Welding rods are indispensable tools in the welding industry, serving as the core component in the creation of strong, durable metal bonds. The variety available, each designed for specific materials and conditions, can often confuse even seasoned professionals.
Understanding the nuances of different welding rods is crucial for achieving optimal results in welding projects.
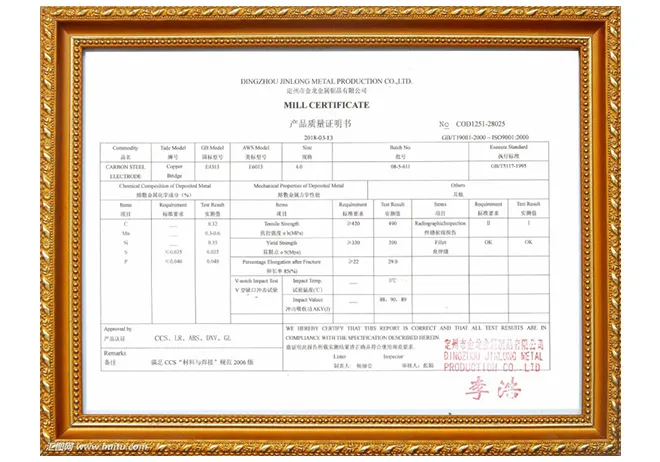
Electrode types form the foundation of welding, and choosing the right one involves consideration of the workpieces, the welding position, and the desired weld properties. Let's delve into the fundamental categories and their applications.
Firstly, mild steel electrodes, such as the ubiquitous E6010 and E6011, are favoured for their deep penetration and are particularly useful where rust, dirt, or other impurities need to be tolerated. These rods are ideal for pipe welding and structural work, with E6010 offering a more aggressive, penetrating arc and E6011 providing an AC option for less industrial power sources.
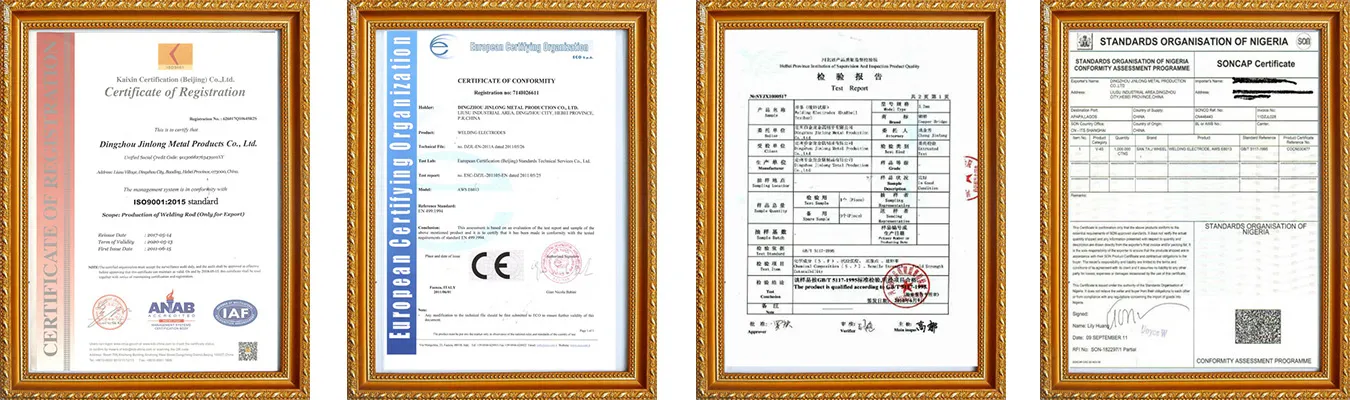
For applications requiring smoother welds and higher tensile strength, such as in high-pressure environments, low hydrogen electrodes like the E7018 are preferable. They produce welds with less risk of cracking and enhanced ductility. The E7018 rods are instrumental in structurally critical projects, including the construction and maintenance of bridges and buildings.
Stainless steel electrodes cater to environments that demand corrosion resistance and aesthetics. Their seamless ability to join various grades of stainless steel makes them invaluable across industries that operate in corrosive conditions such as food processing or chemical plants. The 308L and 316L electrodes are noteworthy for their use with their respective stainless steel types, ensuring welds maintain integrity under stress and strain.
all types of welding rods
Aluminum electrodes, demanding in their approach, have specialized formulations like the E4043, which is essential for welding wrought and cast aluminum structures. Known for its ease of flow and minimal spatter, E4043 ensures a neater weld appearance, key in visible weld applications like vehicle frames and hulls in marine settings.
For those working with cast iron, ensuring the welding rod's compatibility with iron content is critical. Nickel-based electrodes, like Ni-Cl and Ni99, can't be overlooked, as they're specifically designed to address issues like cracking or excessive hardness found with other materials. These rods are quintessential for repairing or joining cast iron machinery, where exposure to severe working conditions is routine.
Specialty rods, designed for hard-facing or alloy welding, focus on enhancing surface resistance or restoring worn-out parts. Such electrodes help prolong the service life of industrial machinery faced with high abrasion or impact scenarios, showcasing their application in industries like mining or forestry.
The authoritative knowledge on welding rods elevates one's approach to welding, guiding an informed decision-making process. Expert welders recognize that the harmonious choice of electrode and technique ultimately affirms the safety, aesthetics, and longevity of their projects. It is this genuine understanding of welding rods, harmonized with practical application, that transcends mere technique into artistry, ensuring virtually flawless outcomes and reinforced trust in one's professional capabilities.