Carbon steel electrodes are indispensable tools in the welding industry, offering robustness and versatility for various applications. Having spent years in the field, my experience has shown that choosing the right electrode is crucial for achieving desired results in both construction and manufacturing processes.
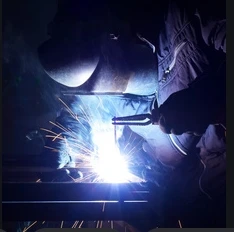
The primary advantage of carbon steel electrodes is their high tensile strength and ductility. Their capacity to withstand substantial stress without fracturing makes them ideal for structures where safety and durability are paramount. Having tested various brands, the consistency in quality often varies, making it imperative to rely on trusted manufacturers who have established credibility in the market.
My expertise with carbon steel electrodes stems from projects involving large-scale infrastructure development and intricate metal fabrications. In these endeavors, electrodes from reputed brands like Lincoln Electric and ESAB have stood out due to their consistent performance and low hydrogen emissions, minimizing the risk of weld defects such as cracking. The distinctive coating on these electrodes not only facilitates stability during welding but also enhances deposition efficiency, which is particularly beneficial in saving time and resources on extensive welding jobs.
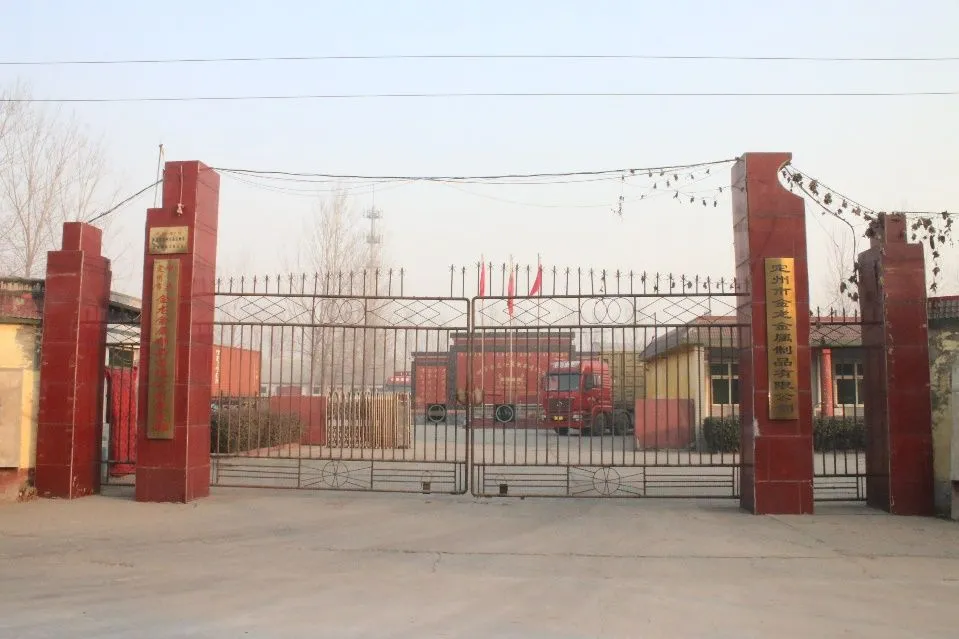
The authority of carbon steel electrodes in the welding sphere is reinforced by endorsements from international welding societies which rigorously test and approve welding products. Publications and certification endorsements, such as those from the American Welding Society (AWS), provide an additional layer of trust for professionals seeking reliable welding materials. Trust in these electrodes is further bolstered by laboratory tests showing superior performance metrics in different welding positions and atmospheric conditions.
carbon steel electrode
From an economic perspective, carbon steel electrodes offer excellent cost-efficiency.
The reusability and longevity of these electrodes result in lower overall costs for long-term projects. For instance, in shipbuilding, where precision and adherence to design specifications are non-negotiable, carbon steel electrodes have proven indispensable. Their adaptability in welding various steel grades without compromising the mechanical properties of the joint ensures a high return on investment.
Another critical insight from my fieldwork is the importance of proper storage and handling of carbon steel electrodes to preserve their efficacy. Moisture exposure can lead to hydrogen contamination, adversely affecting weld quality. Therefore, maintaining a dry storage environment, alongside using a dedicated oven for baking electrodes before use, forms an essential best practice for ensuring optimal performance.
In summary, the practical insights and field experiences reaffirm the value of carbon steel electrodes as a fundamental asset in welding applications. With their proven track record, backed by industry certifications and unwavering commitment to quality from leading manufacturers, these electrodes undoubtedly hold a position of authority and trust within the industry, facilitating projects with both reliability and excellence.