Electrode of welding stands as a core component in the welding industry, pivotal in determining weld quality, performance, and efficiency. Selecting the right welding electrode is crucial for any project, whether it's a minor repair or a significant industrial fabrication. Understanding the intricacies of electrodes can save time, resources, and ensure the safety and durability of the final structure.
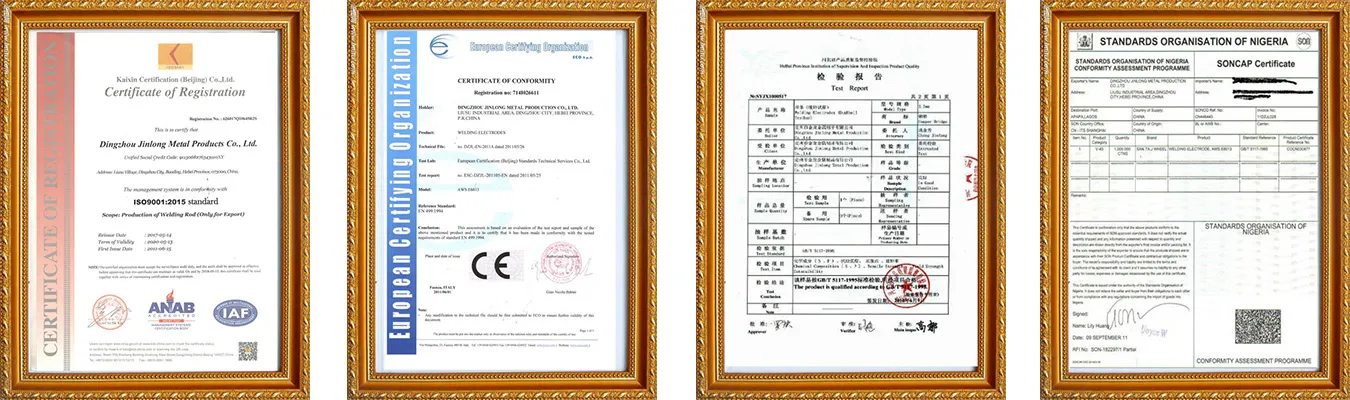
A deep dive into electrodes reveals their fundamental role in welding. Essentially, electrodes act as a conductor of electric current, used to create an electric arc between the electrode and the metals to be joined. This electric arc generates the heat necessary to melt the base materials, facilitating the fusion process. Electrodes come in various types and sizes, each designed for specific applications, materials, and welding conditions.
The classification of welding electrodes generally follows the American Welding Society (AWS) specification standards. Each type has a distinct designation that highlights its features. For example, in the designation E6010, 'E' stands for electrode, '60' indicates a tensile strength of 60,000 psi, '1' suggests the welding position best suited for the electrode, and '0' represents the type of coating and current.
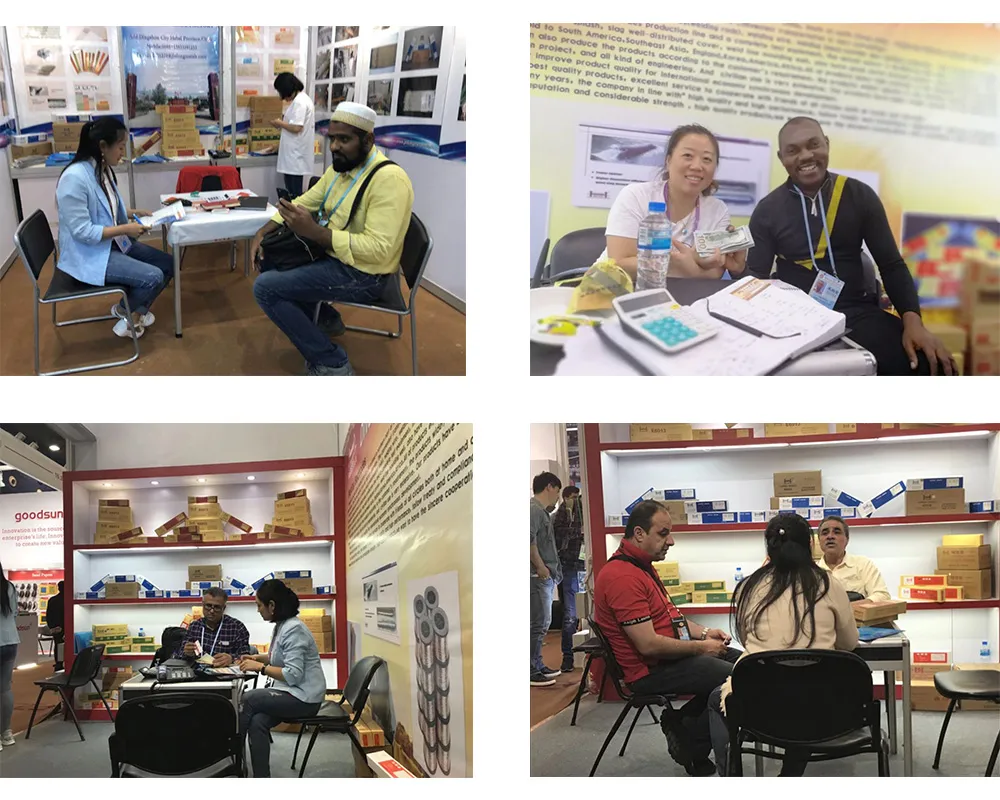
Experience plays a significant role in electrode selection. Welders must assess the material to be welded, the expected environmental conditions, and the mechanical properties desired in the final product. For instance, while working with ferrous metals like carbon steel, E6010 might be preferred for its excellent penetration and arc stability, essential for pipe welding in particular. On the other hand, E7018 is often chosen for its low hydrogen content, minimizing the risk of cracking in thicker materials.
Expertise in using welding electrodes entails understanding the subtle differences between their compositions and coatings. Electrodes can be made of different metal compositions and have various coatings like cellulose, rutile, or basic, each affecting the welding process's current and speed. Rutile-coated electrodes, for instance, offer a smooth arc and better bead appearance, while basic-coated electrodes provide stronger welds with less spatter.
electrode of welding
In terms of authoritativeness, securing certifications from reputable welding authorities can enhance a company's credibility. The AWS and the International Organization for Standardization (ISO) often conduct rigorous tests to validate electrode performance. Adhering to these standards ensures that the electrodes meet safety and quality requirements, thereby boosting the reliability of the final structures.
Trustworthiness in the manufacturing process is equally important. The source of the electrode and the reputation of the manufacturer can significantly impact the performance outcomes. Quality control measures, consistent testing, and transparency about the electrode compositions further contribute to the trustworthiness of the product. Therefore, selecting electrodes from well-established manufacturers with proven track records can ensure consistent performance.
Keeping pace with technological advancements in electrode manufacturing can also provide competitive advantages. Innovations such as flux-cored wires and advancements in electrode coatings are constantly reshaping welding practices, offering improved efficiency and precision. Staying updated with these developments allows businesses to adopt better techniques, reducing project timelines and costs without compromising on quality.
In conclusion, welding electrodes are more than mere accessories; they are the lifeline of effective welding practices. Prioritizing experience, expertise, authoritative validation, and trustworthiness in electrode selection not only bolsters operational efficiency but also ensures the longevity and safety of the welds produced. As the industry evolves, refining these aspects will remain key to mastering the art and science of welding.