Choosing the right welding rod is crucial for achieving strong, effective welds, and when it comes to selecting between a 1/8 inch rod and a 3/32 inch rod, understanding the nuances can greatly impact your decision. Both 1/8 inch and 3/32 inch welding rods have their own applications and benefits, depending on the type of welding job you are undertaking.
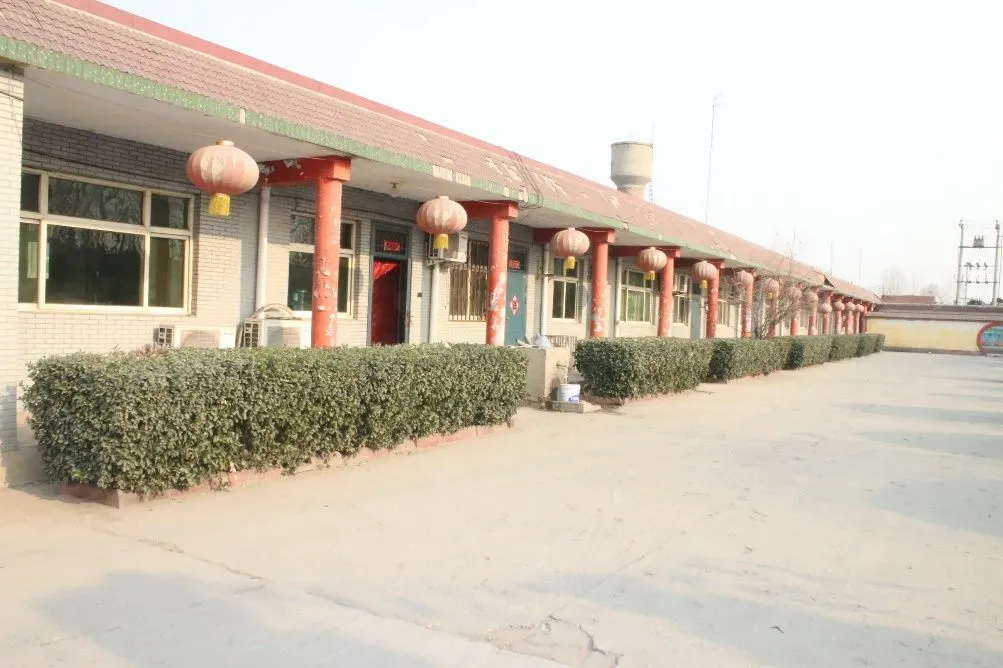
Welding rods, also known as electrodes, are essential tools in the welding process. The size of these rods often determines the type of material they are best suited for, as well as the overall quality and strength of the weld.
Understanding Welding Rod Diameters
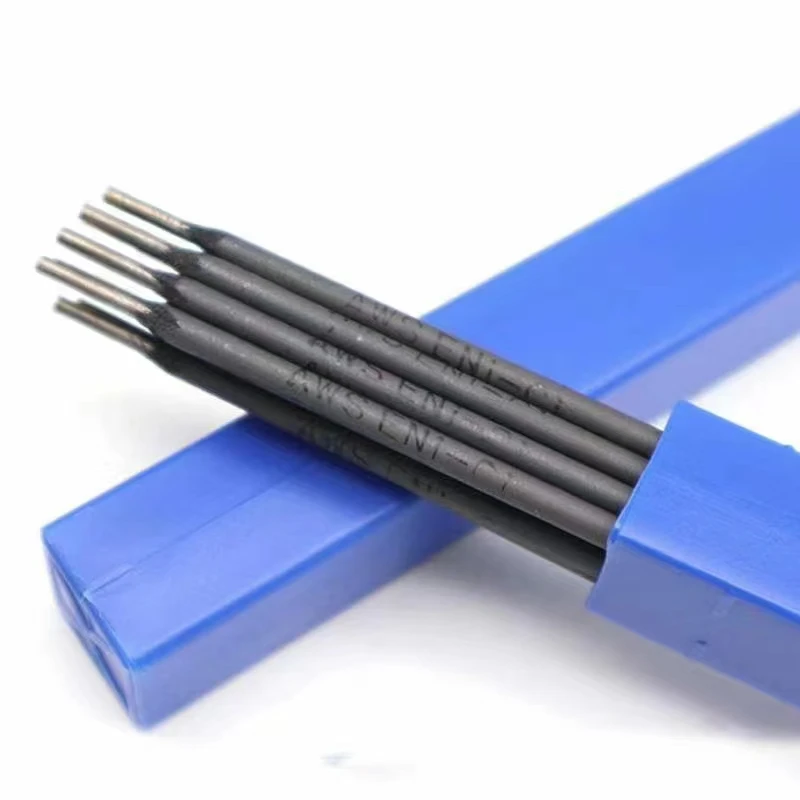
The diameter of a welding rod is a critical factor that dictates its usability for various projects.
The 1/8 inch rod is generally more robust compared to its 3/32 inch counterpart. Due to its larger diameter, it is often used for heavier welding tasks where greater heat penetration is required. This makes it ideal for welding thicker materials such as steel beams or other substantial constructions.
In contrast, the 3/32 inch welding rod, being thinner, is typically used for lighter duty tasks. It provides more precise control and is ideal for more delicate work, such as joining thinner metals or executing fine detail work on intricate projects. The smaller diameter allows for quicker melting, which is crucial for avoiding overwelding and ensuring a cleaner finish.
Practical Experience with Welding Rods
Experience plays a vital role when deciding between these two sizes. Many professional welders tend to keep both sizes in stock to handle a variety of welding tasks efficiently. In scenarios requiring deep weld penetration, such as heavy-duty repairs or construction, a 1/8 inch rod provides the strength and durability needed. However, for intricate designs or repairs on thinner materials, a 3/32 inch rod allows for more finesse and control.
Expertise in Welding Techniques
which is bigger 1 8 or 3 32 welding rod
Expert welders understand that the choice of welding rod also depends on the welding position. In overhead or vertical welding, where gravity can affect the weld pool, a 3/32 inch rod might be preferred for its easier control and lighter weld pool. Meanwhile, in flat or horizontal welding positions, a 1/8 inch rod can be used effectively without the added concern of gravity pulling excessively on the molten metal.
Authoritativeness and Source Credibility
Industry standards and guidelines from authoritative bodies should always be considered when selecting welding materials. Organizations like the American Welding Society (AWS) provide comprehensive standards for welding rods, and following these can enhance the quality and safety of your work. Relying on certified welding supplies and consulting professionals within the field ensures that the best practices are adhered to.
Building Trustworthiness through Quality Results
Ultimately, trustworthiness in welding comes from consistent quality results. Experienced welders often emphasize the importance of testing different rods on scrap metals before proceeding with the actual project. This practice not only helps in determining which rod yields the best results for a specific task but also builds a reputation for precision and reliability.
Furthermore, understanding the nuances of electrode composition—such as whether the rod is made from low-hydrogen materials or if it features any coatings that facilitate smoother welding—can enhance the quality of the weld, thereby building clients' trust over time.
In conclusion, while both the 1/8 inch and 3/32 inch welding rods have significant differences, the choice ultimately hinges on the specific requirements of the task. Welders must balance the need for strength and control with the thickness of the materials they are working with, while adhering to safety standards and leveraging professional expertise for optimal results.