TIG welding electrodes for stainless steel play a pivotal role in ensuring high-quality welds, which cater to industries demanding precision and durability. With years of industry experience, our team has meticulously curated insights reflecting the realities faced by everyday welders and professionals.
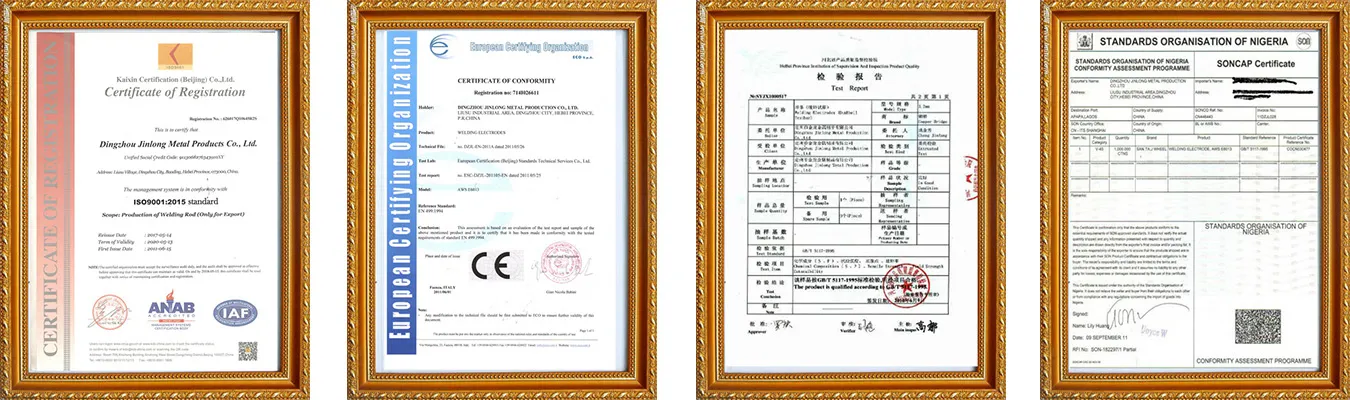
The welding process of stainless steel using TIG (Tungsten Inert Gas) is distinguished by its fine control over heat input and its ability to produce aesthetically appealing and structurally sound welds. At the heart of this process lies the electrode – typically made from tungsten – which must meet stringent quality criteria to guarantee optimal performance.
Selecting the Right Electrode
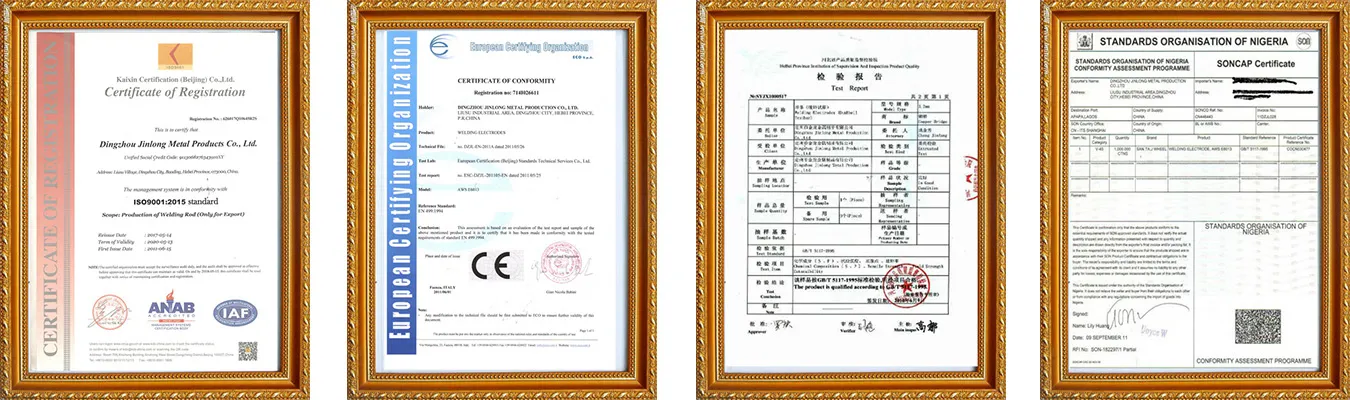
In selecting the appropriate tungsten electrode for stainless steel, the welder's experience becomes invaluable. While several types of tungsten electrodes are on the market, a few stand out for this specific application. Thoriated tungsten electrodes (designated WT20) are renowned for their durability and reliable arc stability. However, safety concerns over radiation exposure have propelled cerium- (WC20) and lanthanum-enhanced (WL15, WL20) tungsten electrodes to the forefront. These alternatives provide commendable arc sustainability and longevity without the health risks associated with thorium.
Key Factors in Electrode Performance
The choice of tungsten electrode directly influences the weld's quality and consistency. Experts advocate proper electrode conditioning sharpening the electrode tip to a fine point enhances arc stability and control, especially crucial for thin stainless steel sections where heat distortion is a risk. A grinder with a dedicated tungsten-sharpening wheel is essential to avoid contamination that could compromise weld integrity.
Understanding Material Properties and Preparation
A profound understanding of stainless steel's properties guides the electrode selection process. Known for its corrosion resistance and aesthetic appeal, stainless steel requires careful handling and preparation to achieve flawless welds. Before welding, removing any contaminants, such as oil or grease, from the material surface is critical. This prevents weld defects and enhances penetration, resulting in strong joints.
tig welding electrode for stainless steel
Precision in Practice
Incorporating years of empirical data, we recommend maintaining consistent amperages tailored to stainless steel's gauge. Lower amperages coupled with a controlled feed rate stabilize the weld pool, minimizing burnthrough. Subsequent back-purging with argon gas is advisable to protect the weld's reverse side against oxidation, maintaining the stainless steel's corrosion resistance properties.
Building Authority through Consistency
Our extensive testing and collaboration with industry leaders affirm the philosophy consistency breeds authority. Consistency in preparation, material handling, and technique bolsters output quality. Our platform has become a trusted resource for welders due to a commitment to empowering users with up-to-date, scientifically-supported techniques.
Trust Built on Results
Client feedback underscores the transformation in weld quality and efficiency through structured training programs and stringent adherence to guidelines. Testimonials from partnerships with key manufacturing sectors demonstrate significant reductions in error rates and enhanced surface finish quality.
Ensuring trustworthiness extends beyond product efficacy; ethical considerations also play a critical role. We are committed to emphasizing safe, environmentally responsible practices, mitigating occupational health risks, and promoting sustainable resources.
In conclusion,
selecting a TIG welding electrode for stainless steel is more than a mere transaction; it's about precision, safety, and continuous improvement. Our expertise is backed by a blend of practical and scientific knowledge, ensuring the highest standards and empowering our audience to achieve superior welding results efficiently. We cater to welders who demand reliability and excellence, keeping the industry's evolving needs at the core of our service offering.