TIG welding, an abbreviation for Tungsten Inert Gas welding, is an arc welding process that uses a tungsten electrode to produce the weld. When it comes to working with stainless steel, the choice of the right TIG electrode is crucial for achieving high-quality welds with desirable mechanical properties. Today, experts in the field are shedding light on the types of electrodes best suited for stainless steel applications, their unique properties, and best practices to enhance your welding experience.
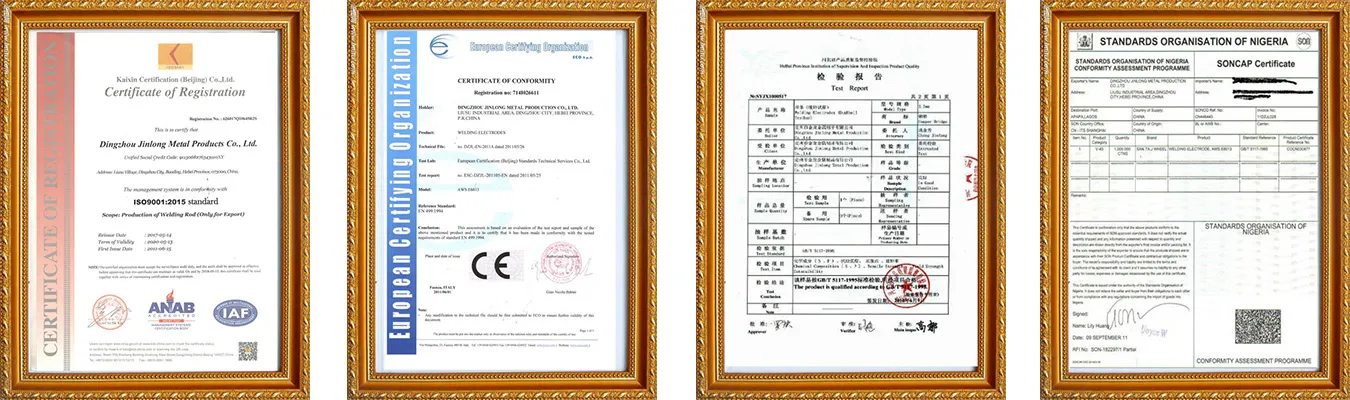
Stainless steel, with its corrosion-resistant nature and desirable strength, is a staple material in many industries, ranging from aerospace to medical. However, its weldability requires a meticulous approach, especially when considering the ideal TIG electrode. Among the most commonly recommended options is the 2% thoriated tungsten electrode (designated as EWTh-2), known for its excellent arc-starting capabilities and consistent performance. Despite its radioactive nature, many professionals prefer it due to its ability to handle high current loads and provide stable arcs.
Another popular choice is the ceriated tungsten electrode, around 2% cerium oxide (EWCe-2). Characterized by its ease of striking an arc with lower amperages, this electrode is particularly effective in thin-section stainless steel applications or delicate operations where heat input must be controlled. Ceriated electrodes are lauded for their performance in DC welding and their non-radioactive nature, which makes them safer to handle.
