Enhancing industrial processes often hinges on the choice of materials and tools, especially when dealing with carbon steel pipes. The welding electrode for carbon steel pipe plays a crucial role in determining the quality, durability, and strength of the joinery. As an experienced professional in this domain, it's essential to delve deep into the particulars that make certain welding electrodes superior for these applications.

Carbon steel, renowned for its versatility and affordability, is sporadically simple to weld. However, its chemical composition requires specific electrode considerations to avoid issues such as cracking or weakening of the weld over time. Among the variety of electrodes available, selecting one that complements the properties of carbon steel is paramount. One of the reputable choices in the industry is the E6010 electrode. Its cellulose-based coating facilitates deeper penetration, making it ideal for root pass applications in pipe welding. This electrode excels in demanding environments, such as those found in pipeline constructions and industrial setups where robust and reliable welds are necessary.
Another significant contender is the E7018 electrode. It's coated with low-hydrogen potassium iron powder, offering a high deposition efficiency. This type of electrode is especially beneficial when welding carbon steel pipes that are thick or require a durable and aesthetically smooth finish. The reduced hydrogen content minimizes the risk of cracking, a common issue encountered with carbon steel due to its high carbon content. For industries that prioritize precision and long-term efficacy, using E7018 ensures the structural integrity of the weld, thus bolstering trust in the project outcome.
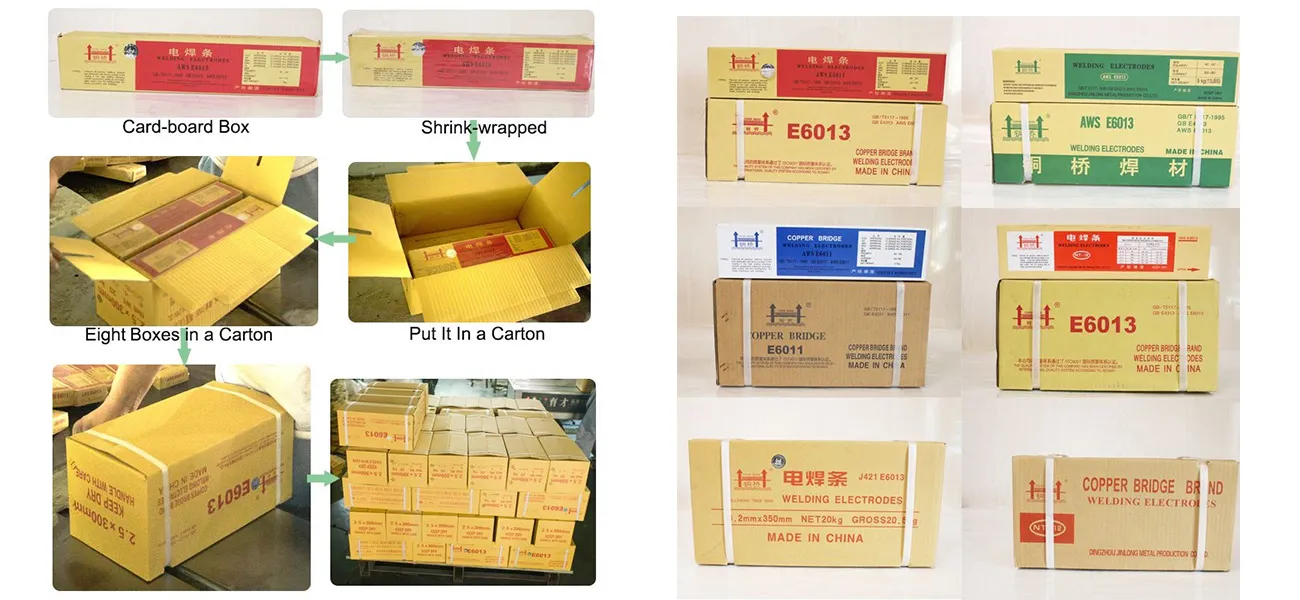
Expert welders frequently share their experiences concerning the pre- and post-treatment of carbon steel joints to further enhance the outcome. Preheating the pipes before welding can significantly reduce the thermal gradient, thus limiting the chances of forming brittle structures within the weld zone. Post-weld heat treatments can relieve stresses and improve ductility, which is particularly vital in environments subject to fluctuating pressures and temperatures.
welding electrode for carbon steel pipe
The authority in welding electrodes extends to understanding the dynamic nature of industry standards and certifications. Organizations like the American Welding Society (AWS) set rigorous standards that guide the selection and application of welding electrodes. Choosing electrodes that comply with these standards is not only a testament to quality but also to a commitment to safety and longevity.
Trust is a significant pillar in the industry. Companies and trade professionals must rely on electrodes procured from reputable manufacturers with a history of quality assurance. Establishing this trust comes from years of operational success, testing, and continuous improvement. A collaborative approach with manufacturers can also yield tailor-made solutions that cater to specific industrial needs, further enhancing project-specific outcomes.
In summary,
the selection of the right welding electrode transcends beyond routine decision-making. It is a confluence of real-world experience, technical expertise, adherence to authoritative standards, and an unwavering commitment to quality and safety. As industries evolve, the welding methodologies and tools used must also advance to meet the growing demand for reliability, precision, and sustainability in carbon steel applications. Investing in quality electrodes is not just a choice but a strategic decision to ensure the resilience and success of industrial ventures.