The art of welding, much akin to a skillful orchestra conductor leading a symphony, requires precision, expertise, and the right tools. Among those tools, a stainless stick welding rod plays an instrumental role, especially when tackling stainless steel projects. As steel structures endure the relentless beat of time and elements, a seasoned welder knows the significance of selecting the right welding rod to ensure durability, integrity, and aesthetics.
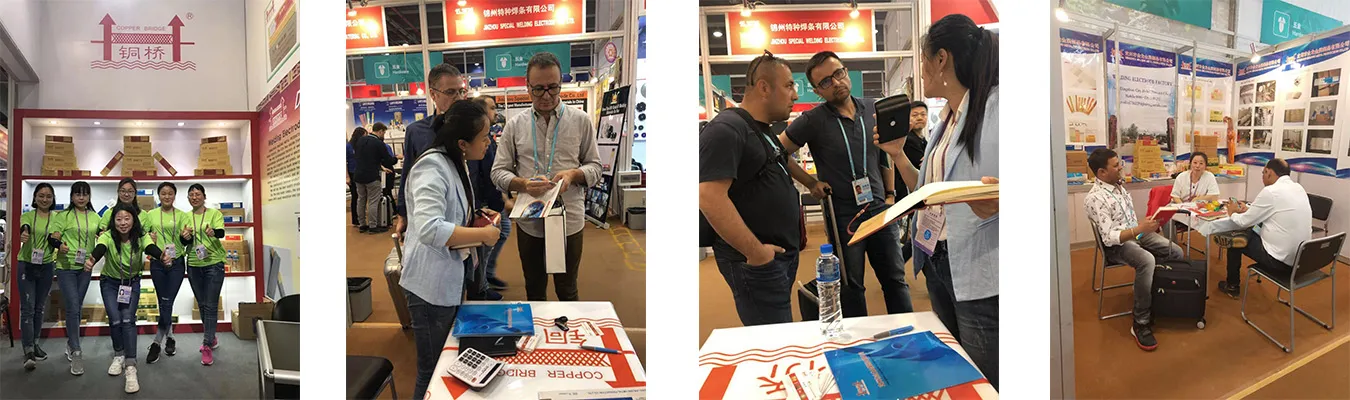
Stainless stick welding rods are uniquely designed for welding stainless steels, which are renowned for their resistance to corrosion, heat, and their appealing finish.
The use of stainless in construction spans global boundaries, making it an industry staple. However, achieving the perfect weld with stainless steel requires more than just the basics; it demands an in-depth understanding of the rods used in the process.
The uniqueness of stainless stick welding rods lies in their composition. Typically, these rods contain a core of stainless steel wire, surrounded by a flux coating that helps to protect the weld pool from the atmosphere. This coating is crucial as it not only protects the weld area from contamination but also stabilizes the arc and influences the mechanical properties of the weld. The resulting welds from these rods are characterized by high strength, corrosion resistance, and a smooth finish, hallmark traits of stainless steel itself.
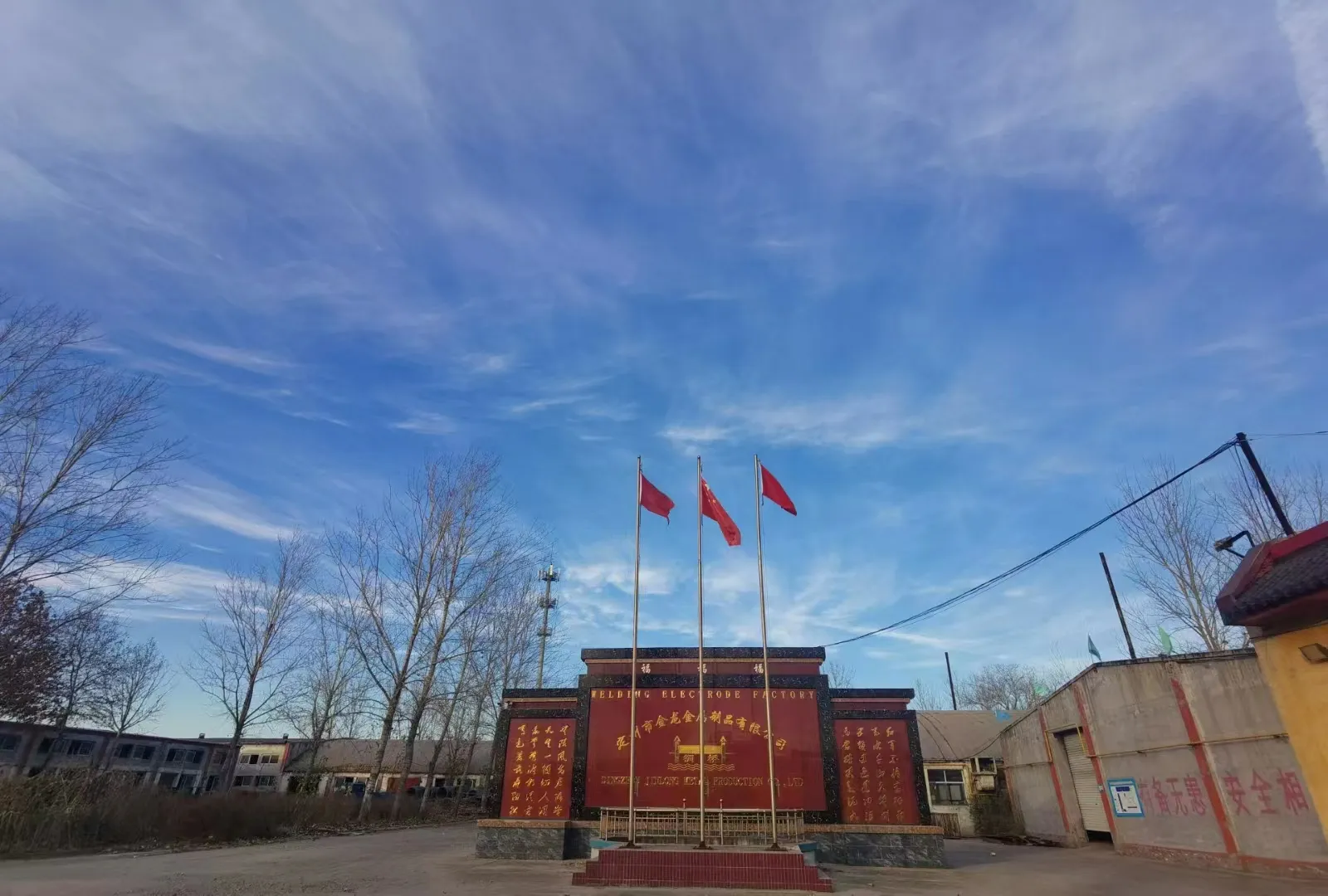
When diving deeper into the technical side, there are several types of stainless rods, each tailored to specific applications. The most commonly used alloy is 308L, suitable for 304-grade stainless steel and 18/8 steel, describing its chromium and nickel composition. For higher temperature applications, or environments with aggressive corrosive agents, 316L rods are often preferred due to their enhanced molybdenum content which offers superior corrosion resistance.
Experience dictates that the choice of rod also considers the position of the welding. E6010 and E7018 are popular choices for all-position welding, but when it comes to stainless steel, using rods specifically designed for it, such as the E308L-16, is pivotal in achieving strength and aesthetic output.
stainless stick welding rod
