Carbon steel welding electrodes are essential tools for both amateur and professional welders, offering unmatched versatility and performance in a variety of welding applications. Known for their ability to join metal with ease, these electrodes are particularly favored for their robustness and adaptability. With the correct choice and application of carbon steel electrodes, industry professionals can achieve excellent welding results, ensuring structural integrity and safety.
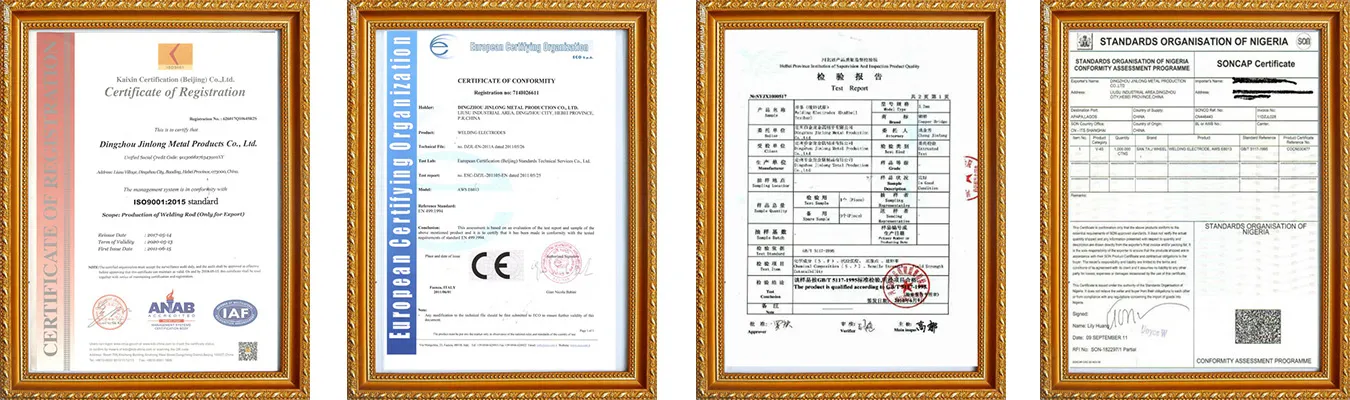
Understanding the Types of Carbon Steel Welding Electrodes
Carbon steel welding electrodes come in various types, each with specific characteristics suited to different welding tasks.
Two popular options are E6010 and E7018 electrodes. The E6010 is known for its deep penetration ability, making it ideal for welding through rust, oil, or dirt. Its cellulose sodium coating provides strong arc force and penetration, crucial for tasks like pipeline welding. On the other hand, the E7018 electrode is low hydrogen, often used in structural welding applications, offering smooth, stable arcs and minimizing the risk of cracking.
Choosing the Right Electrode
Selecting the right carbon steel electrode depends on the welding position, base material, and environmental conditions. For vertical or overhead positions, E6010 is a preferred choice due to its fast-freezing characteristics. However, when working on clean, flat, or horizontal surfaces where a smooth finish is essential, E7018 electrodes are recommended for their low-hydrogen performance and ability to produce a more aesthetically pleasing weld bead.
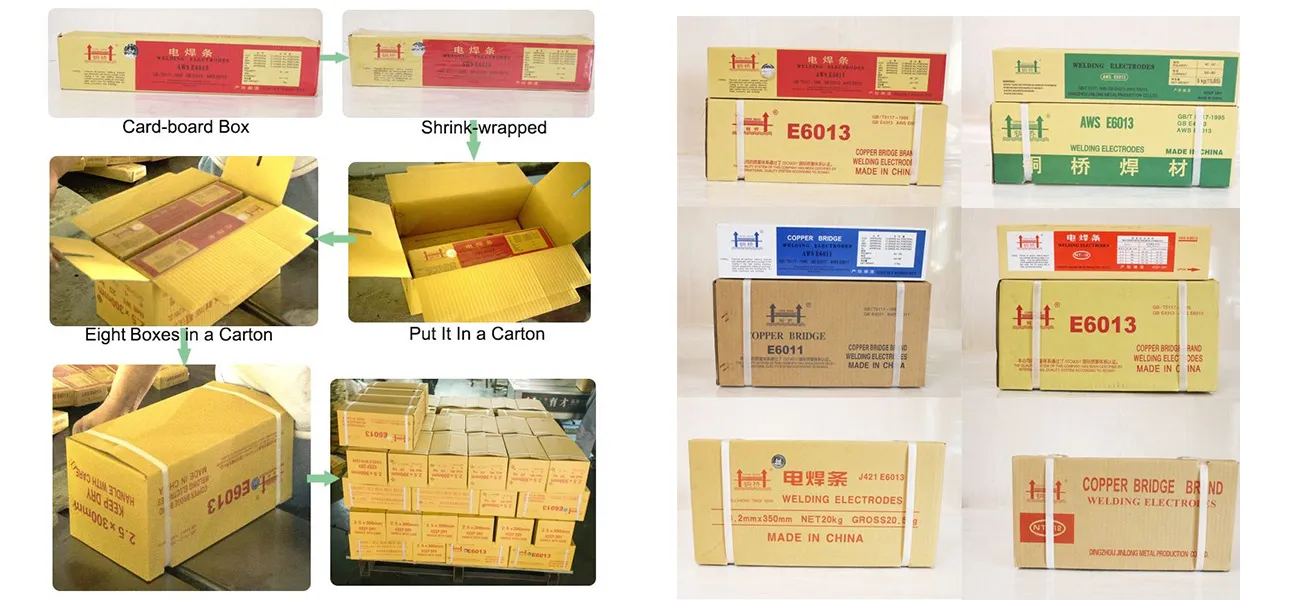
Preparation and Handling
Proper handling and storage of carbon steel electrodes are crucial to maintaining their effectiveness. Moisture can compromise an electrode's performance, leading to defects such as porosity in the weld. Therefore, storing electrodes in a dry, enclosed space is necessary to prevent moisture absorption. For low-hydrogen electrodes like E7018, additional precautions, such as using an electrode oven, can further ensure optimal moisture protection.
carbon steel welding electrode
Welding Techniques and Best Practices
Welding with carbon steel electrodes requires specific techniques to ensure quality and integrity. An understanding of appropriate amperage settings, angle control, and travel speed is essential. For example, maintaining the recommended amperage setting, usually specified by the electrode manufacturer, helps in achieving optimal arc length. Consistent control of the angle and travel speed can prevent common issues like slag inclusion or uneven bead formation.
Safety and Compliance
Safety is paramount in welding operations. Using the correct personal protective equipment, such as welding helmets, gloves, and protective clothing, is essential to protect against the hazards of welding, including UV light and hot metal. Furthermore, adhering to industry standards and regulations ensures that welding practices meet necessary safety and quality benchmarks.
The Impact of Technological Innovations
Advancements in welding technology have introduced improved carbon steel electrodes with enhanced performance features. Innovations focus on reducing welding defects and increasing efficiency, such as the development of advanced coatings that enhance arc stability and reduce spatter. Staying informed about these technological changes allows welders to choose the best products that offer superior quality and reliability.
In conclusion, the selection and use of carbon steel welding electrodes play a crucial role in the success of a welding project. By understanding the characteristics of different electrodes, employing proper handling techniques, and embracing technological innovations, welders can achieve high-quality, durable welds that meet both professional and safety standards.