Exploring the various types of electrodes utilized in welding unveils the vastness and specificity required in selecting the right materials for successful outcomes. Welding electrodes, primarily categorized into consumable and non-consumable, serve an indispensable role in both industrial and intricate welding processes, each with unique characteristics suited to different tasks and metal types.

Consumable electrodes are predominantly used in shielded metal arc welding (SMAW), also known as stick welding. One of the most commonly used electrodes in this category is the E6010, known for its ability to penetrate deeply, making it ideal for welding on unclean or rusted surfaces. E6010 electrodes are typically employed in construction projects crucial for their tensile strength and adaptable nature. Another prevalent consumable electrode is the E7018, renowned for its ease of use and smooth bead appearance. This low-hydrogen electrode is preferred for welding applications requiring high impact resistance and strength, such as in structural welding and pipelines.
In contrast, non-consumable electrodes, like those used in tungsten inert gas (TIG) welding, are vital for precision tasks. Tungsten electrodes do not melt during the welding process, allowing for superior control and detailed craftsmanship. Available in variations such as pure tungsten or tungsten mixed with rare earth oxides like thorium, lanthanum, and cerium, each offers distinct advantages. For example, thoriated tungsten electrodes are famous for their excellent arc start and longevity, suitable for welding thin metals due to their stability and heat resistance.
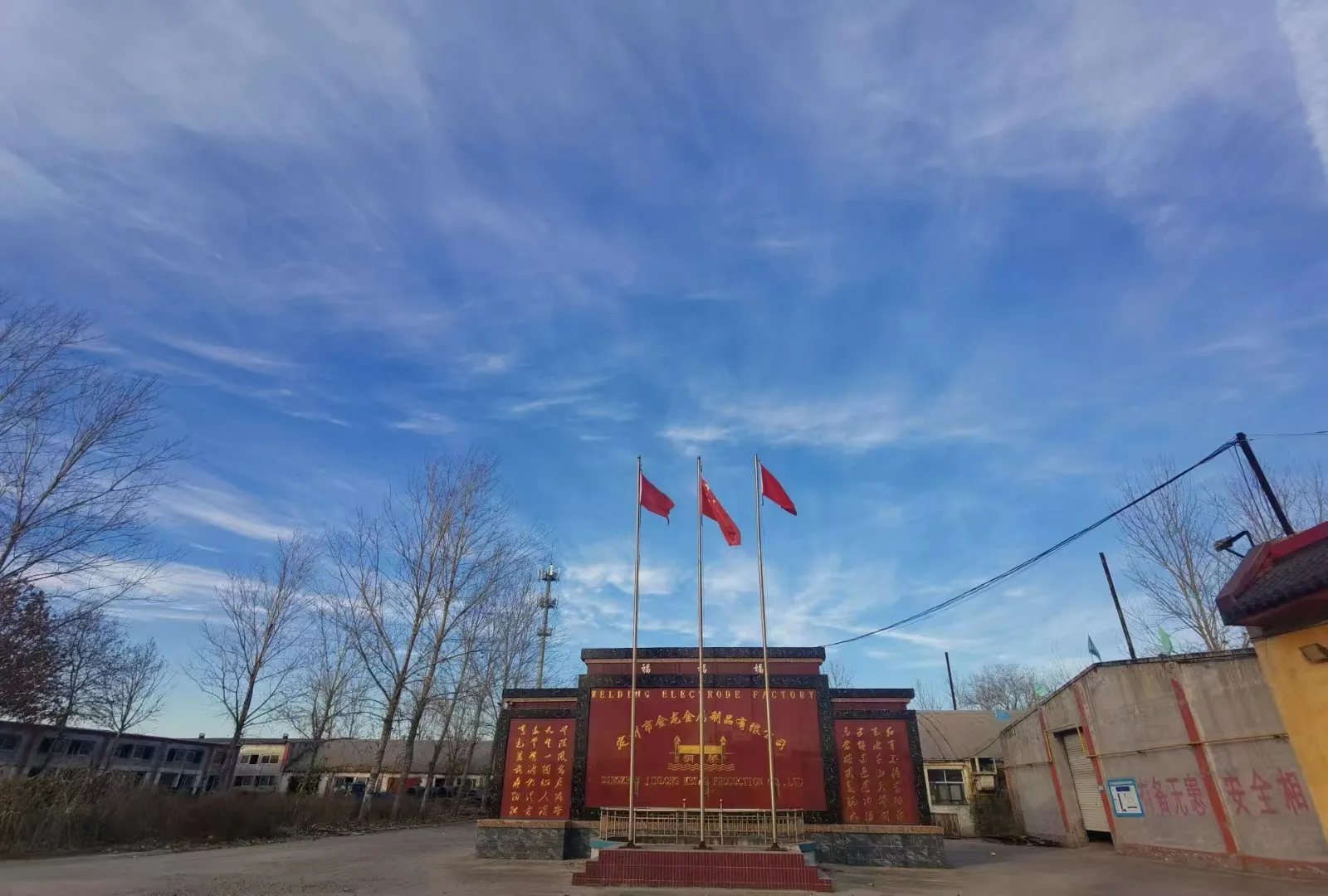
Moving towards advanced types,
flux-cored electrodes provide the flexibility of welding outdoors even in adverse conditions. Thanks to their flux core, they can perform without shielding gas, making them a popular choice for projects that demand mobility and efficiency, such as repair works and field construction. Self-shielding flux-cored electrodes further simplify outdoor tasks, eliminating the need for gas bottles and making transportation less cumbersome.
types of electrodes welding
Other specialized electrodes like the aluminum and stainless steel types cater to niche markets. Aluminum electrodes are essential in combining aluminum parts or repairs, characterized by corrosion resistance and lightweight properties. However, their handling requires expertise due to their conductive nature and oxidation tendencies. Similarly, stainless steel electrodes are sought after for their anti-corrosive properties, ideal for applications in environments exposed to acids or other harsh substances.
In the realm of welding electrodes, understanding and leveraging their varieties translates to optimizing performance, cost-efficiency, and output quality in diverse applications. Professionals with hands-on experience emphasize the importance of selecting the correct type, factoring in the material, environment, and demands of each project, reinforcing expertise in maneuvering these complex choices. Also, adherence to safety standards and regular equipment calibration is imperative, instilling trust and authority in every welded joint executed.
With advancements in technology, welding electrodes continue evolving, introducing hybrid varieties boasting enhanced features and catering to ever-changing industry needs. Welding specialist forums and certification programs increasingly advocate continuous skill enhancement, ensuring competitiveness amidst dynamic market scenarios. Therefore, for enthusiasts and seasoned welders alike, diving deep into the comprehensive world of welding electrodes proves to be a cornerstone of metallurgical mastery.