Selecting the right stainless steel welding rod is a crucial decision in ensuring the integrity, durability, and performance of a welded structure. With myriad options available, the choice can seem daunting, often compounded by misinformation and varying opinions. A comprehensive understanding of the selection process for stainless steel welding rods can ensure that each weld meets the highest standards of quality and safety.
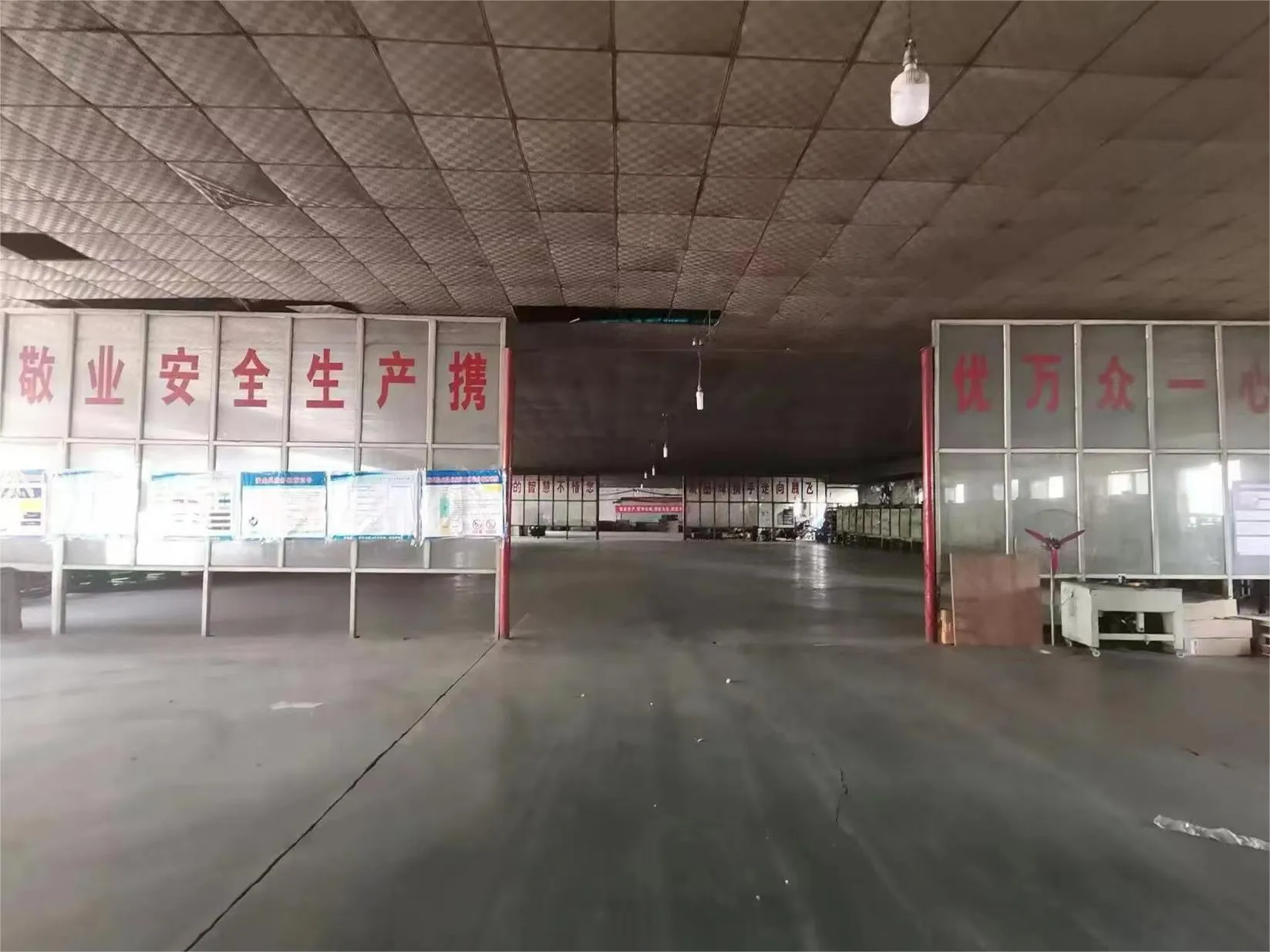
Stainless steel is renowned for its corrosion resistance, strength, and aesthetic appeal, which varies widely among different grades. Therefore, the first step in selecting a welding rod involves understanding the specific properties of the stainless steel being used. Common grades include 304, 316, and 409 stainless steels, each possessing distinct characteristics that affect their behavior when welded. Identifying the base material enables the proper matching of welding rods, thereby preventing potential issues like corrosion or cracking.
