Selecting the right welding rod for cast iron is crucial to ensure strong, durable joints that maintain the integrity of the piece. While welding cast iron can be challenging due to its brittle nature and propensity for cracking, understanding the right electrode choice can empower both novice and seasoned welders alike to achieve superior results.
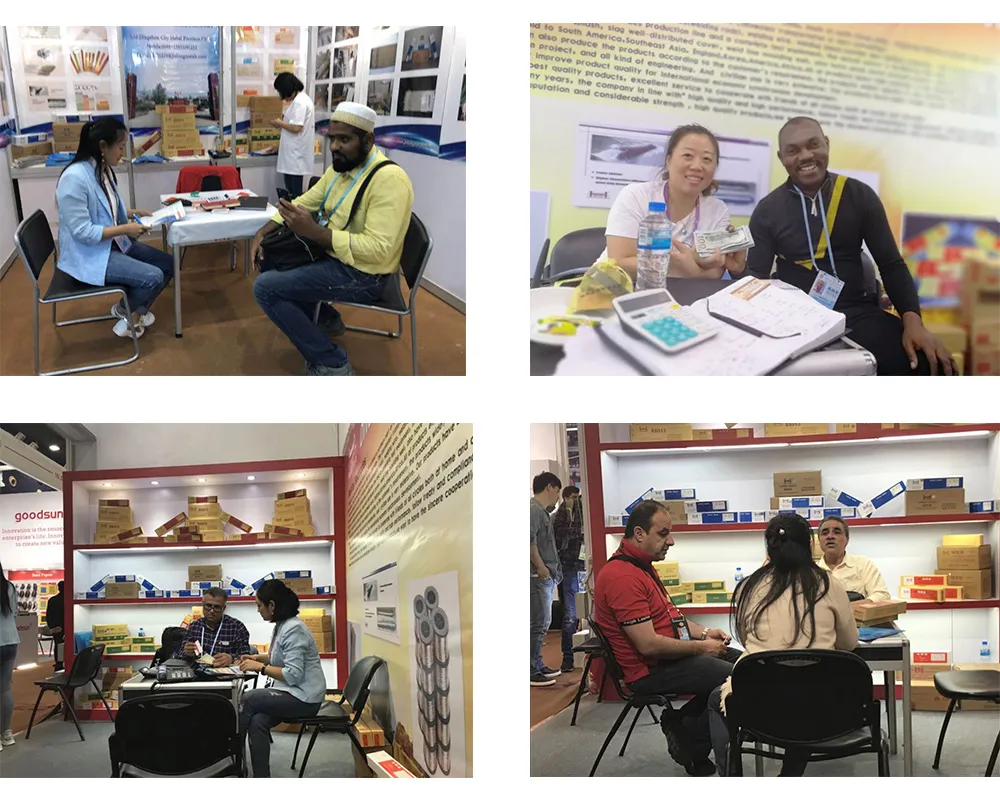
The nature of cast iron, a high-carbon alloy containing various forms of iron, carbon, and silicon, makes it prone to issues like cracking and stress fractures when welded improperly.
Choosing an appropriate welding rod mitigates these problems by providing compatibility with cast iron's distinct characteristics.
Nickel-based Electrodes
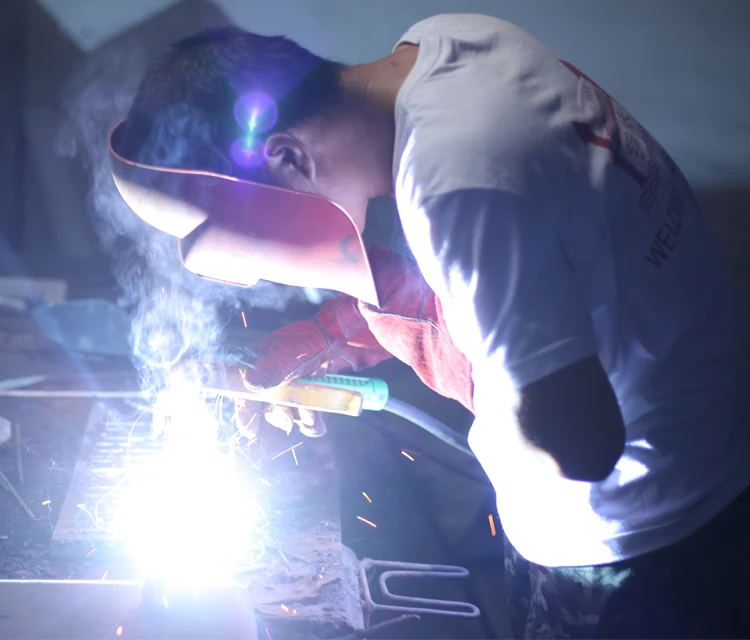
Nickel-based electrodes are often the top choice for welding cast iron. These rods help create welds that are strong and flexible, accommodating the inherent brittleness of cast iron. Nickel 99 (ENi-CI) and Nickel 55 (ENiFe-CI) are the most commonly used electrodes.
Nickel 99 rods consist of 99% nickel content, producing soft, machinable welds which absorb thermal expansion. Ideal for applications requiring the weld area to be machined afterward, they are particularly beneficial in joining thin cast iron pieces.
Nickel 55 rods, with 55% nickel content, strike a balance between strength and ductility, offering solid welds for thicker sections of cast iron. Although they have reduced machinability compared to Nickel 99, they are more cost-effective and still offer good thermal expansion absorption.
Steel-based Electrodes
Steel electrodes, while less common, also have applications in cast iron welding, particularly in cases where machinability is not a priority, and cost constraints exist. These rods create a harder, more brittle weld, requiring post-weld heat treatments to relieve stress and minimize cracks.
Low Hydrogen Electrodes are another option, producing strong, crack-resistant welds. However, the challenge lies in controlling graphite formation, which can lead to brittleness if not managed through careful temperature regulation and pre/post-welding heating techniques.
Welding Techniques and Considerations
which welding rod used in cast iron
Welding cast iron successfully with these electrodes involves more than just the right rod choice. Follow these key techniques for optimal performance
1. Preheat and Post-Heat Gradually heating the cast iron before welding helps reduce thermal shock, and post-heating allows for controlled cooling, minimizing the risk of cracking.
2. Short Welds and Peening Short, controlled welds distributed evenly across the joint prevent heat build-up. Peening the welds as you go can also help to relieve stress.
3. Slow Cooling Allowing the welded cast iron to cool slowly, ideally in an insulated environment, prevents rapid contraction that can lead to cracks.
4. Cleaning and Preparation Ensuring the base metal is clean and free from contaminants is essential. Grind out any damaged material to create a fresh surface for a productive weld.
Trust and Credibility in Selecting Welding Rods
The choice of welding rod reflects not just the technical requirements of the task but also considerations of reliability and trust in the products and processes used. Utilizing trusted brands and consulting industrial standards and expert recommendations reinforces the welding process's credibility.
In addition to product choice, continual professional development—staying updated with the latest industry practices and material innovations—is crucial in maintaining expertise. Engaging with professional welding communities and forums also provides a wealth of experiential knowledge, highlighting practical insights and personal testimonies from seasoned welders.
Conclusion
Achieving success in welding cast iron involves a combination of selecting the right electrode and implementing meticulous welding techniques. Nickel-based electrodes stand out for their compatibility and ease of use, while steel-based options cater to specific project parameters and budget considerations. By fostering expertise through knowledge, experience, and community engagement, welders can confidently and effectively tackle the complexities of cast iron welding, resulting in robust and reliable welds that stand the test of time.