Selecting the right welding rod for stainless to stainless welding is a pivotal decision for any welder seeking optimum results. Stainless steel, known for its anti-corrosive properties and aesthetic appeal, demands a welding process that preserves these qualities while ensuring strength and longevity.
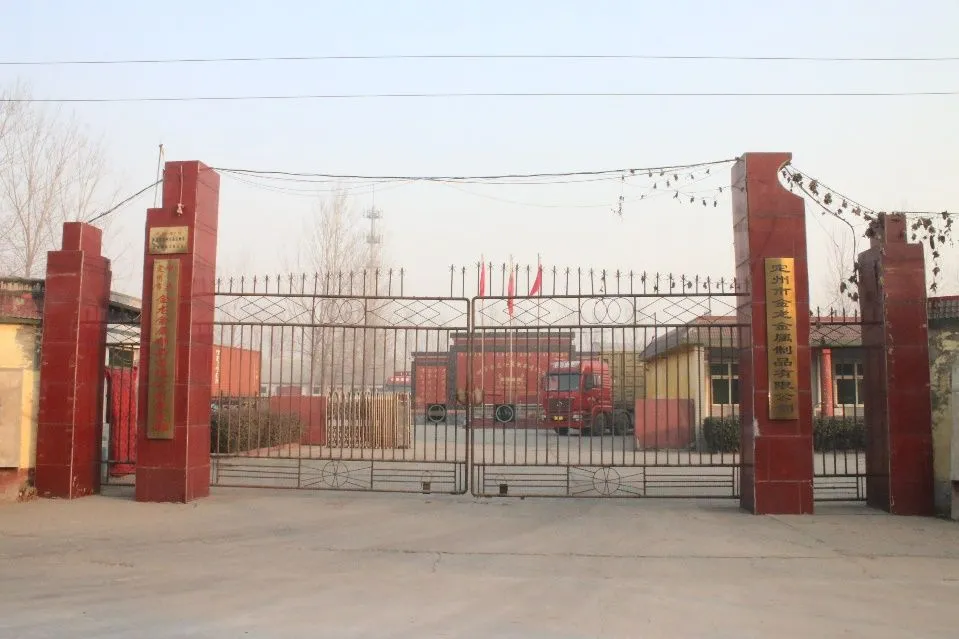
Understanding the nuances of stainless to stainless welding rods is crucial. The most commonly used rods for such applications are the 308L, 316L, and 309L, each serving unique purposes depending on the welding requirements. An in-depth understanding of these rods not only ensures the structural integrity of the welded components but also the surface finish, which is essential for various industries ranging from construction to culinary equipment.
The 308L rod is primarily used for welding similar base metals such as 304 stainless steel. This rod is praised for its low carbon content, which minimizes the risk of carbide precipitation during welding. This characteristic is particularly important to maintain corrosion resistance in environments where the welded steel is exposed to moisture or aggressive chemicals.

For situations involving more demanding conditions, such as exposure to marine environments, the 316L rod becomes indispensable. This rod contains molybdenum, an alloying element that enhances pitting and crevice corrosion resistance, qualities vital for marine structures or equipment handling salt water.
When welding dissimilar stainless steels, the 309L rod typically becomes the go-to choice. This rod is engineered to handle the thermal and mechanical disparities between different stainless steel grades, offering superior fusion and minimizing the risk of cracking.
stainless to stainless welding rod
Welding stainless to stainless involves precision and expertise. The welder must consider factors such as heat input, which should be carefully controlled to prevent warping and preserve the corrosion resistance of the stainless steel. Over-heat input can lead to discoloration and compromised material properties.
Furthermore, shielding gas selections play a critical role. Argon is often used as a primary shielding gas due to its inert properties, ensuring the weld pool is protected from atmospheric contamination. However, in certain applications, a combination of argon with a small percentage of hydrogen or nitrogen can enhance the weld's aesthetic and penetrate qualities, though these mixtures should be employed with caution.
Safety cannot be neglected when engaging in stainless to stainless welding. The welder must be equipped with appropriate gear to protect against UV radiation and harmful fumes. Adequate ventilation in the workspace is crucial to safeguard respiratory health, as welding stainless steel can release hexavalent chromium, a carcinogenic compound.
Lastly, post-weld treatment should never be overlooked. Depending on the application, processes such as passivation might be necessary to enhance the corrosion resistance of the welded structure. This process involves treating the stainless steel with a mild acid solution to remove contaminants and restore the chromium oxide layer, ensuring the welds are as durable and resistant as the parent material.
In conclusion, the choice of welding rod for stainless to stainless applications should be made with a deep appreciation of the specific requirements imposed by the project. Understanding the unique demands of the task, along with the properties of the various rods available, empowers welders to produce superior results that meet both functional and aesthetic standards. The expertise and attention to detail in selecting the right materials and adopting appropriate techniques echo through the longevity and performance of the welded stainless steel, reinforcing the industry's commitment to quality and innovation.