When it comes to successful welding projects, selecting the appropriate welding rod size is crucial. Different welding rod sizes are designed to meet the demands of varying materials, joint designs, and project specifications. Understanding these sizes can drastically impact the quality of a weld, the time taken for a project, and ultimately, the structural integrity of the finished product.
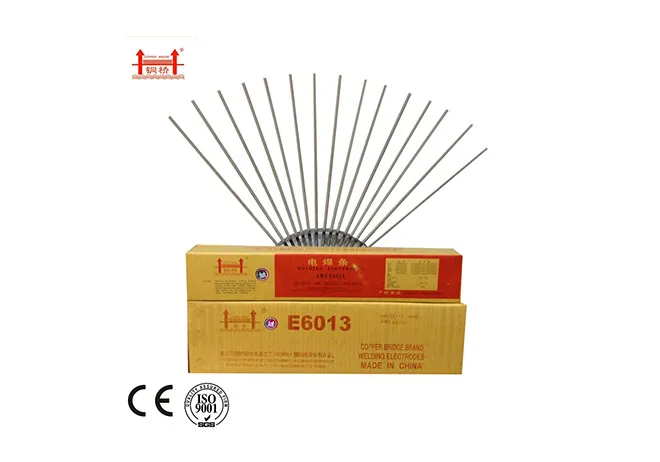
Welding rods, also known as electrodes, come in various diameters, each suited for different tasks. The diameter of a rod directly affects the heat input and the depth of penetration during welding. For instance, thicker rods are typically used for heavy industrial works that require deeper penetration and a larger weld bead, whereas thinner rods are more suited for delicate welds and thin materials.
The standard sizes for welding rods range from 1/16 inch to 3/8 inch in diameter, but the most commonly used sizes include 1/16, 3/32, 1/8, 5/32, and 3/16 inches. When working with thin metal sheets, opting for a smaller rod such as 1/16 or 3/32 inch is advisable as it reduces the risk of burn-through, providing better control over the weld. On the other hand, for thicker structures like structural beams or heavy machinery components, a 1/8 inch or larger rod would ensure proper fusion and strength.
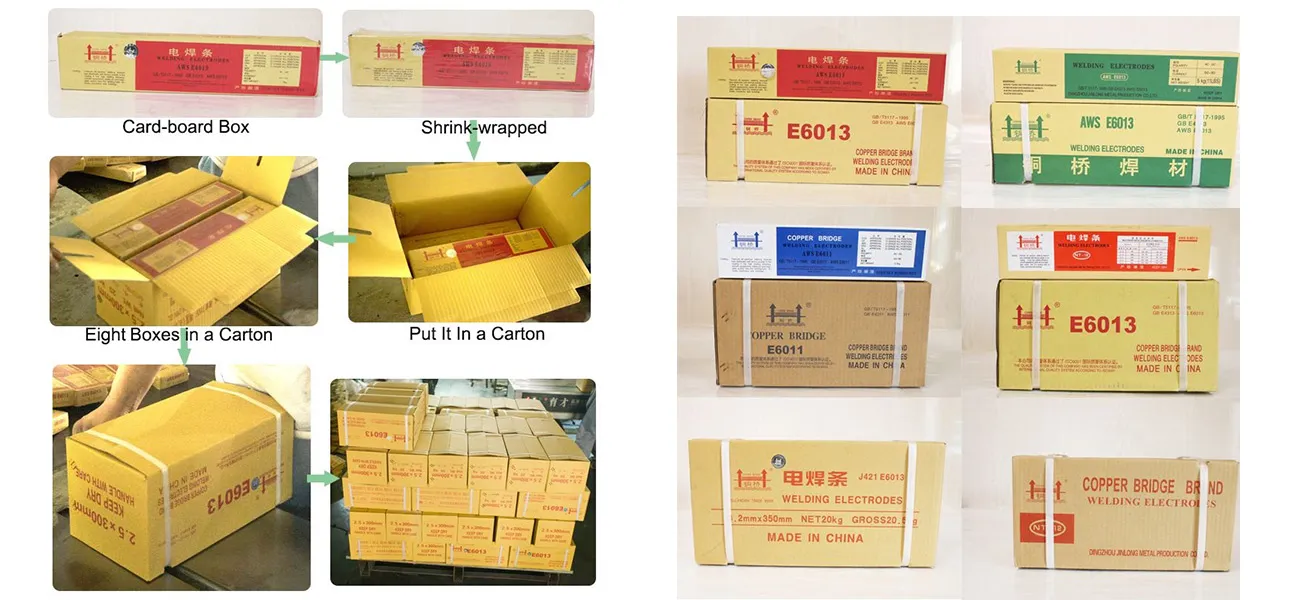
Understanding the application is paramount. In the automotive industry, for example, smaller rod sizes are favored for bodywork repairs to achieve precision and avoid unnecessary heat that could warp the sheet metal. In contrast, the construction industry might opt for larger rods that handle structural steel and support beams.
Moreover, welding positions significantly impact the choice of rod size. For overhead or vertical welding, a smaller rod provides better control and less filler metal fall-off. Position-specific welding rods, such as those used in vertical-up or vertical-down positions, may also come in various coating types, influencing their usability and the final weld quality.
different welding rod sizes
Each size comes with its own welding parameters. Amperage settings must match the rod size to optimize the arc stability and penetration. For example, a 3/32 inch rod typically runs on an amperage of 40-125, while a 1/8 inch rod might require 75-185 amperes. Mastering these parameters can lead to superior weld consistency and efficiency.
Selecting the proper welding rod size is not a one-size-fits-all decision. Factors such as base material, welding position, and desired mechanical properties must be carefully considered. An experienced welder or engineer will thoroughly assess these variables before making an informed decision. Testing different sizes in the preliminary stages of a project can also offer insights into the best match for a specific task, ultimately saving time and resources.
Industry standards and manufacturer's guidelines provide a great baseline for choosing the correct rod size, but expertise and experience should govern the final selection. Feedback from past projects, expert consultations, and continuous skill development play an integral role in honing the ability to make the right choice.
Investing time in understanding the nuances of different welding rod sizes and their application ensures high-quality welds that meet safety and performance standards. As technology in welding continues to advance, staying abreast of the latest rod sizes and innovations remains essential for any professional seeking to maintain a competitive edge in the industry.