Choosing the right filler material is crucial in welding, especially when working with stainless steel materials. Stainless TIG (Tungsten Inert Gas) wire stands out due to its ability to produce precise, high-quality welds that are both aesthetically pleasing and structurally sound. Understanding the unique advantages and applications of stainless TIG wire can ensure optimal results in any welding project.
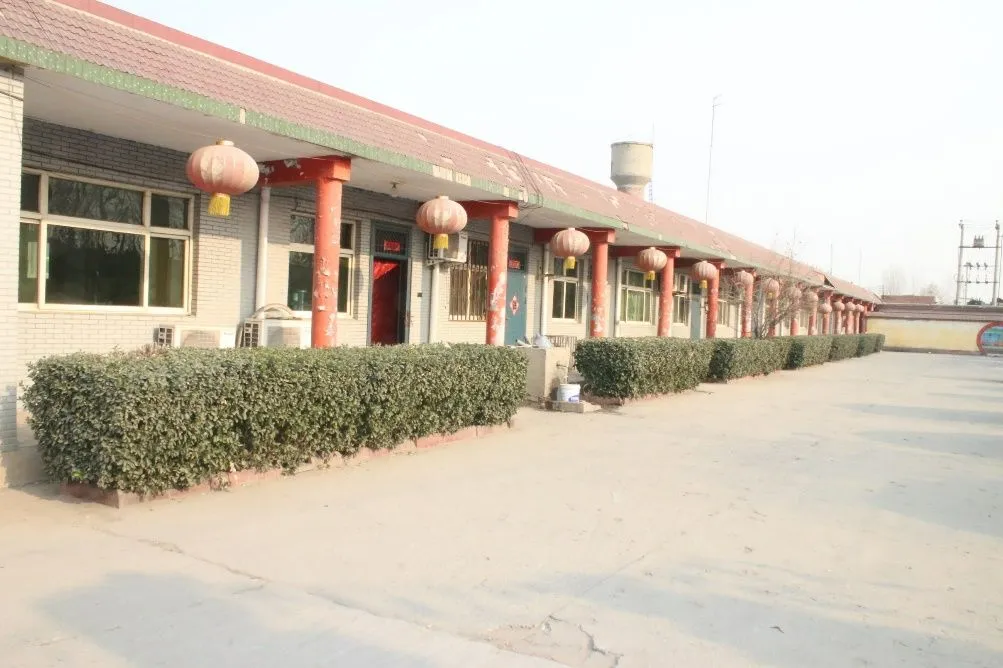
Stainless TIG wire is an indispensable tool for welders focused on crafting durable and corrosion-resistant joints. It is composed primarily of chromium-nickel alloys, which contribute to its impressive anti-corrosive properties, making it ideal for projects exposed to harsh environments. This characteristic is particularly advantageous in industries such as aerospace, automotive, and food processing, where stainless steel's longevity and resilience are essential.
One of the primary benefits of using stainless TIG wire is its ability to produce clean, precise welds. The TIG welding process employs a non-consumable tungsten electrode, and the addition of an inert gas, usually argon, shields the weld area from atmospheric contamination. This shielding protects the molten metal from oxidation and ensures the welded joint's purity and strength. Such precision is vital in projects where the appearance of the weld is as important as its function, such as in architectural and decorative applications.
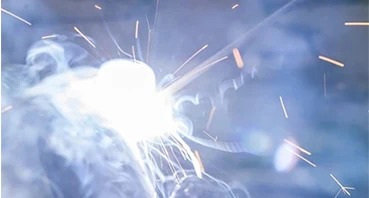
Expertise in handling stainless TIG wire involves understanding the importance of wire diameter and type selection, which vary depending on the welding project's specific requirements. For example, a project requiring structural strength may demand a thicker wire, whereas more delicate applications necessitate thinner wires for detailed work. Knowing the appropriate wire type is crucial to match the base materials being joined. Experienced professionals often opt for ER308L stainless TIG wire for joining 300-series stainless steels due to its low carbon content, minimizing carbide precipitation during welding, and maintaining corrosion resistance.
stainless tig wire
Trustworthiness is essential when selecting a stainless TIG wire supplier. A reputable manufacturer will ensure that the wire is manufactured to meet industry standards, such as those set by the American Welding Society (AWS). This compliance is crucial in guaranteeing that the wire performs consistently under various conditions, providing welders with the confidence needed to undertake critical applications. Collaborating with an experienced and trustworthy supplier can impact the overall success of a project significantly.
In addition to selecting high-quality materials, employing proper welding techniques is vital for achieving the desired outcomes. Welders must understand the nuances of heat input and travel speed when working with stainless TIG wire. Excessive heat can lead to warping or distorting the workpiece, while too low a temperature may result in weak welds. Balancing these parameters requires a blend of skill, experience, and understanding of the material's behavior under different thermal conditions.
For those entering the field or seeking to enhance their welding capabilities, investing in comprehensive training programs can build the expertise needed to excel. Such programs often cover topics like material selection, equipment usage, and troubleshooting common issues encountered during welding. Experienced mentors can provide invaluable insights that accelerate learning and refine techniques.
In conclusion, choosing stainless TIG wire as the filler material can elevate the quality and longevity of stainless steel welds. Its corrosion resistance and ability to create aesthetically superior welds make it a preferred choice for many industries. By selecting high-quality wires and refining welding techniques, professionals can ensure the durability and performance of their projects. As the field of welding continues to evolve, staying informed and connected with leading suppliers and educational resources will help maintain high standards and drive success in any ventures involving stainless TIG wire.