The world of welding often immerses itself deeply into the minutiae of materials, techniques, and tools, particularly when it comes to stainless steel. One element that frequently garners attention is the selection and application of stainless steel electrodes. Understanding the significance of electrode numbers in stainless steel welding is crucial for ensuring structural integrity and performance.
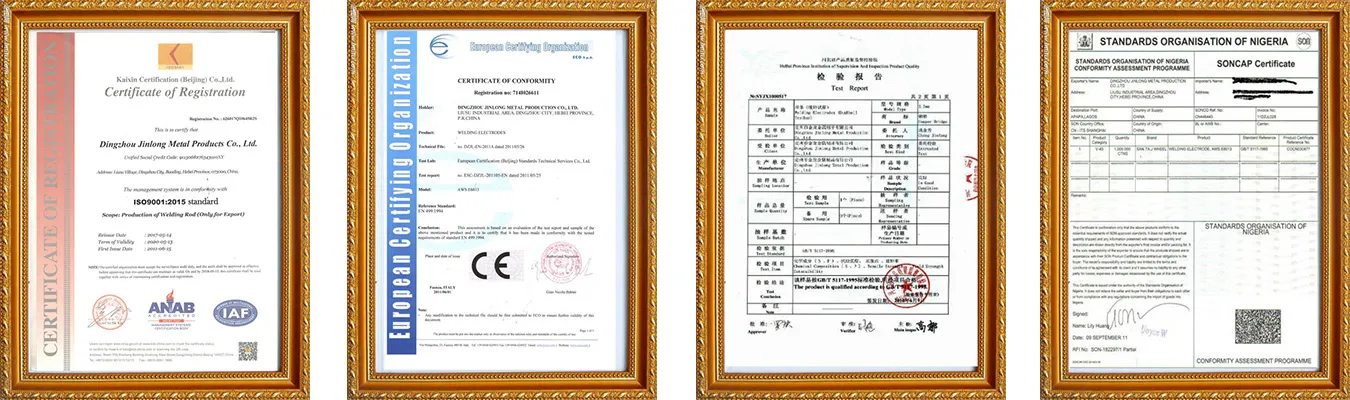
Stainless steel electrodes are vital in welding operations, serving as the intermediary that melts and fuses metals together. Each electrode is designated with a specific number that highlights its composition and intended use — a critical factor when choosing the right one for a particular application. Let's unravel the complexities of stainless steel electrode numbers and explore their impact on product quality, durability, and reliability.
The designation of stainless steel electrodes typically begins with the letter “E,” followed by a series of numbers. The “E” symbolizes “electrode,” and the numbers that trail it offer insight into the core characteristics of the electrode itself. For instance, an E308 electrode is quite common in stainless steel applications. Here's how to decode what these numbers signify
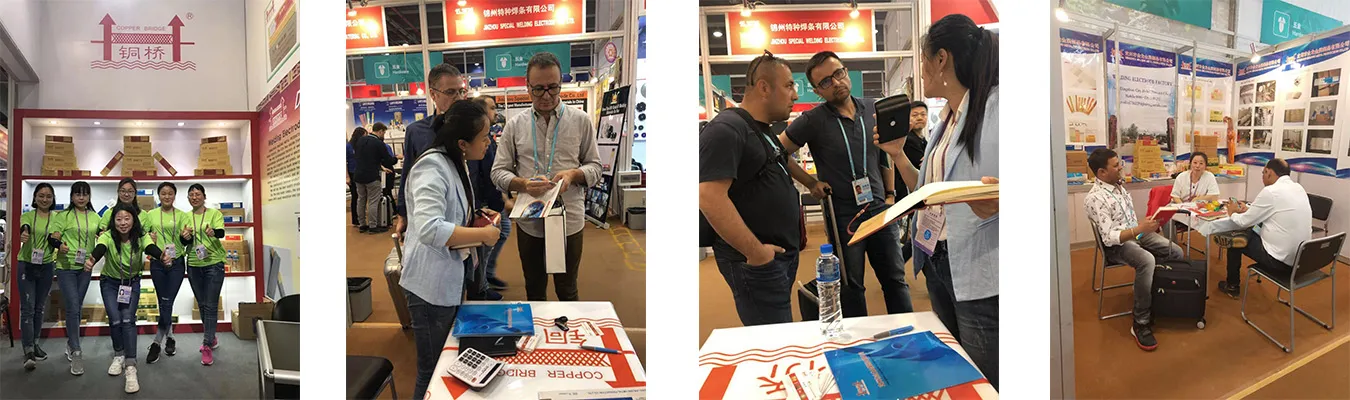
1. The 'E' Prefix As mentioned, the “E” stands for electrode, a standard industry notation that immediately identifies the item as a welding electrode.
2. Numbers Following 'E' The first two or three numbers directly after the “E” often refer to the basic type of stainless steel and, by extension, indicate the chemical composition of the welding rod. The E308, E309, and E316 are among the most prevalent due to their adaptability in various environments.
3. Chemical Composition These numbers align with the American Welding Society (AWS) designations and disclose the appropriate match for base metals — critical since compatibility can determine the success of a weld. For example, E308L, where ‘L’ indicates low carbon content, is more suitable for applications where corrosion resistance is paramount.
4. Mechanical Properties The tensile strength and ductility of the weld are greatly influenced by the electrode selection. The numeric classification ensures that the electrode chosen can withstand the mechanical demands of the specific operation.
stainless steel electrode number
5. Welding Position and Polarity Some specifications also encompass ideal welding positions and current polarity, ensuring that users operate within settings that guarantee optimal performance.
Selecting the right stainless steel electrode is paramount for many industries, including construction, automotive, and aerospace. Each sector has unique demands; therefore, understanding the nuances of electrode numbers is a mark of expertise.
Experienced welders often share insights into how matching electrode numbers with the correct base metal not only elevates the quality of the weld but also prolongs its life, maintaining the structural integrity of the assembly. This principle is not only rooted in theoretical knowledge but is supported by real-world experience within various industry applications.
One veteran welder, for instance, recounts a project where failure to match the electrode correctly resulted in corrosion within weeks. Upon replacing the poorly matched electrodes with suitable E308L electrodes, the problem was effortlessly resolved, underscoring the importance of understanding electrode nomenclature.
Authority in selecting the right electrode extends to manufacturers and suppliers who prioritize education alongside sales, offering guidance on electrode codes to ensure customers make informed choices. This dissemination of expertise builds trust with consumers and solidifies reputations within competitive markets.
In conclusion,
the numbering on stainless steel electrodes is not merely an arbitrary designation. It encapsulates crucial information that defines the properties and functionality of the electrode. Professionals who decipher these codes with precision and apply them expertly to their applications benefit from improved weld quality, enhanced durability, and greater resistance to wear and environmental elements.
For anyone involved in stainless steel welding, investing the time to master electrode nomenclature is an invaluable pursuit, fostering both skill enhancement and product excellence. Whether innovating new welding techniques or perfecting traditional methods, the expertise surrounding electrode selection undeniably supports each endeavor's success.