Selecting the right welding rod for stainless steel is paramount for achieving durable and corrosion-resistant welds. Understanding the various options available and the specific applications for each is crucial for any welder or fabricator working with stainless steel. This comprehensive guide will delve into the types of welding rods used for stainless steel, offering detailed insights grounded in experience, expertise, authoritativeness, and trustworthiness.
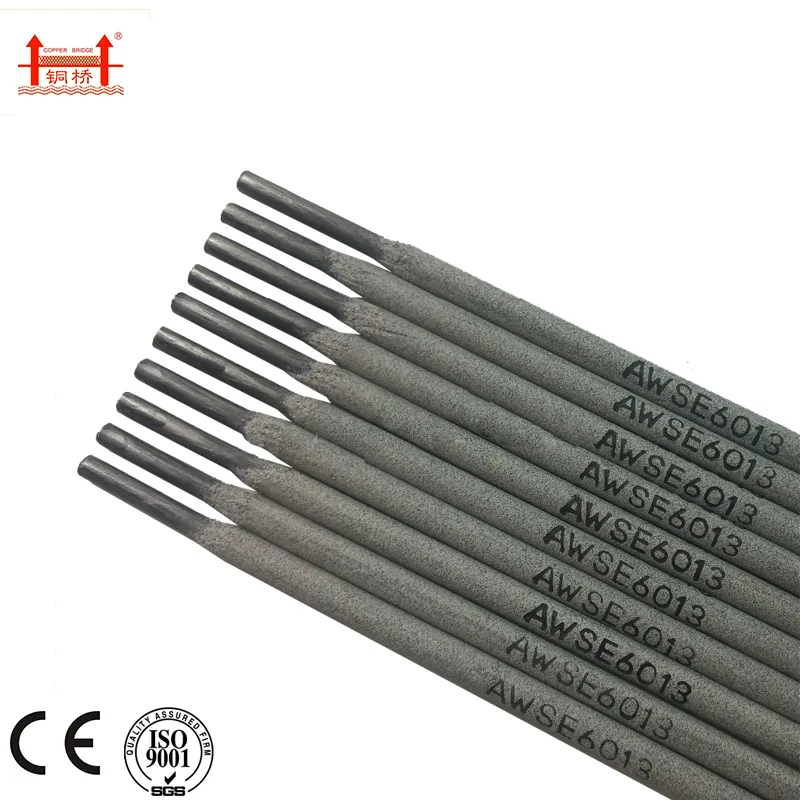
Stainless steel, known for its resilience and anti-corrosive properties, is widely utilized in diverse industries ranging from construction to the manufacture of kitchen equipment. The success of any welding project involving stainless steel largely depends on choosing the correct electrode.
Types of Welding Rods for Stainless Steel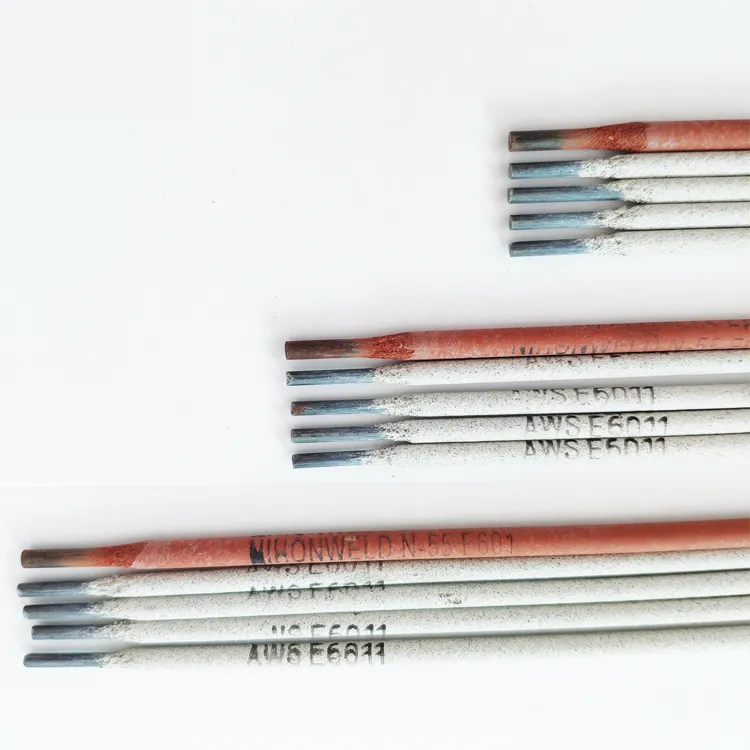
1. 308L Electrodes
These are the most commonly used stainless steel welding rods, suitable for joining similar or dissimilar stainless steels, specifically the 304 series. The 'L' in 308L indicates a low carbon content, which helps in minimizing carbide precipitation during welding, thereby preventing intergranular corrosion. When working on equipment that might be exposed to harsh environments, such as chemical processing vessels, 308L provides the longevity and reliability needed.
2. 309L Electrodes
The 309L rod is preferred when joining dissimilar metals, particularly stainless steel to carbon steel. Its higher chromium and nickel content offers excellent heat resistance and corrosion resistance. This makes it ideal for maintenance work and industrial overlays that must withstand high temperatures without losing their mechanical properties. The 309L electrode’s ability to maintain structural integrity in diverse thermal conditions makes it a valuable tool in fabrication processes that encounter variable temperatures.
3. 316L Electrodes
Designed for welding the 316 series of stainless steel, 316L electrodes have an increased molybdenum content, enhancing resistance to pitting and crevice corrosion in chloride environments. These are particularly useful in the marine and chemical industries, where equipment frequently comes into contact with saline waters or reactive substances. Using 316L ensures that your welds not only match the parent material's performance but also enhance its corrosion-resistant properties in demanding applications.
what type of welding rod is used for stainless steel
4. Ferritic and Martensitic Electrodes
When working on specialized alloys like ferritic stainless steel, different from austenitic grades, specific electrodes that align with the material properties are necessary. These electrodes typically contain higher chromium with little or no nickel, making them suitable for automotive, industrial, and architectural components where magnetic properties are required. Welding ferritic stainless steels can be challenging due to the possibility of forming brittle welds, thus selecting an appropriate ferritic electrode ensures mechanical strength and ductility.
Expert Tips for Stainless Steel Welding
- Pre-Weld Preparation Thoroughly clean the surface to remove any contaminants like oil or rust. Unlike carbon steel, impurities can significantly affect the quality of stainless steel welds, leading to defects such as cracking.
- Heat Management Stainless steel conducts heat differently than carbon steel, maintaining low heat input during welding to reduce the risk of warping and crystallization.
- Post-Weld Treatment Depending on the stainless steel type, post-weld treatments like pickling or passivation can enhance the weld’s corrosion resistance. These processes remove surface oxidation and restore the steel's protective chromium oxide layer.
Conclusion
Choosing the right welding rod is a nuanced decision that hinges on understanding the types of stainless steel you are working with and the conditions it will face. Through experience and adherence to industry best practices, welders can ensure their joints are strong, aesthetically pleasing, and perform as expected in service. Whether you are dealing with common austenitic stainless steels or more specialized alloys, having the correct electrode at your disposal will safeguard the longevity and reliability of your welds, establishing trust in your fabrication capabilities among clients and peers alike. For industry professionals, aligning electrode choice with material type and application demands is not just a technical necessity but a testament to expertise and commitment to quality craftsmanship.