In the world of welding, the choice of electrode is paramount to achieving quality, durable welds. Different types of electrodes cater to various welding requirements, influencing factors like weld strength, corrosion resistance, and overall quality. This article delves into the myriad of welding electrodes available, providing insights based on expertise and experience while ensuring reliability and authoritative guidance for selection.
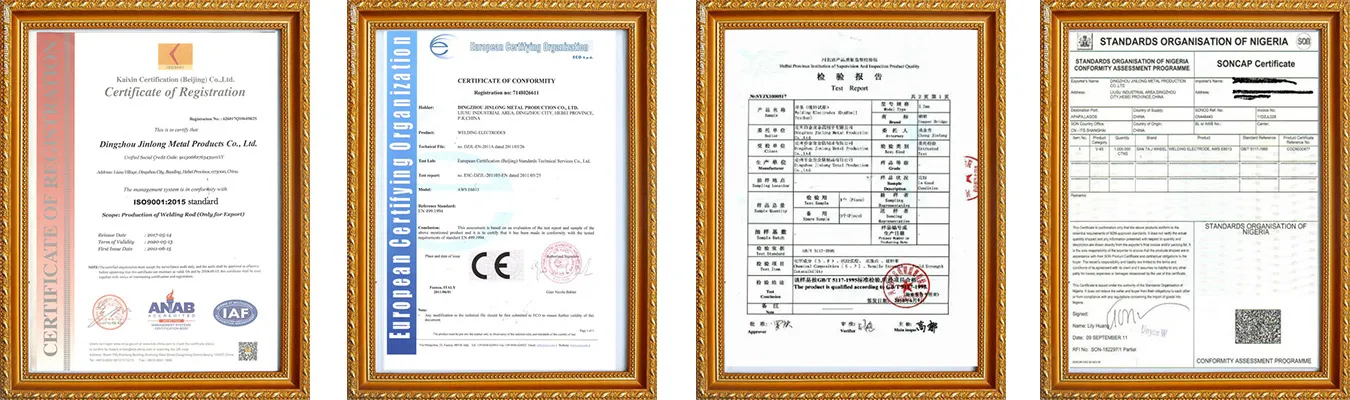
Welding electrodes are broadly categorized into consumable and non-consumable types. Consumable electrodes, which melt and become part of the weld, are common in processes such as Shielded Metal Arc Welding (SMAW) and Gas Metal Arc Welding (GMAW). Non-consumable electrodes, like those used in Tungsten Inert Gas (TIG) welding, do not melt and serve a different function.
1. Shielded Metal Arc Welding (SMAW) Electrodes
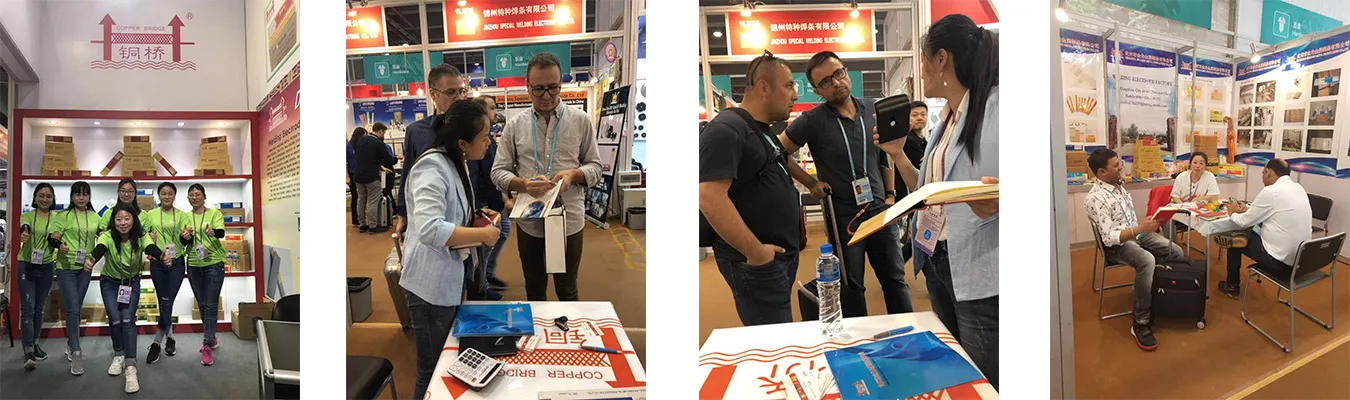
SMAW, often referred to as stick welding, utilizes electrodes that are coated with a flux. The flux stabilizes the arc and shields the molten metal from contaminants. Among the various SMAW electrodes, E6010, E6011, E7018, and E7024 are the most prevalent.
- E6010 and E6011 Known for their deep penetration and strong arc force, these electrodes are ideal for welding through rust or paint, making them suitable for outdoor and repair applications. They produce welds that are tough and ductile, although their cellulose-based coating can be challenging for beginners.
- E7018 Renowned for its low hydrogen properties, the E7018 electrode minimizes the risk of cracking in the weld. Its applications span from structural steel fabrication to pressure vessels, providing a smooth, stable arc with excellent mechanical properties.
- E7024 This electrode is characterized by its high deposition rate, making it perfect for horizontal fillet welds and flat position welds, often used in shipbuilding and heavy equipment manufacturing.
2. Gas Metal Arc Welding (GMAW) Electrodes
In GMAW, also known as MIG welding, the electrode is a wire fed continuously through the welding gun.
The wire acts as both electrode and filler material.
kinds of electrode in welding
- ER70S-6 A versatile choice, ER70S-6 is used across industries due to its ability to produce clean, high-quality welds in all positions on mild steel. It's particularly effective on surfaces with mill scale and rust.
- ER5356 and ER4043 Designed for aluminum welding, these electrodes offer corrosion resistance and strength. ER5356 is preferred for its higher tensile strength, while ER4043 provides better ductility and less susceptibility to cracking.
3. Tungsten Inert Gas (TIG) Welding Electrodes
TIG welding, revered for its precision and aesthetics, uses non-consumable tungsten electrodes. These electrodes provide a stable arc and are pivotal in applications where weld appearance and precision are critical.
- Thoriated Tungsten With enhanced electron emission, thoriated tungsten is favored for DC welding. Its robustness and ability to withstand high amperage make it a staple in industries like aerospace.
- Ceriated Tungsten Ideal for both AC and DC applications, ceriated tungsten electrodes are noted for their low work function, offering excellent arc starting at low amperages, beneficial for delicate work such as thin metal sheet welding.
- Lanthanated Tungsten These electrodes have become increasingly popular due to their versatility, providing a steady arc for both AC and DC welding while offering lower burn off and less tungsten spitting.
Choosing the right welding electrode hinges on the specific requirements of the task at hand—from the type of material being welded to the desired welding position and conditions. A thorough understanding of the characteristics and applications of each electrode type empowers welders to make informed decisions, ensuring optimal performance and structural integrity of their welds. With ever-evolving technology and materials, staying updated with the latest electrode advancements is essential for continuing excellence in the field of welding.