Identifying the right cast iron welding rod involves more than just understanding the basic specifications; it requires a nuanced understanding of metallurgy and the specific demands of your welding project. The numbers associated with cast iron welding rods are not mere catalog IDs—they contain critical information about the rod's properties, suitable applications, and performance characteristics.
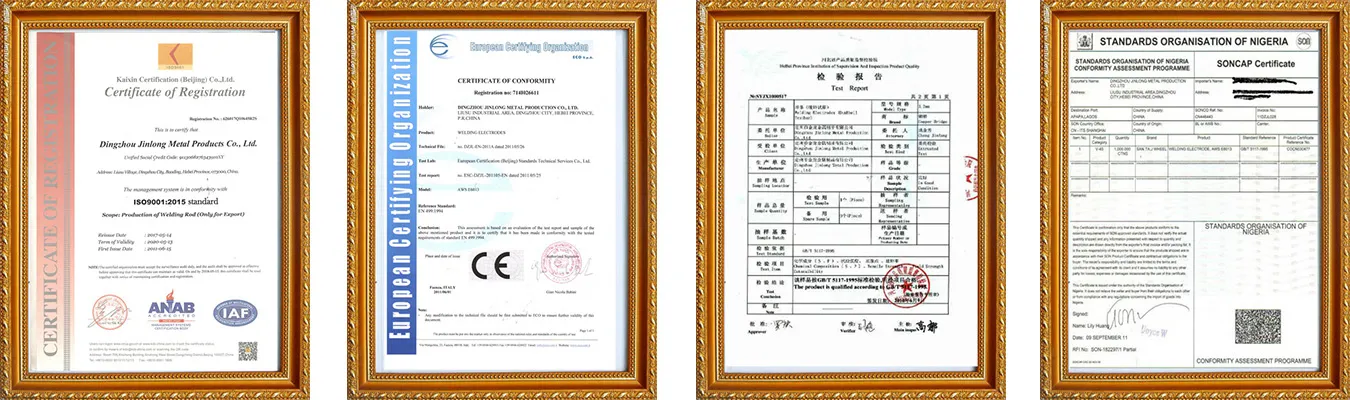
Firstly, it's essential to recognize the metallurgical challenges presented by cast iron. This material, known for its high carbon content, poses unique challenges during welding. The primary challenge is the tendency for welds to crack due to carbon migration and the creation of brittle microstructures.
This is where the correct choice of welding rod becomes crucial.
The numbering system of welding rods provides insights into the rod's composition and its applicability. For instance, rods like NI-CAST 55 and NI-CAST 99 are specifically designed for cast iron welding. The numbers here indicate the percentage of nickel content. NI-CAST 55 consists of approximately 55% nickel, which makes it suitable for welding cast iron with a higher likelihood of maintaining the structural integrity of the parent material. In contrast, NI-CAST 99 contains about 99% nickel, offering better performance for applications requiring a softer and more ductile weld. The higher nickel content reduces the chances of cracking and is ideal for more complex or high-stress applications.

Experts in the field often emphasize the importance of preheating and slow cooling when working with cast iron welding rods. Preheating the material helps in reducing the thermal gradient between the weld area and the surrounding metal, minimizing internal stresses. Additionally, slow cooling prevents the formation of hard microstructures that could lead to failure.
Choosing the appropriate rod involves understanding the end-use requirements. For instance, if the welded joint is expected to experience high mechanical stress, opting for a rod with higher ductility such as the NI-CAST 99 might be advisable. On the other hand, for straightforward repairs, a more economical option like a 55% nickel rod could suffice.
cast iron welding rod numbers
In addition to the rod’s chemical composition, the environment in which the welding takes place is also a consideration. Environmental factors like temperature, humidity, and exposure to corrosive elements can affect the weld quality. Therefore, ensuring that the working conditions are optimal and that the rods are stored to maintain their integrity is vital.
The thickness and positioning of the cast iron pieces also play a role in rod selection. Thicker sections may require rods that offer better penetration, ensuring a strong bond throughout the weld’s depth, while thinner sections may need rods with smoother arc characteristics to avoid burn-through.
Understanding these nuanced details not only enhances the outcome of your welding project but also demonstrates a level of professionalism and expertise that's crucial for building trust with clients and fellow craftspeople. Maintaining up-to-date knowledge of advancements in welding materials and techniques is essential for staying authoritative in a field that is continuously evolving.
In conclusion, selecting the right cast iron welding rod is a complex decision that blends art and science. It requires an appreciation for the material properties of cast iron, an understanding of the welding environment, and a careful consideration of the specific requirements of the task at hand. By paying attention to these aspects, you not only ensure the success of your projects but also reinforce your position as a knowledgeable and trustworthy professional in the industry.