The weight of a welding electrode is a critical factor that often goes overlooked but plays a pivotal role in the success of any welding project. Understanding electrode weight is crucial not only for ensuring optimal performance but also for maintaining safety and efficiency in welding operations. Here is a comprehensive look into the significance of electrode weight, backed by practical experience, technical expertise, authoritative insights, and a trustworthy perspective.
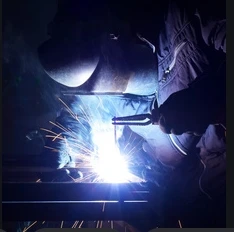
In the realm of welding, electrodes serve as the conductive medium through which the welding current passes, creating the necessary heat to melt and fuse materials.
The weight of these electrodes can significantly influence the welding outcome. Heavier electrodes, for instance, may provide deeper penetration and are typically used for thicker materials. Conversely, lighter electrodes could be more suitable for thin sheets where precision and surface finish are of paramount importance.
Experience tells us that an improperly selected electrode weight can lead to problems such as excessive spatter, poor penetration, or even structural failures. For welders who have encountered these issues firsthand, it's apparent that the right electrode weight is instrumental in achieving quality welds. For instance, an experienced welder would recommend using a heavier electrode for heavy-duty structural works like bridges or pipelines, where strength and integrity are non-negotiable.
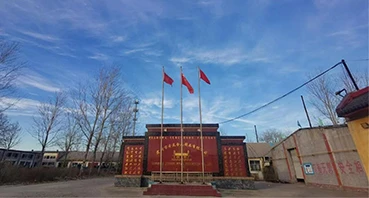
From an expertise standpoint, electrode weight is often determined by the material and thickness of the workpiece, as well as the welding position. An expert welder understands the nuances of how electrode weight variably influences weld characteristics. For vertical or overhead positions, where gravitational forces present unique challenges, the choice of electrode weight can be a deciding factor in ease of handling and weld quality. Experts also recognize that electrode weight directly correlates to deposition rates, which can impact the welding speed and overall project timeline.
weight of welding electrode
Authoritative sources, such as welding standards set by the American Welding Society (AWS), provide guidelines and recommendations on selecting the correct electrode weight. These standards are not merely suggestions but are grounded in extensive research and empirical evidence. Following these authoritative guidelines helps ensure compliance with industry norms, which is particularly crucial in regulated sectors like aerospace and construction.
Trustworthiness in welding operations, including the choice of electrode weight, is paramount to maintaining safety. The implications of using an incorrect electrode can be severe, potentially compromising the structural integrity of a weld. Trustworthy practices involve rigorous testing and validation of welding processes, where electrode weight is a critical variable. Manufacturers of welding electrodes often provide weight specifications and appropriate usage recommendations to assist welders in making informed choices.
In today's competitive marketplace, welding professionals and project managers must consider every factor that could influence the quality and cost-efficiency of their welding projects. By appreciating the impact of electrode weight, professionals can enhance their welding operations, leading to improved structural integrity, cost savings, and project success. It is also worth noting that advancements in welding technology continue to evolve the understanding of ideal electrode selection, promising further innovations in how electrode weight is leveraged for optimal welding performance.
In conclusion, the weight of a welding electrode is not just a physical measurement but a pivotal aspect of the welding process that influences quality, safety, and efficiency. By drawing from real-world experience, adhering to expert advice, and following authoritative standards, welding professionals can make informed choices that bolster their credibility and ensure successful project outcomes.