Understanding the nuances of electrical components can prove instrumental in optimizing your system’s efficiency and performance. Among such components, the E308L 16 welding electrode is revered for its distinctive properties that cater to specific professional needs while offering economic value. Though commonly used in various industries, there exists a myriad of lesser-known yet crucial details regarding its efficient use and associated current, appealing specifically to both seasoned welders and novices seeking to enhance their craft.
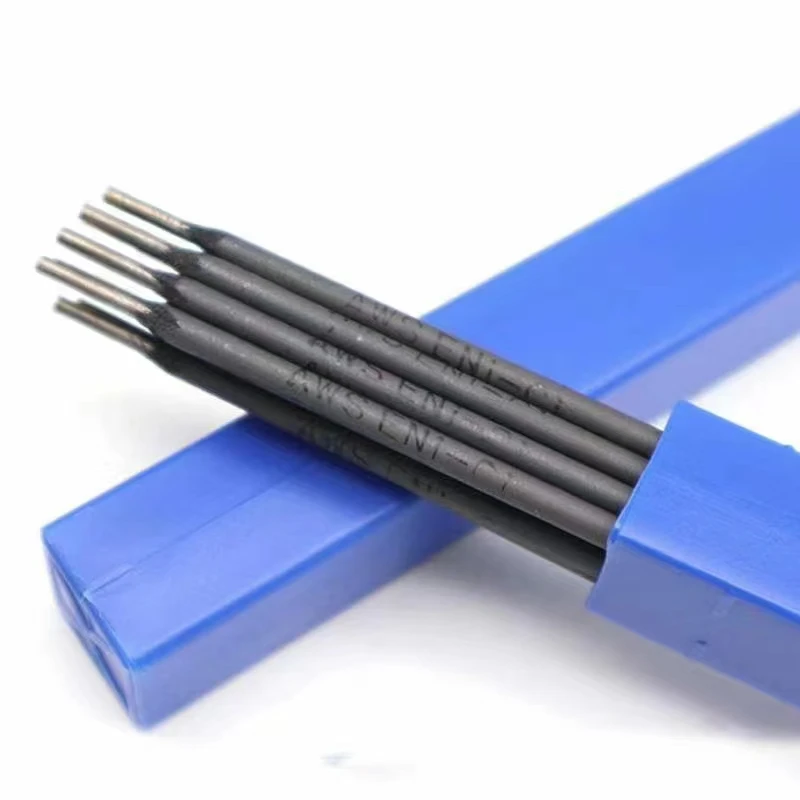
Within the realm of stainless steel welding,
the E308L 16 electrode is a recognized staple. This particular electrode is characterized by its low carbon content, formulated primarily for welding 18Cr - 8Ni and other stainless steels. The 16 denotes its usability with both alternating current (AC) and direct current electrode positive (DCEP), offering flexibility in diverse welding scenarios. The significance of understanding the amperage range is paramount for achieving optimal welding results and ensuring the longevity of the welded structure.
To delve deeper into its application, the E308L 16 electrode is best suited for welding Austenitic stainless types, known for their corrosion resistance, making them a staple in industries such as food processing, chemical production, and more. A crucial aspect of its usability lies in its amperage range which directly influences the weld quality. Typically, an amperage range between approximately 50 to 90 amps is preferred, but adjustments might be necessary based on the welding position and thickness of the materials involved. Adopting the correct amperage ensures a stable arc, reducing the likelihood of weld defects such as porosity or cracking.
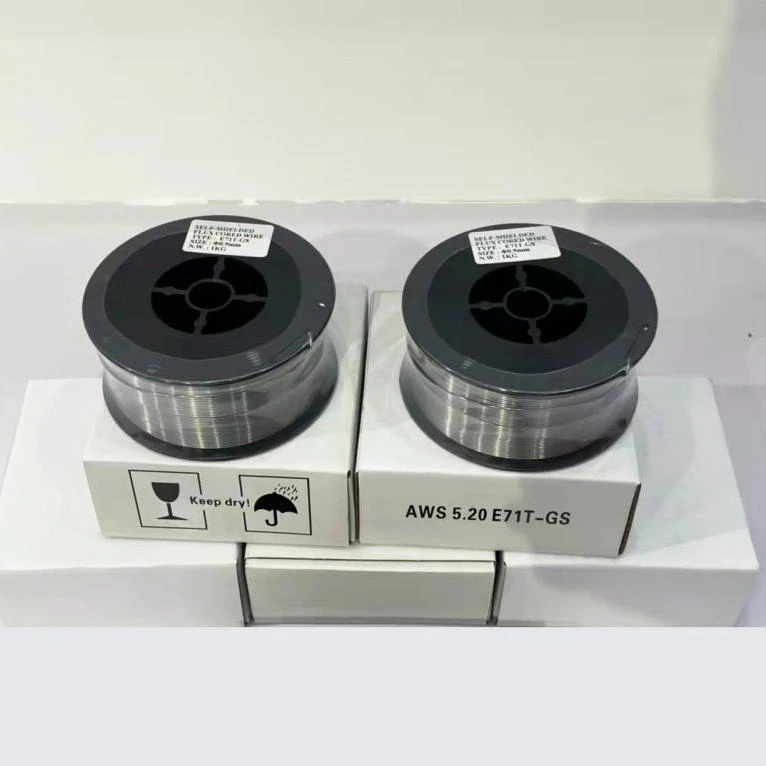
Using the E308L 16 electrode effectively involves mastering its application under varying operational conditions. For instance, when welding horizontal or flat surfaces, increased amperage might be beneficial to enhance penetration and weld formation. Conversely, for vertical and overhead positions, a lower amperage is advisable to manage the molten pool and prevent slag inclusions or dripping. Thus, comprehending the interplay between the electrode, the current, and the welding position enhances both the skill and safety of the operator, fostering confidence in one’s craftsmanship.
e308l 16 amps
Professional welders emphasize the importance of the correct settings to avoid common pitfalls. Overlooking the correct amp settings often results in overheating, damaging the electrode coating, which can lead to contamination of the weld. Such errors compromise the integrity of the weld, leading to potential failure under operational stresses. Therefore, conducting trial runs prior to major projects is advised to optimize settings that align with material specifications and project requirements.
Supplementing technical expertise with practical know-how elevates the credibility of any weld operation. Adherence to manufacturer specifications while remaining flexible and accommodating to individual project requirements establishes a benchmark for best practices in welding with E308L 16 electrodes. Additionally, one should prioritize personal protective equipment (PPE) to safeguard against the hazards of welding, including UV radiation and spatter, underscoring a commitment to comprehensive safety standards.
For a weld professional striving to refine their technique, understanding the intricacies of equipment and material is only the beginning. Continuous learning, practice, and adapting to the nuances of each project environment solidify one's standing as an authority in the field. The ability to leverage expertise with a mindset geared towards innovation and precision is what sets leaders apart in any technical domain.
To conclude, the correct use of E308L 16 electrodes, when coupled with a deep understanding of required amp settings, catalyzes not only superior weld quality but also enhances the efficiency and reliability of the welds. As such, cultivating an environment where knowledge sharing and adherence to industry standards are prioritized, establishes a foundation for credible, authoritative, and trustworthy welding practices.