Arc welding is a versatile technique employed across various industries, and the choice of welding rod is critical to achieving optimal results. For devices operating on Alternating Current (AC), certain welding rods stand out due to their performance and compatibility with AC currents.
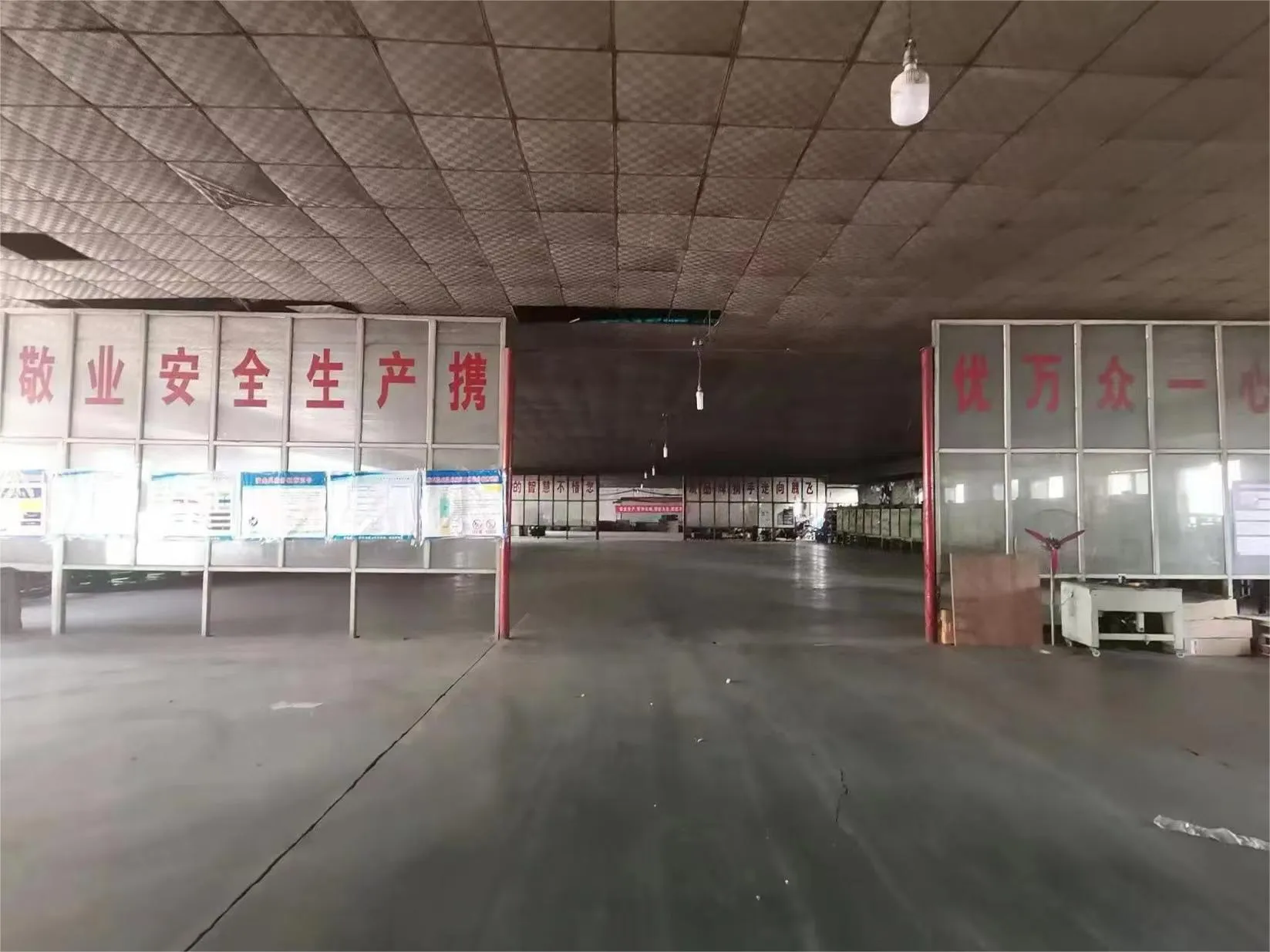
The 6011 welding rod is particularly notable for its effectiveness with AC welding machines. It's designed for deep penetration and fast freezing, making it ideal for vertical and overhead positions. One of the significant advantages of the 6011 rod is how it handles dirty or rusty surfaces while maintaining robust structural integrity. This makes it a popular choice for maintenance and repair work.
