In the dynamic landscape of welding, selecting the right filler material plays a crucial role in ensuring robust and reliable joints. The MIG solid welding wire stands out as an essential component for achieving superior welding quality across diverse metalwork projects. A deep dive into this product reveals its multifaceted advantages and the specific nuances that make it the preferred choice for professionals and hobbyists alike.
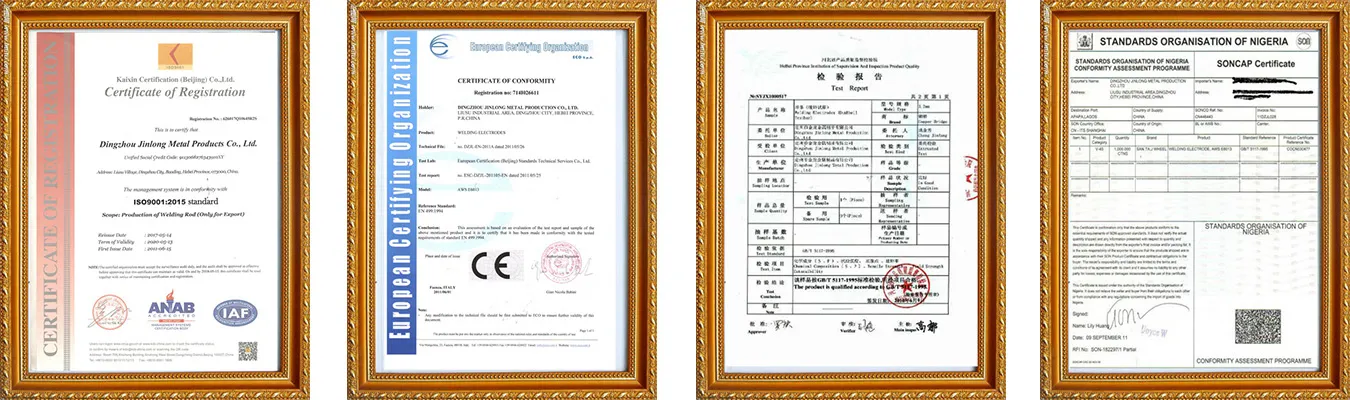
MIG solid welding wire, often regarded as the backbone of metal inert gas welding, comes in various compositions tailored to suit different materials, such as carbon steel, stainless steel, and aluminum. This versatility is critical because it allows welders to match the wire with the base materials, ensuring optimal fusion and mechanical properties. For instance, when welding carbon steel, a copper-coated solid wire typically known as ER70S-6 is often employed due to its excellent arc stability, ease of use, and the ability to produce a high-quality weld even on slightly rusty or contaminated surfaces.
One of the primary reasons for the prevalent use of MIG solid welding wire is its contribution to the consistent and smooth feeding process. Compared to flux-cored wires, solid wires minimize spatter, resulting in cleaner welds that require less post-weld cleanup. This is particularly beneficial in high-volume production settings where time efficiency and cost reduction are paramount. Additionally, the smooth and continuous feed provided by solid wires reduces the likelihood of wire burn-back and bird-nesting, common issues that can disrupt the welding process and lead to costly downtime.
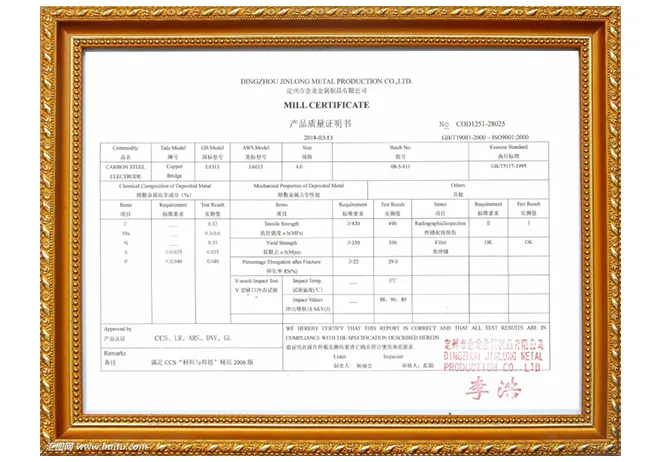
Experienced welders appreciate the control and precision that MIG solid welding wire offers. Its performance is less dependent on operator skill compared to some other processes, which makes it accessible for beginners while still being the choice of seasoned professionals for intricate work. The wires allow for flexible control over the welding arc, providing greater accuracy and adaptability based on the specific demands of the project at hand. This adaptability is indispensable when welding in various positions, such as overhead or vertical, which are often necessary in complex assemblies and repairs.
mig solid welding wire
From an expertise standpoint, the science behind solid welding wire continues to evolve with advancements in metallurgy and production techniques. Modern solid wires are often engineered with precise chemical compositions and surface finishes that enhance their performance characteristics. These innovations result in wires that deliver stronger welds with fewer defects. For example, the inclusion of elements like silicon and manganese can improve the weld's deoxidation properties, leading to a stronger bond and a visually appealing finish. Understanding these technical aspects allows welders to select the appropriate wire for each specific application, ensuring the integrity and durability of the finished product.
The authoritative trust that users place in solid welding wires is bolstered by their widespread approval and certification by industry standards. These standards, set by organizations such as the American Welding Society (AWS) or the International Organization for Standardization (ISO), ensure that wires meet rigorous testing criteria for performance and safety. Products that comply with these standards provide welders with the assurance that they will achieve reliable and consistent results in their welding endeavors.
Trustworthiness in MIG solid welding wire is not only about meeting industry standards but also about the reputation of the manufacturers. Leading producers of solid wires invest heavily in research and development to innovate and refine their products. Their continued commitment to quality means that professionals around the globe can rely on these wires for critical applications, knowing that their performance will be consistent with expectations.
In summary, the decision to use MIG solid welding wire in a project is not just about convenience; it's an informed choice that highlights the emphasis on quality, precision, and efficiency. By understanding the specific attributes and benefits of these wires, welders can enhance their craftsmanship, minimize errors, and complete projects with confidence. The welds achieved with these wires bear testament to the blend of art and science that welding truly represents.