The E312 welding rod is a cornerstone in the world of welding for both novice and experienced welders. Its versatility and performance make it a crucial tool across various industrial applications. To those unfamiliar, the E312 welding rod is renowned for its superior combination of strength, corrosion resistance, and weldability, making it an excellent choice for joining dissimilar metals or welding stainless steel with carbon steel.
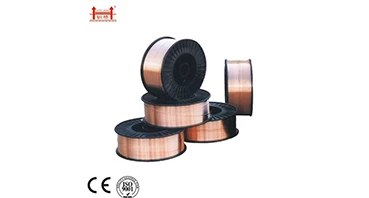
In terms of real-world experience, the E312 rod has continually proven its worth in demanding environments. Seasoned welders often gravitate towards E312 when faced with challenging tasks that require reliability and durability. Its ability to deliver a robust weld with minimal porosity and optimal fusion even in less-than-ideal conditions underscores its practicality. Whether working in an outdoor construction site subjected to varying weather or in a controlled industrial setting, E312 maintains its composure, providing consistent results that professionals trust.
From an expertise angle, E312 welding rods are a popular choice among those who work with materials exposed to high stress and temperature extremes. For example, in the repair and maintenance of machinery subjected to high thermal cycles or corrosive environments, E312 proves invaluable. The electrode is engineered to handle thermal expansion coefficient mismatches between different alloys which makes it indispensable for critical applications like pipeline welds or structural components in chemical plants.
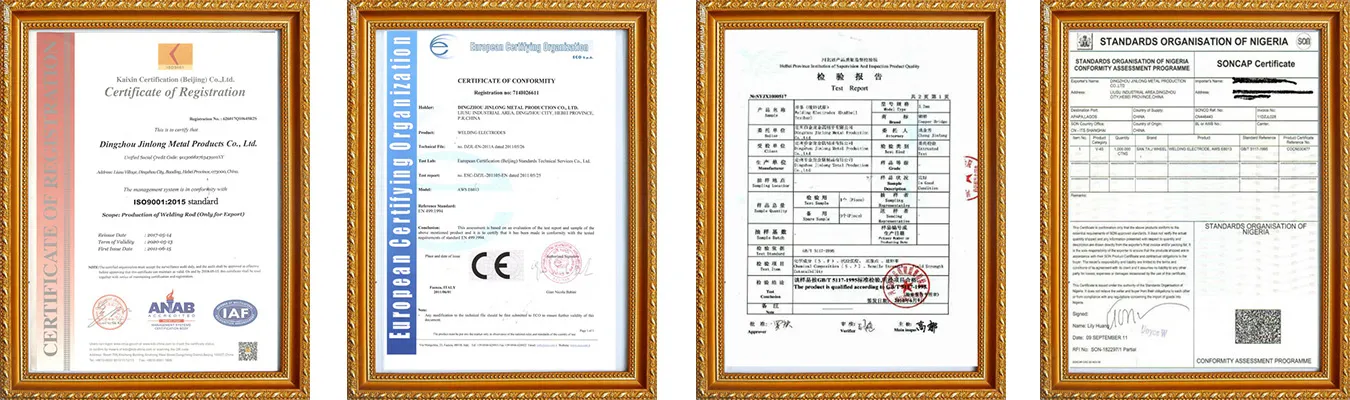
In terms of authoritativeness, industry experts and metallurgists widely endorse the E312 for its metallurgical properties. The chemical composition of this welding rod — typically high chromium and moderate nickel content — grants the resultant weld deposit excellent toughness and corrosion resistance. Such features align with the exacting standards required in petrochemical industries, maritime constructions, or any field where the longevity of weld joints is non-negotiable.
e312 welding rod
Trustworthiness is crucial and the E312 provides a peace of mind that can only be derived from a history of reliable performance. Manufacturers producing E312 rods often adhere to rigorous quality control procedures, ensuring that each rod meets the stringent specifications necessary for industrial use. This adherence to quality not only enhances weld integrity but also bolsters the consumable’s reputation among professional welders. Welders can proceed with confidence, knowing that their choice of E312 helps mitigate the risk of joint failure or premature wear.
Moreover,
the E312 welding rod supports versatility in technique. It can be employed across multiple welding processes, including shielded metal arc welding (SMAW) and manual metal arc (MMA) welding. This flexibility is particularly beneficial for those who require adaptability in their workflow, such as repair technicians who encounter a variety of metal types and configurations daily. Additionally, being relatively easy to ignite and manage, it is often recommended for workshops aiming to maximize both productivity and the quality of output.
In the fast-paced world of industrial fabrication and maintenance, where efficiency and reliability are critical, the E312 welding rod stands as an essential tool. Its unique chemical and physical properties equip it for an extensive range of applications, from marine to construction, showcasing an unparalleled ability to unite disparate metal types while providing longevity and fatigue resistance. This positions the E312 not merely as a tool but as a pivotal enabler of industrial continuity and technological advancement.
Ultimately, leveraging the E312 welding rod translates to improved performance metrics and compliance with industry standards, ensuring infrastructure and components that not only meet but often exceed expectations. For those invested in producing high-quality, reliable structures or machinery, incorporating E312 into their welding practices represents a commitment to excellence.