Joining it in popularity is the 7018 AC welding rod, known for producing smooth, strong welds with low hydrogen content. The 7018 is often utilized in construction due to its excellent mechanical properties and its ability to prevent cracking. Despite being traditionally suited for DC operations, special formulations of the 7018—designed specifically for AC—allow craftsmen to enjoy the same benefits using an AC power source.
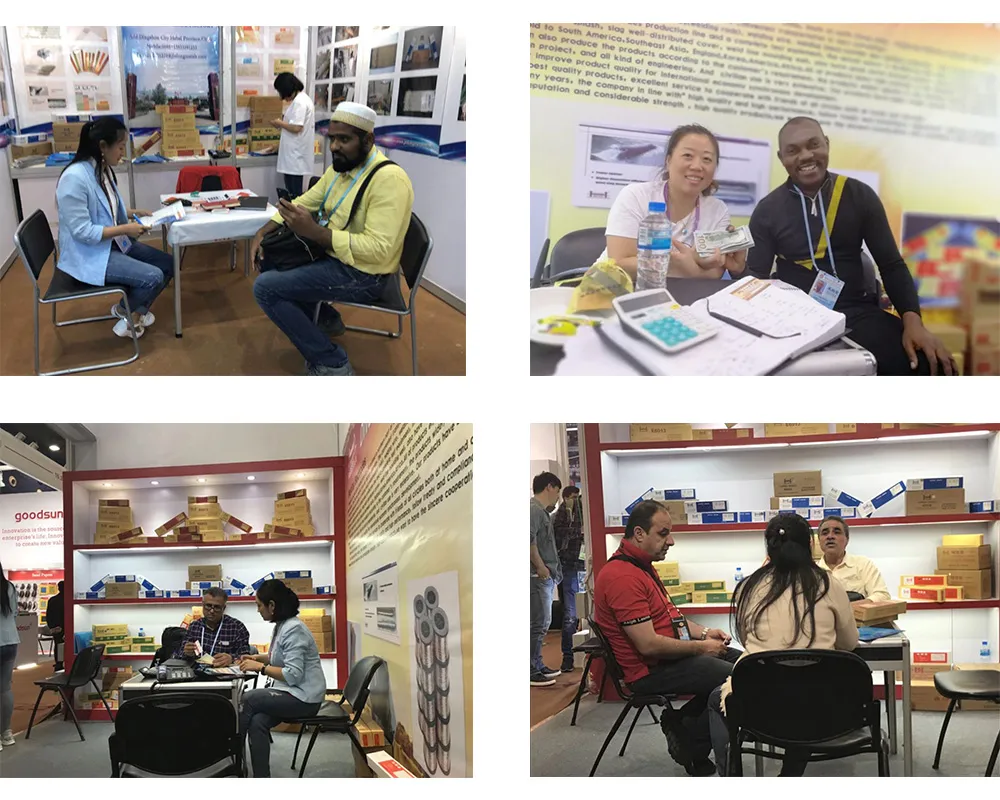
Errors in rod selection can lead to poor penetration, weak welds, or excessive spatter. Therefore, understanding the context of your welding project helps ensure you select the most appropriate rod. For instance, when working on steel structures that must endure substantial stress, a 7018 is typically advised due to its robustness and ductility.
While these rods are among the most efficient for AC, they can present challenges without proper technique or equipment. Preheating the workpiece might be required to reduce the risk of cracking when using rods like the 7018. Moreover, ensuring the welding machine is properly calibrated and using dry, well-maintained rods can prevent issues such as porosity or lack of fusion.
what welding rods are ac
Experienced welders often emphasize the importance of understanding voltage settings and maintaining a consistent arc length. This expertise is critical, as too much arc length with AC welding can lead to increased spatter and undercutting. Practicing these elements can markedly improve the quality and appearance of the weld.
Welders also weigh environmental factors when selecting AC welding rods. If working outdoors in an exposed or windy environment, the versatility and resilience of the 6011 rod make it a dependable choice as it withstands such conditions, keeping the arc stable and minimizing electrode sticking.
Industry professionals continually explore advancements in materials and technology, often seeking to optimize efficiency and safety. Modern coatings on electrodes, for instance, are designed to stabilize the arc and improve operability, ensuring clean welds even under challenging conditions.
Connecting with the field's recognized experts through courses or certifications can deepen one’s understanding. Agencies such as the American Welding Society provide standards and certifications that validate skill levels and knowledge in selecting and operating various welding rods effectively.
Ultimately, selecting the appropriate welding rod when working with AC currents is as much about understanding the materials as it is about the technique. The 6011 and AC 7018 are standard-bearers in the field, offering proven reliability and efficiency. Through continuous learning and application of best practices, welders can assure quality and safety in every project they undertake.