Selecting the right welding stick for stainless steel is pivotal to ensuring the success of any welding project. With a multitude of options available in the market, it’s vital to make a precise choice that aligns with your project needs. Drawing from years of hands-on experience, this guide unveils the technical considerations and expertise required to choose the optimal welding stick for stainless steel, thereby enhancing the quality and durability of the welds.

Understanding the specific properties of stainless steel is the cornerstone of achieving superior welds. Known for its corrosion resistance and strength, stainless steel is a preferred material across numerous industries, from construction to aerospace. However, these same properties can present challenges during the welding process. Selecting a welding stick that complements stainless steel’s distinctive characteristics is crucial to maintaining its integrity.
Renowned experts agree that choosing the appropriate welding stick necessitates a thorough understanding of the alloy type of the stainless steel you are working with. Common types such as 304, 316, or 409 each have unique attributes. For instance,
a 308L welding stick is typically recommended for joining 304 and 304L stainless steel. This stick is favored for its ability to produce a stable arc and smooth bead, minimizing the risk of porosity and ensuring superior fusion.
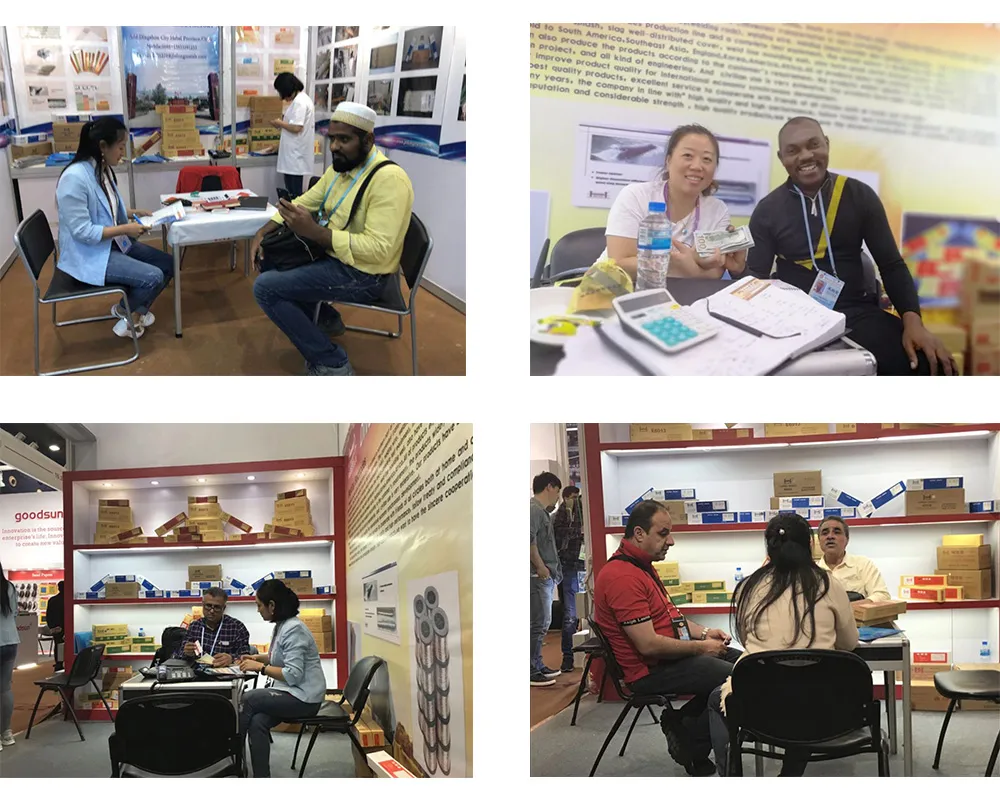
Professional welders emphasize the importance of considering the joint design and position when selecting welding sticks. For overhead or vertical welding positions, a stick with a fast-freezing slag is advantageous, aiding in preventing the molten weld pool from spilling and ensuring precision. Moreover, the penetration depth offered by the stick is another critical factor; deeper penetration is often required for thicker materials to ensure a robust bond.
welding stick stainless steel
Equally significant is the expertise required in post-welding procedures. Professional reviews highlight the importance of proper passivation after welding stainless steel. Passivation is a chemical treatment that removes free iron from the surface and enhances the naturally occurring corrosion-resistant oxide layer. Neglecting this can result in premature corrosion, negating the benefits of choosing quality materials and sticks.
Staying updated with the latest advancements in welding technology can enhance both efficiency and quality in stainless steel projects. Many modern welding sticks are designed with innovative coatings that facilitate smoother operations and are more forgiving with respect to setting deviations. Experienced welders are increasingly seeking sticks that promise reduced spatter and minimal slag, which in turn, minimizes cleaning time and maximizes productivity.
Sharing insights from leading industry professionals adds credibility and authority. It is widely endorsed that investing in high-quality consumables from trusted brands yields dividends in the long run. Reliable performance and consistent results justify the initial cost, reducing the chances of joint failures and costly reworks, thus establishing trustworthiness in the choice of products.
In conclusion, selecting the right welding stick for stainless steel involves a delicate balance of expertise, understanding material properties, and leveraging modern technological advancements. Prioritizing these considerations will not only ensure the structural integrity and aesthetic appeal of your welds but also affirm the credibility and authority of your work, resonating with clients and peers alike in the welding domain.