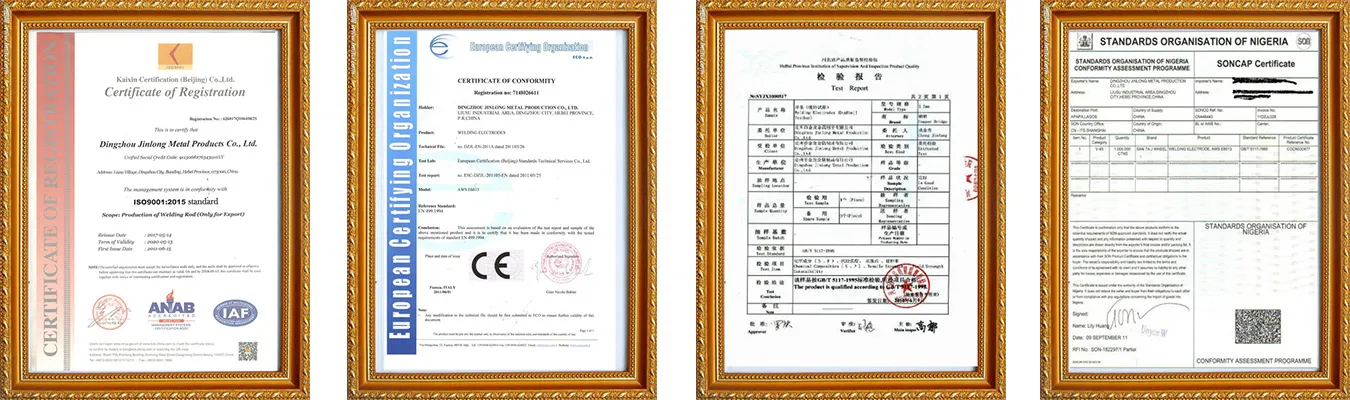
During welding, maintaining a suitable interpass temperature is vital. For 7018 electrodes, a steady hand and control over the arc are necessary to produce a uniform bead. The 7018 rods are renowned for their low hydrogen content, which mitigates the risk of hydrogen-induced cracking—a common issue in welding cast iron. However, this requires the rods to be kept in a controlled environment to prevent moisture absorption, ensuring their effectiveness and trustworthiness in delivering high-quality welds.
Post-welding, the cooling process must be carefully managed. Slow, controlled cooling is recommended to prevent stress and cracking. Wrapping the welded part in insulating blankets or burying it in sand enables gradual cooling and stress relief. This method has been repeatedly endorsed by seasoned professionals who value its reliability.
welding cast iron with 7018 rod
From an expertise perspective, it is crucial to understand why cracks occur and how the 7018 rod helps alleviate these issues. The ductility of the weld metal deposited by the 7018 rod absorbs more stress and allows for minor movements in the weld area, which accommodates the expansion and contraction commonly experienced in cast iron welding.
In terms of equipment and technique, employing a direct current electrode positive (DCEP) setup can improve penetration and fusion, enhancing the weld's integrity. Training and certification in this particular welding process further bolster a welder's credentials, reflecting a deep understanding and authoritative proficiency in managing the complexities that welding cast iron with a 7018 rod involves.
Industry experts also emphasize the importance of verifying weld integrity through non-destructive testing methods, such as ultrasonic testing or radiography, to ensure the welds meet safety standards and performance expectations. Professionals in welding highly value these practices as they contribute to the overall trustworthiness of the technique.
Finally, it is essential to acknowledge that while the 7018 rod provides a versatile solution, a welder’s skill and knowledge remain paramount. With a combination of proper technique, environmental control, and sophisticated understanding, welding cast iron with a 7018 rod not only becomes feasible but delivers durable joints that withstand operational stresses, bridging the gap between theoretical practice and effective application in the field.
By improving product reliability and performance through authoritative, expert application of the 7018 rod, businesses can ensure higher customer satisfaction and solidify their position as trusted providers of high-quality welding solutions.