Choosing the right filler rod for cast iron is crucial for ensuring a strong, durable weld that will stand the test of time. In the realm of metalworking, cast iron presents unique challenges due to its composition and properties. As an experienced industry professional, I will guide you through the nuances of selecting the perfect filler rod, drawing insights from real-world experiences and industry expertise.
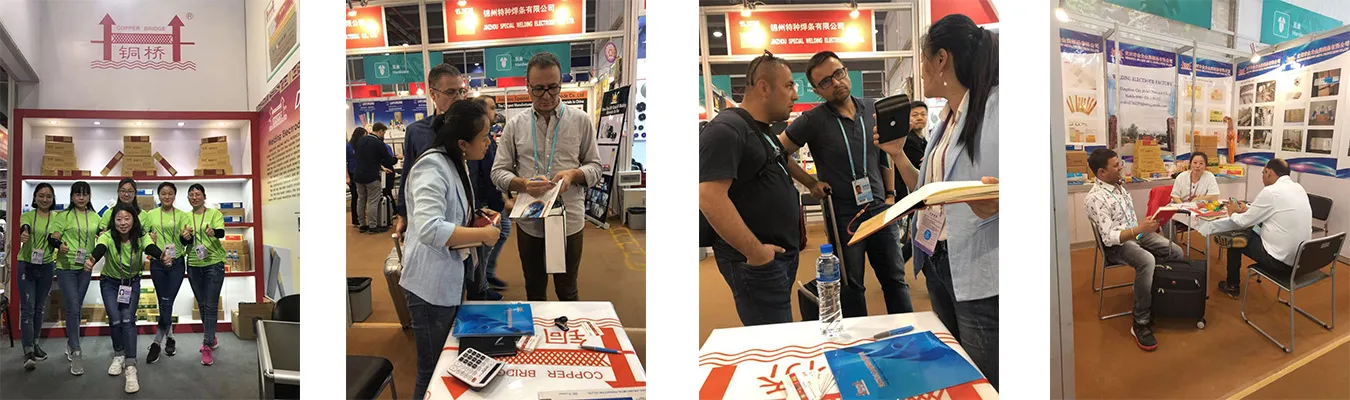
Cast iron is an alloy predominantly composed of iron, carbon, and silicon, which lends it durability and wear resistance. However, its high carbon content also makes it prone to cracking during and after welding. To address this, the choice of filler rod becomes pivotal.
Nickel-based filler rods are often preferred due to their compatibility with cast iron. Nickel rods offer excellent elasticity and a lower coefficient of thermal expansion, which alleviates stress during cooling and minimizes the risk of cracking.
One popular choice is the ENiFe-CI rod, which contains both nickel and iron. This composition closely matches the properties of cast iron, providing a strong bond that can accommodate the material's thermal contraction. In contrast, ENi-CI rods are composed almost entirely of nickel, making them ideal for applications where maximum strength and ductility are paramount. These rods are particularly beneficial when working with nodular cast iron or when machining the weld is a priority due to their softer, more machinable nature.
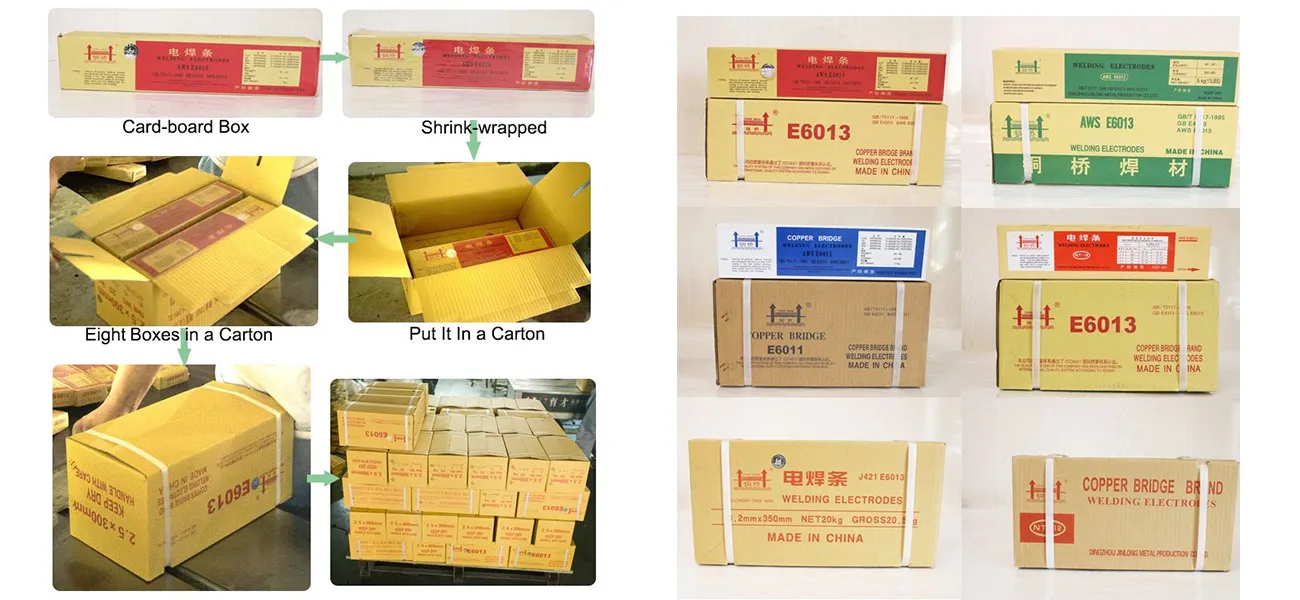
Choosing the right filler rod is not only about material compatibility but also about understanding the type of cast iron involved. Gray cast iron, the most common type, usually works well with the aforementioned nickel-based rods. However, when dealing with white cast iron, which is notoriously difficult to weld, preheating and slow cooling are essential to prevent cracking, alongside a carefully chosen filler rod.
Practical experience in the field reveals that while nickel rods are forgiving, they're not foolproof. Welders must pay attention to joint design and preparation for successful outcomes. Cleaning the weld area to remove contaminants and employing a suitable welding technique such as Tungsten Inert Gas (TIG) or Shielded Metal Arc Welding (SMAW) further enhances the weld quality.
filler rod for cast iron
From a professional standpoint, it's essential to consider the operational environment of the welded piece. For components exposed to high temperatures, an austenitic stainless steel rod like the E312-16 can sometimes be more appropriate than a pure nickel rod. These rods offer excellent thermal and corrosion resistance, expanding the range of applications for welded cast iron components.
The authority of any product recommendation lies in verifiable results and industry consensus. Both nickel and stainless steel rods are endorsed by standards organizations like the American Welding Society (AWS), providing a benchmark for quality and performance. Certifications ensure that these rods meet rigorous criteria, offering welders peace of mind and reliability in their work.
Trust in the performance of a filler rod is substantiated by both lab tests and fieldwork. Consistent results under varied operating conditions confirm the efficacy of these rods, affirming their status as the industry standard. A commitment to sourcing filler rods from reputable manufacturers further bolsters trust, ensuring each product batch meets the expected standards of excellence.
In conclusion, selecting the right filler rod for cast iron welding demands a balance of technical knowledge, practical expertise, and trust in product quality. By prioritizing these factors, welders can achieve durable, robust welds that fulfill their project's demands. Whether choosing between nickel-based or stainless steel rods, the key lies in understanding the nuances of the materials and the specific requirements of the job, leading to outcomes that not only excel in performance but also stand resilient against the challenges posed by cast iron.