Welding professionals advocate for matching the filler material, i.e., the welding rod, with the base metal to maintain weld integrity. The 308L rod is a popular option for welding 304 and 304L stainless steels since it is designed to minimize the risk of carbon precipitation, which can lead to intergranular corrosion. For 316 and 316L stainless steels, the 316L welding rod is preferred because it offers molybdenum content that enhances corrosion resistance, particularly in chloride environments. It is this attention to detail and material compatibility that safeguards against premature failure and ensures long-term durability.
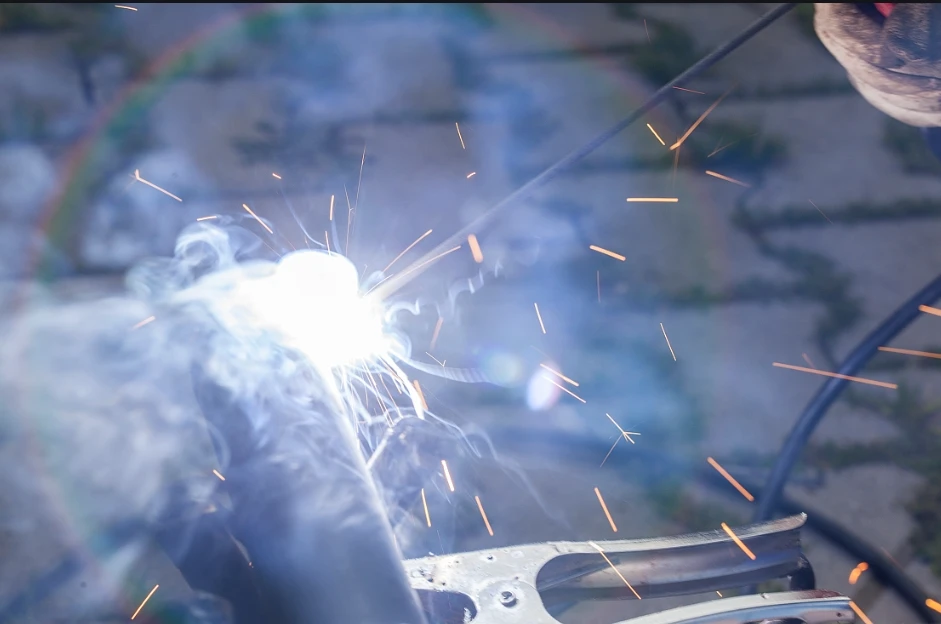
Positioning is another factor to consider in welding rod selection. Different rods are engineered for varying welding positions—flat, vertical, horizontal, and overhead. The physical properties of the rod, including diameter and coating, can influence the ease with which a welder operates in these positions. Choosing the right rod for the position not only simplifies the welding process but also contributes to achieving cleaner, stronger welds with reduced defects.
stainless steel welding rod selection
Sustainability and the working environment are becoming increasingly significant in material selection, affecting how welding rods are chosen. Some rods are specifically formulated to produce minimal spatter and smoke, which is critical in maintaining a healthy workspace and reducing the welder's exposure to potentially harmful emissions. With the growing emphasis on eco-friendly practices, opting for rods that reduce waste and require fewer resources for cleanup aligns with broader environmental goals.
Expert welders also stress the importance of considering the welding process itself, whether it is shielded metal arc welding (SMAW), gas tungsten arc welding (GTAW), or flux-cored arc welding (FCAW). Each process has specific rod types tailored to optimize welding performance and efficiency. For GTAW, for instance, the pureness of the rod and its thickness can significantly impact the precision and quality of the welds produced, often employing rods such as ER308L for stainless steels due to its effectiveness in preventing oxidation and maintaining weld integrity.
Testing and certification stand as critical aspects reflective of the trustworthiness of the materials used. Ensuring that the welding rods being selected comply with industry standards and undergo rigorous testing processes builds confidence in their performance. Certifications from recognized bodies confirm their suitability for specific applications, refine welding practices, and meet governmental and industrial regulations, thus instilling a sense of reliability in each project.
True expertise in welding encompasses not just the technicalities but also the safety, economy, and sustainability aspects of the job. Selecting the appropriate stainless steel welding rod is a testament to professional diligence and commitment to quality. By leveraging comprehensive knowledge and making informed decisions, welders can achieve superior results that speak to their skill and understanding, setting benchmarks of excellence in metalworking craftsmanship.