Selecting the right welding rod for A36 steel is crucial in ensuring a quality and durable bond. A36 steel, prized for its excellent welding properties, is a staple in the construction of buildings, bridges, and general structural applications. For those seeking an authoritative guide based on real-world expertise and experience, a few considerations stand paramount in making an informed choice.
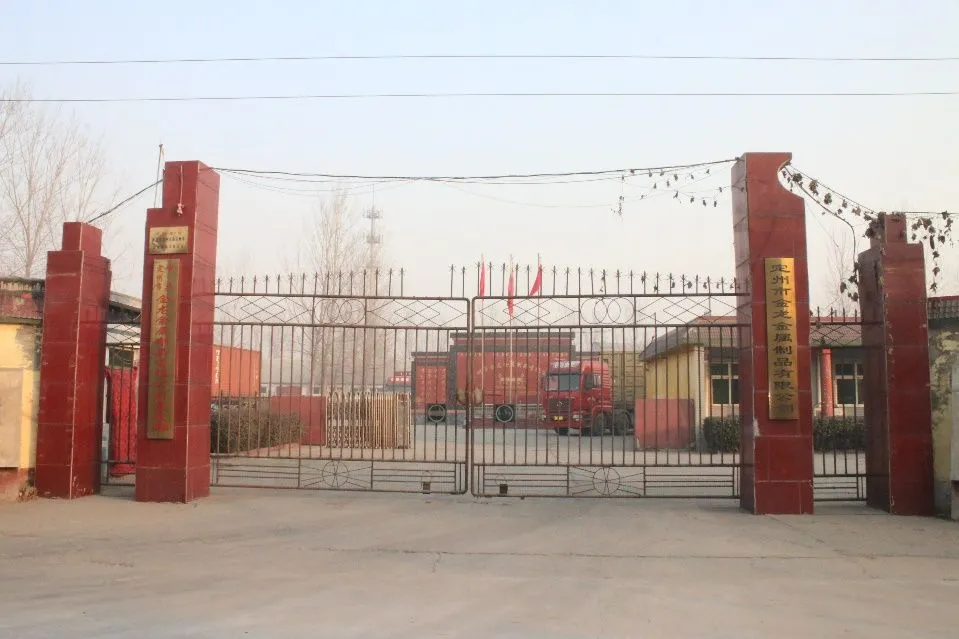
As a low-carbon steel offering good strength and formability, A36 is highly weldable with a variety of electrodes. However, one must understand the specific demands of the project to select the most appropriate welding rod. For common applications, the E6013 welding rod stands out. Known for its versatility and ease of use, E6013 rods produce a soft arc with excellent wetting action, perfect for clean, flat welds on A36 steel.
For projects requiring deeper penetration and higher strength, E7018 electrodes may be recommended. These low-hydrogen rods offer greater tensile strength, which is vital for load-bearing structures. They also provide increased resistance to moisture and cracking, a significant advantage in outdoor or high-stress environments.
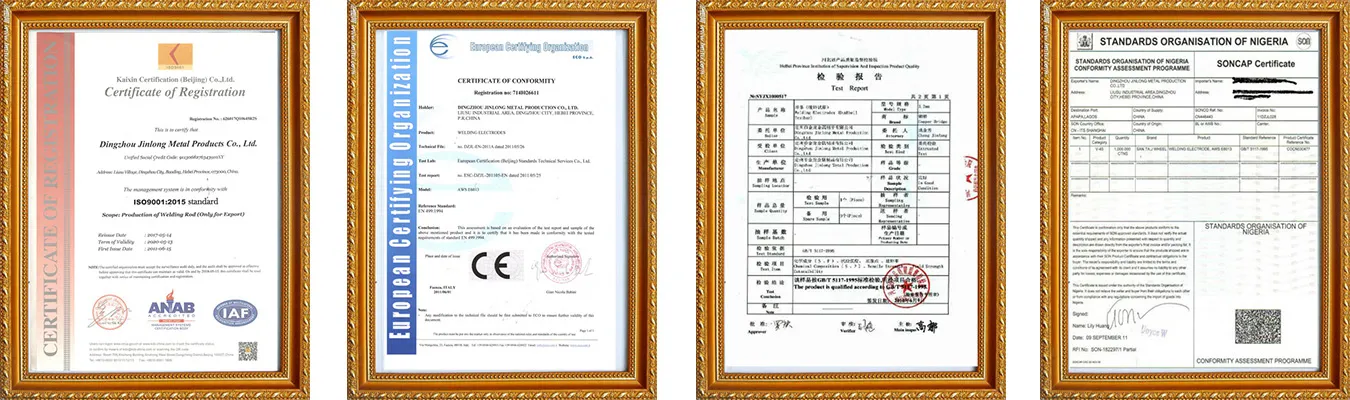
Experience teaches that the thickness of the A36 steel piece greatly influences electrode selection. For thinner plates, around ¼ inch or less, an E6013 will suffice, thanks to its consistent performance in various positions and ease of control. Conversely, for thicker sections exceeding ¼ inch, E7018’s superior penetration and mechanical properties become invaluable.
Beyond rod selection, welding technique also plays a pivotal role. Mastery of the appropriate technique, such as stringer beads or weaving, can amplify the material’s inherent strengths and compensate for its weaknesses. This expertise ensures that the joint integrity remains unassailable under stress and over time.
welding rod for a36 steel
Ensuring the cleanliness of the A36 steel surface before welding also cannot be understated. Removing impurities such as rust, grease, and paint is essential to avoid contamination of the weld pool, which can lead to defects or structural weaknesses. A simple wire brushing or sanding ought to suffice for most impurities.
An often overlooked yet critical aspect of the welding process on A36 steel is pre-weld setup and post-weld treatment. Preheating the steel, especially in cold environments or with thicker sections, helps in minimizing residual stress and potential cracking. Following the weld, allowing adequate cool-down periods and post-weld heat treatments are equally crucial, as rapid cooling can affect the weld’s structural integrity.
Moreover, it is fundamental to comply with relevant industry standards such as the AWS (American Welding Society) specifications, which ensure that both procedures and materials align with established guidelines, fostering trust and quality assurance.
Trustworthiness in welding goes beyond just the selection of the correct rod; it encompasses the welder's skill, adherence to safety protocols, and understanding of A36’s unique characteristics. Whether for a seasoned professional or a novice hobbyist, acknowledging these considerations can make a tangible difference in the outcome of their projects.
Ultimately, while A36 steel’s forgiving nature welcomes various welding approaches, leveraging a balanced blend of practical experience, technical knowledge, and authoritative industry standards ensures that the final product is not only functional but reliably robust. Making informed decisions about welding rods and techniques not only enhances product performance but also contributes to long-term success and safety in all steel-structured endeavors.