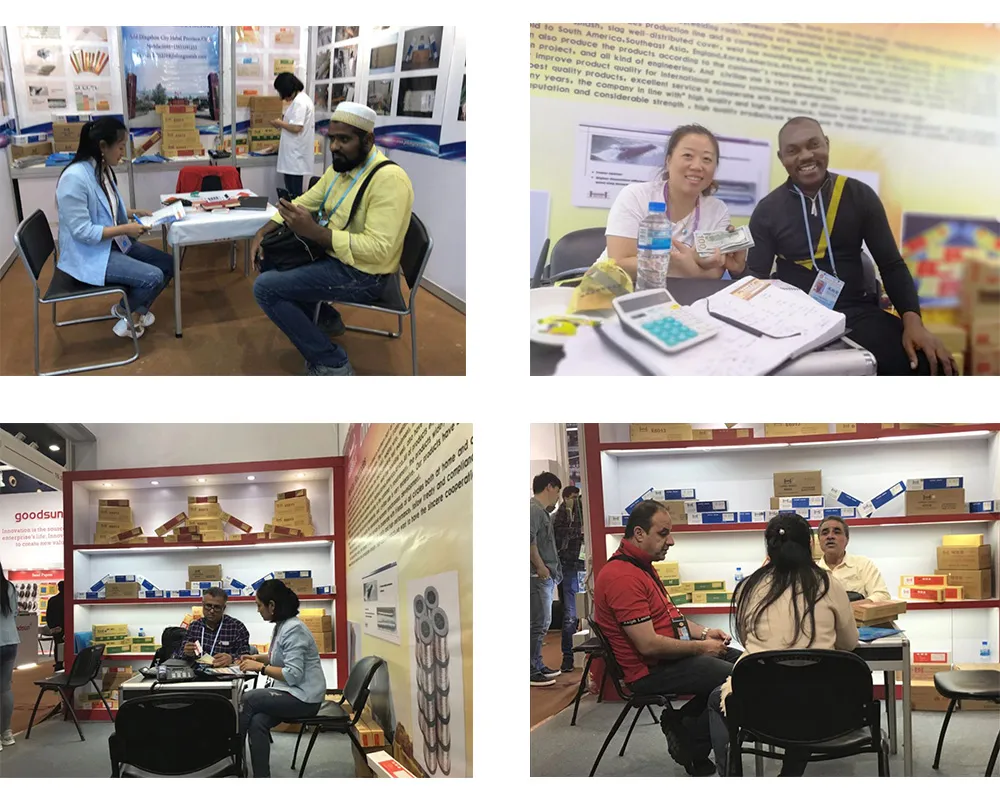
For those seeking a versatile option, the lanthanated tungsten electrode (1.5% lanthanum oxide, EWLa-1.5) offers a balance of arc stability, ease of use, and longevity. This electrode proves to be a worthy contender for stainless steel projects that demand repetitive arc starting and longer life in both AC and DC welding modes.
When selecting the appropriate electrode, attention must also be given to its diameter. The thickness of the stainless steel being welded often dictates the required electrode diameter. For materials up to 1.5mm, a 1.6mm electrode is usually sufficient, while thicker materials up to 6mm might need a 2.4mm electrode. Recognizing this crucial aspect enhances weld quality, reduces contamination risks, and minimizes unexpected costs due to electrode consumption.
tig electrode for stainless steel
Experienced welders emphasize the significance of maintaining a clean tungsten surface. Any contamination can lead to a compromised arc, spatter, and weld defects. Regular dressing of the electrode, ideally before each use, is advised. Sharpening the tungsten electrode to a precise point, ensuring it meets the required shape for your specific application, is pivotal in achieving smooth and stable arcs.
Furthermore, the implications of an inert gas supply cannot be overlooked. Argon, being the most commonly used shielding gas, provides a smooth stable arc and minimizes oxidation.
Pure argon is generally suitable for most stainless steel welding tasks. Nevertheless, some professionals opt to mix a small percentage of hydrogen with argon to achieve deeper penetration and improved weld pool fluidity, particularly for austenitic stainless steels.
Every TIG welding enthusiast understands that perfecting their craft involves not only mastering the settings and techniques but also continually refining their choice of equipment. Feedback from across the welding community uniformly underscores the experience of having the right electrode as being paramount to achieving superior welding results efficiently and effectively on stainless steel.
In conclusion, selecting the appropriate TIG electrode plays a quintessential role in the successful welding of stainless steel. While traditionally favored options like thoriated tungsten bring certain benefits, ceriated and lanthanated variants offer safer and often more versatile alternatives. Ultimately, the choice hinges on the specific requirements of the project at hand, underscored by the welder's expertise and preference. As technical advancements continue to evolve, staying informed about electrode characteristics ensures that welders remain prepared for the challenges presented by modern stainless steel applications.