Welding without conventional electrodes might seem like an impossible task to those unfamiliar with the latest advancements in the welding industry. However, this innovative approach, known as friction stir welding (FSW), has revolutionized the way we join materials, offering numerous benefits and applications across various sectors.
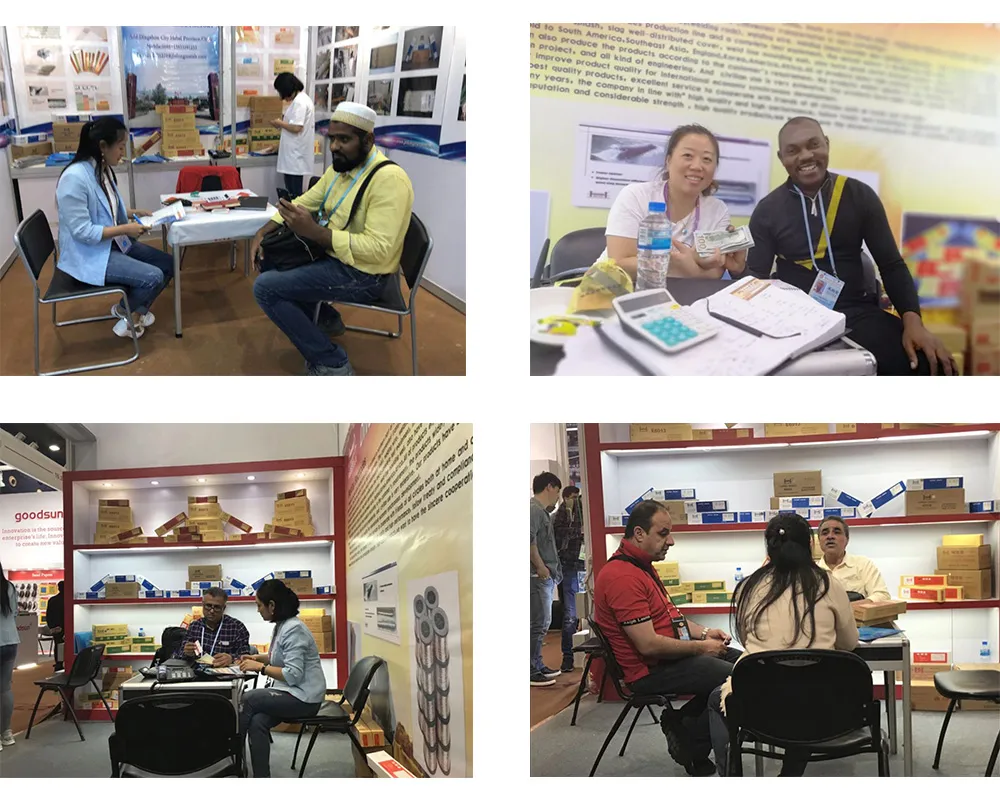
Friction stir welding is an eco-friendly, solid-state joining process that operates by using frictional heat and a non-consumable tool to unite materials without melting them. This method ensures a superior welding bond that overcomes many limitations posed by traditional welding, such as deformation and residual stress in the weld area. As the demand for high-strength, lightweight, yet durable materials grows, industries ranging from aerospace to automotive are increasingly embracing FSW for its numerous advantages.
One of the significant benefits of friction stir welding is its ability to create a weld joint with minimal distortion. By avoiding the molten state, this technique allows the weld area to retain much of its original characteristics, preserving the metallurgical properties of the materials involved. This results in less stress and structural vulnerability, which translates to safer and more reliable products, a crucial consideration in fields where material failure could have catastrophic consequences.
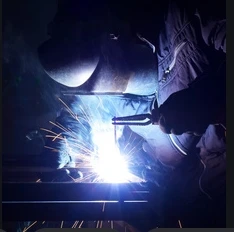
Friction stir welding also impresses with its versatility and adaptability. It can be used to join a variety of materials, from traditional metals like aluminum and copper to more challenging alloys that are often difficult to work with using conventional electrode-based welding. This capability to work with diverse materials opens up immense possibilities for engineers seeking innovative solutions in product design and manufacturing.
The cost-effectiveness and energy efficiency of friction stir welding cannot be overstated. Without the need for consumable electrodes, businesses can reduce material costs and inventory burdens associated with traditional welding supplies. Moreover, the lower energy requirements of FSW contribute not only to a reduced environmental impact but also to significant savings on operational costs over time. This presents an attractive proposition for companies looking to improve their sustainability credentials while also streamlining their production processes.
welding without electrode
From a quality perspective, the consistency of the welds produced by friction stir welding stands out. Automated FSW systems further enhance this consistency, providing uniform weld quality across large production runs. This ensures that each product meets stringent quality standards, crucial for industries where precision is not just preferred but required by regulatory bodies.
Safety concerns are also minimized with friction stir welding. The process eliminates the risk of exposure to harmful fumes, spatter, and ultraviolet light commonly associated with traditional welding, ensuring a safer work environment for operators. This safety factor not only protects workers but also reduces the liability risks for companies.
In a world where technological innovation is key to maintaining a competitive edge, adopting advanced welding techniques like friction stir welding is becoming increasingly important. Those who integrate such cutting-edge technologies into their production lines not only enhance their product offerings but also solidify their position as leaders in their respective industries.
Ultimately, welding without an electrode doesn't just challenge conventional perceptions; it ushers in a new era of possibilities and improvements in manufacturing processes. For companies willing to embrace change, friction stir welding offers an exciting pathway to enhanced performance, environmental responsibility, and overall product quality. This technique epitomizes the kind of forward-thinking approach necessary for success in the modern industrial landscape.