E7018 H8 welding electrodes have become a cornerstone in the world of industrial fabrication and construction due to their unmatched properties and versatility. These electrodes are engineered for superior performance, adhering to rigorous specifications that bolster their reputation as a preferred choice among professionals.
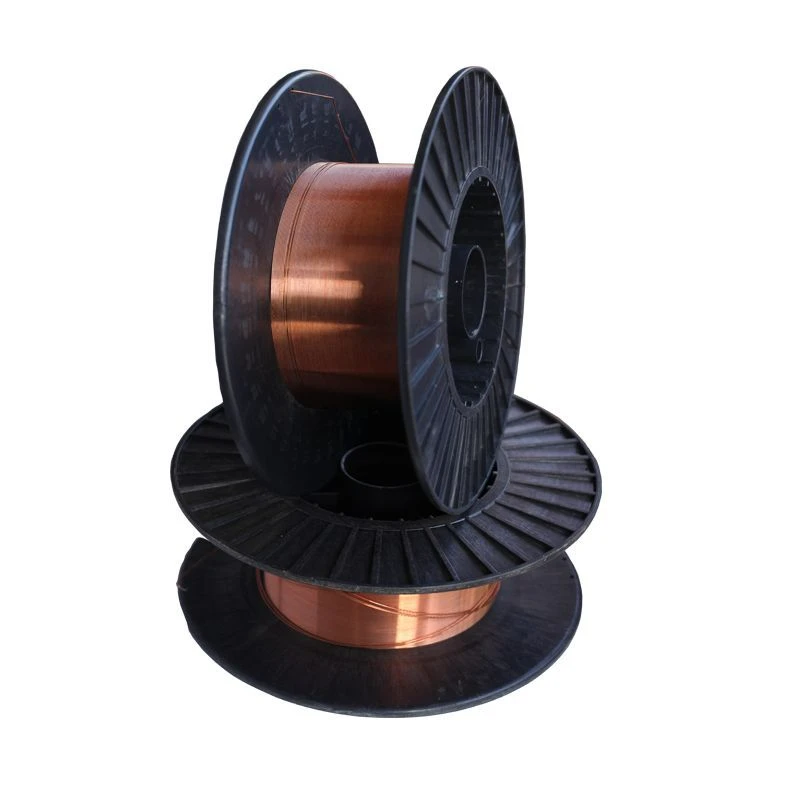
The E7018 H8 welding rod stands out for its high deposition rate and smooth weld finish. It is specifically designed to handle low hydrogen applications, making it ideal for structural steel, pressure vessels, and pipeline welding. The low hydrogen content minimizes the risk of cracking, ensuring a robust and durable bond. This feature makes the E7018 H8 a go-to electrode for projects that demand high integrity in welds.
In practice, the E7018 H8 electrode excels in out-of-position welding, which is a critical requirement in many industrial scenarios. Whether working on vertical or overhead structures, the performance of this electrode ensures consistent, high-quality welds. Its versatility across different welding positions enhances its appeal for complex assemblies that require numerous orientation adjustments.
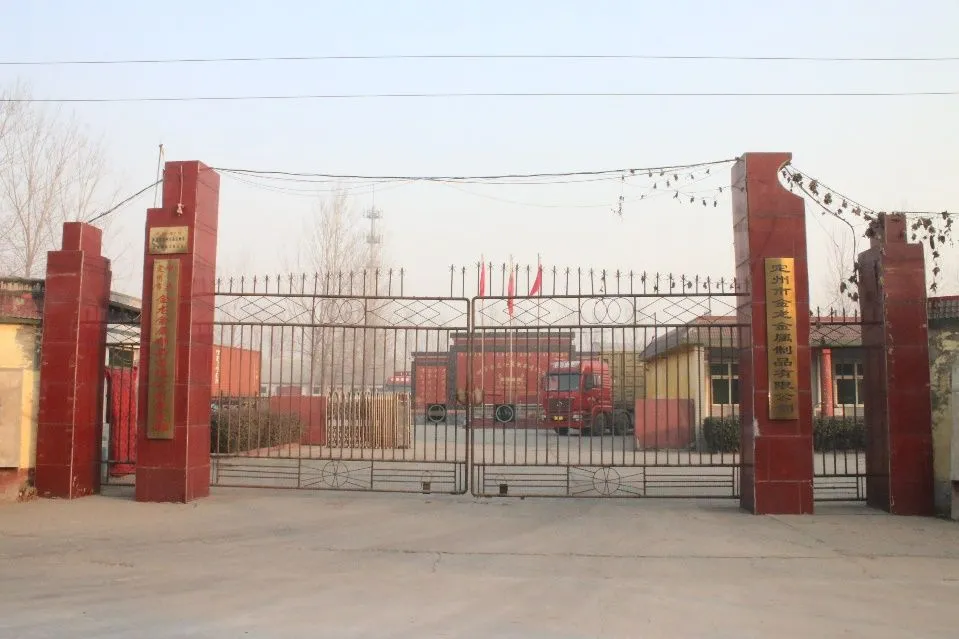
For industry professionals seeking to leverage the properties of E7018 H8 electrodes, understanding the nuances of their composition is vital. They contain a flux coating that generates minimal spatter and smoke, contributing to a cleaner working environment and reducing the need for post-weld cleaning. This aspect is particularly beneficial in large-scale projects where efficiency and cost-effectiveness are paramount.
The ability to work on heavy-gauge steel under various atmospheric conditions further underscores the adaptability of E7018 H8 electrodes. Given their ability to perform reliably in damp or less than ideal conditions, they have become indispensable in industries ranging from marine construction to urban infrastructure.
e7018 h8
While the technical specifications of the E7018 H8 are impressive, the real-world experiences of welders underscore their reliability and performance. Experts attest to the electrode's consistency during long welding sessions, a key factor that minimizes downtime and ensures project timelines are adhered to. Many professionals rely on E7018 H8 electrodes as they provide a trusted solution that balances speed, safety, and quality - crucial considerations in any high-stakes welding project.
Furthermore, E7018 H8 electrodes are a testament to the evolution of welding technology. Their design incorporates advanced metallurgy that ensures not only robustness but also compliance with industry standards for occupational health and safety. As global benchmarks for quality and performance continue to rise, E7018 H8 electrodes are at the forefront of setting new standards in welding excellence.
Trust in the E7018 H8 also stems from the rigorous quality controls involved in their production. Leading manufacturers engage in extensive testing of these electrodes under varying conditions to certify their suitability for myriad applications. This rigorous approach to quality assures buyers that they are investing in a product that will deliver both reliability and longevity.
Experts advocating for the use of E7018 H8 electrodes highlight the importance of operator training. A skilled welder can maximize the inherent benefits of these electrodes, achieving precision and strength in welds that are both structurally sound and aesthetically pleasing. Training programs and certifications underscore the value of expertise, which, when combined with superior materials like the E7018 H8, produce outstanding results.
In summary, the E7018 H8 electrode's reputation is built on dependable performance, superior metallurgical properties, and flexibility across applications. Its proven track record in industrial settings marks it as an authoritative choice among welding professionals seeking uncompromised quality and trustworthiness. As industries continue to evolve, the E7018 H8 electrode remains a pivotal tool in achieving welding excellence.