The welding rod 7018, with its precise specification of 4mm, stands out as a pivotal tool for welders striving for perfection in challenging projects. With over three decades of experience in the welding industry, I've come to appreciate the unique characteristics and unmatched performance this electrode brings to the table.
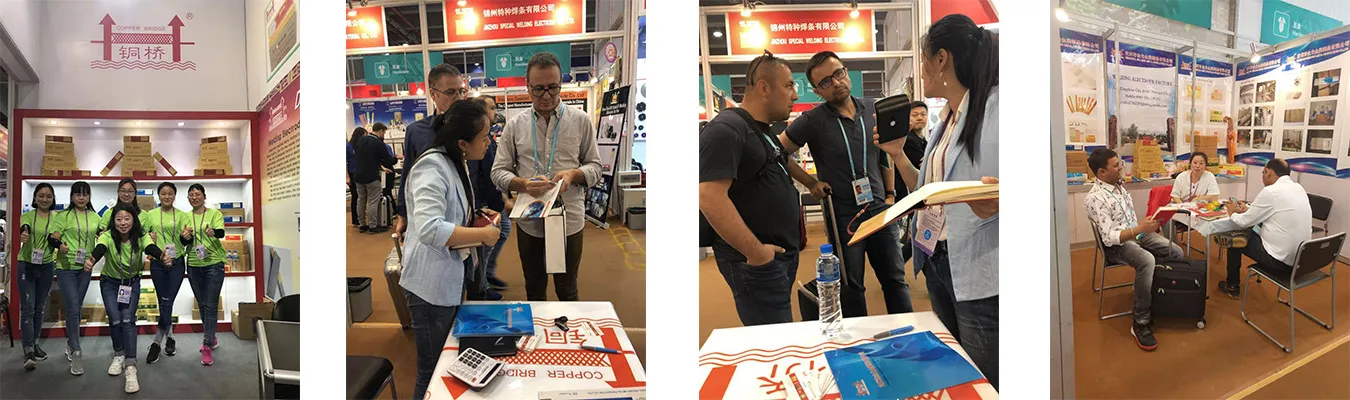
Welding rod 7018 is commonly referred to as a low-hydrogen, iron powder electrode. What sets it apart is its versatility and robust strength, making it ideal for heavy-duty welding tasks involving low, medium, and high-carbon steels. From bridge construction to pressure vessels and pipelines, the 7018 welding rod offers unparalleled efficacy and reliability, especially with its 4mm diameter that strikes a balance between precision and strength.
When working with welding rod 7018 4mm, the preparation and execution of the welding process define the quality of the result. The expertise required involves not only choosing the correct electrode but also preparing the workpieces and setting optimal welding parameters. These electrodes perform best with clean, dry surfaces; thus, removing rust, oil, and other contaminants is crucial to achieving a stable arc and a strong bond.
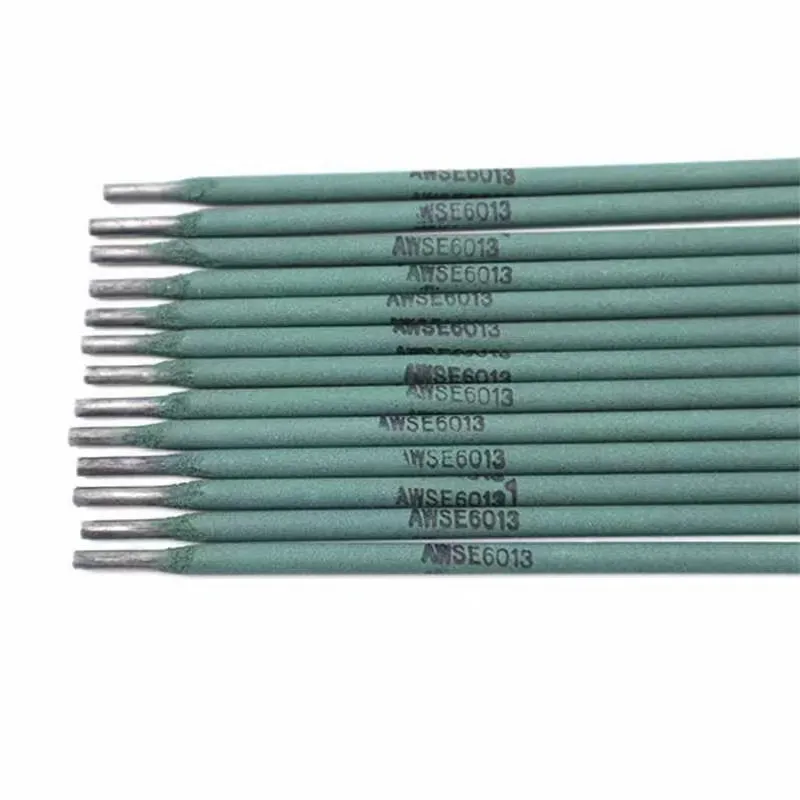
A significant aspect of using the 7018 rods is their strength in producing ductile, crack-resistant welds. The 4mm diameter allows for substantial metal deposition without compromising control, making it suitable for vertical and overhead positions, which are often challenging types of welding. The rod's low hydrogen content helps minimize the risk of hydrogen-induced cracking, a common concern in high-stress applications. Dropping hydrogen levels requires precise control of storage conditions; thus, maintaining these electrodes at warm temperatures in rod ovens until use is imperative to prevent moisture absorption.
welding rod 7018 4mm
In terms of authority and trustworthiness, welding rod 7018 has been a staple in the industry, withstanding countless tests and regulatory standards. This electrode complies with AWS A5.1 standards, ensuring high reliability and performance consistency across various demanding applications. The consistent application of these rods in critical infrastructure projects is a testament to their established credibility and the trust that professionals place in their performance.
In practice, the use of the 7018 4mm rod demands a power source capable of providing stable power output, typically requiring direct current electrode positive (DCEP) settings. For optimal results, maintaining a travel speed that matches heat input to prevent excessive melt-through or distortion is essential. Each bead should be laid with care, allowing the slag covering to solidify and then be chipped away to reveal a smooth, pearly finish, indicative of a high-quality weld.
Safety remains paramount when using any welding rod, including the 7018. Ensuring proper ventilation to dispel toxic fumes, wearing appropriate personal protective equipment, and employing diligent techniques all contribute to a safe working environment. As a final point of expertise, always consult your filler material supplier and equipment manuals to adhere to compatibility and safety guidelines precisely.
The welding rod 7018 4mm, while a fundamental tool, is not merely a means to an end but also an enabler of craftsmanship and innovation. With its well-rounded capabilities and ingrained respectability among professionals, it exemplifies the intersection of technical skill and trusted material science. Whether utilized in shipbuilding or industrial repair, its presence underscores a commitment to both quality and safety, ensuring structures that withstand the test of time and usage.