In practice, achieving a quality weld involves not only the choice of rod but the skillful application of current and technique. The current setting for stainless welding rods is often pegged at lower amperages to avoid overheating which can lead to warping, especially in thinner gauge metals. Ensuring a stable arc and proper travel speed is also essential in maintaining consistent heat input and preventing common issues like warping or burn-through.
Over the years, feedback from professional welders globally has highlighted the practicality and reliability of stainless stick rods. Whether used in the fabrication of chemical tanks, kitchen equipment, or architectural features, these rods provide the structural integrity demanded by rigorous industry standards. Their performance, tested in various environments, stands as a testament to their essential role in modern fabrication.
Reputation and trustworthiness in product quality are crucial for suppliers in this field. Leading manufacturers of stainless stick welding rods invest significantly in research and technological advancements to improve product features, such as reducing spatter or enhancing user comfort. Welders return time and again to trusted brands, knowing their reputation rests not on marketing alone, but on decades of proven performance and continual development.
The credibility of stainless stick welding rods is further bolstered by certifications and standards, such as those from the American Welding Society (AWS) and ISO. Compliance with these standards assures users they are working with materials that meet stringent quality controls pertinent to safety and performance.
In conclusion, the choice of stainless stick welding rods can profoundly influence the outcome of welding projects involving stainless steel. Their importance cannot be overstated when precision, appearance, and strength are at stake. Professional welders equipped with knowledge, appropriate technique, and the right rod selection stand to produce superior results, thus cementing their credibility and expertise in the field. As advancements in metallurgy and manufacturing continue, the evolution of these indispensable welding rods serves as a reminder of the dynamic progress within the world of metal fabrication.