Basic welding rods are foundational elements in the world of welding, and understanding their characteristics is crucial for achieving strong and durable welds. The true test of any welding process lies not only in the expertise of the welder but also significantly in the quality and suitability of the welding rod selected for the task.
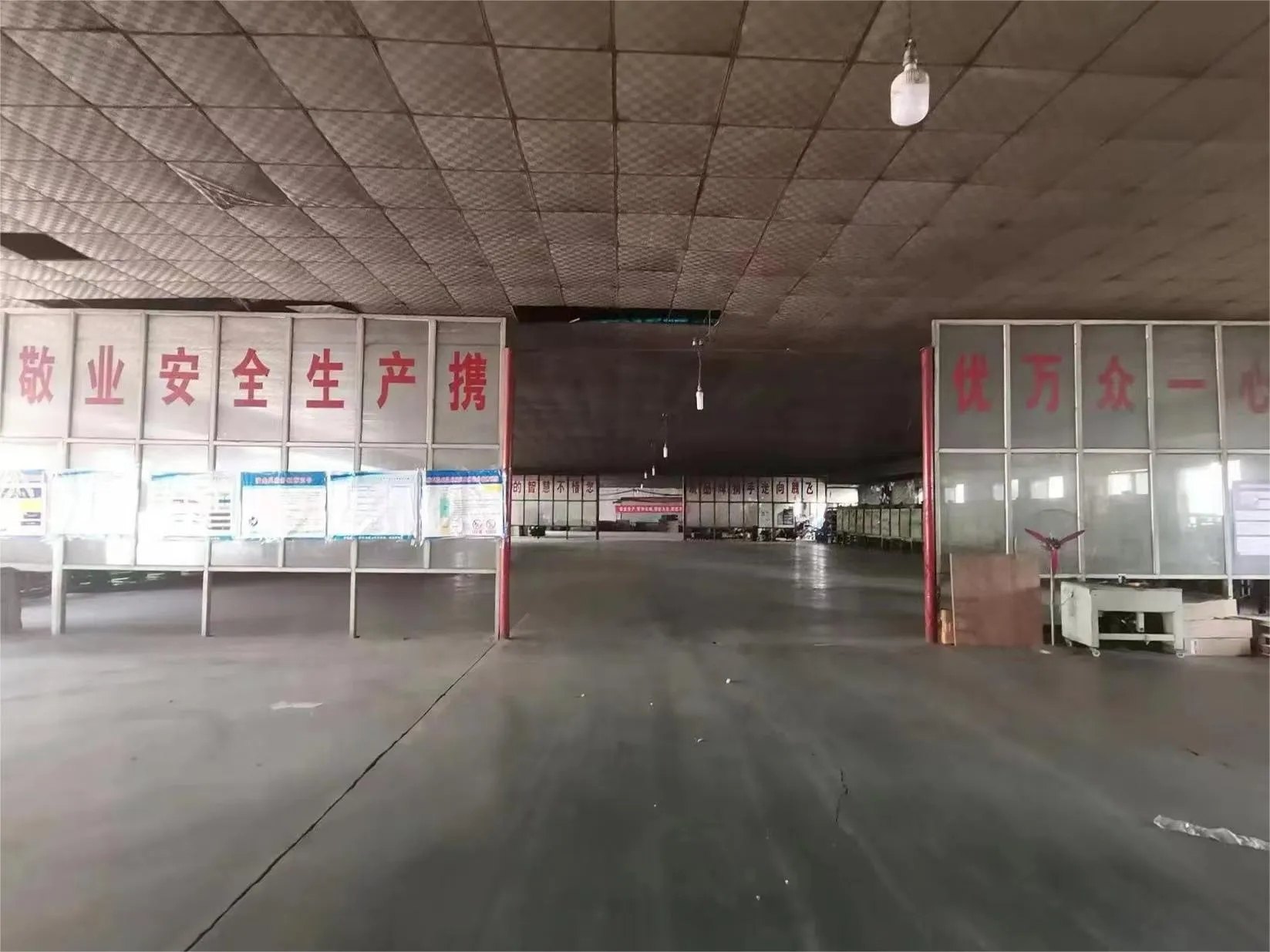
Welding rods, often referred to as electrodes, are integral to the welding process as they form the filler material used to join metals. When heat is applied, these rods melt and create a bond between the metal pieces. This process is essential in numerous industries, from construction to automotive repair, making the choice of the right rod essential for any successful welding operation.
Experience plays a pivotal role in choosing the right welding rod. Seasoned welders understand the intricacies of different materials and their behavior under heat. They appreciate that different rods are suited for particular types of metals and welding processes. For instance, mild steel welding often uses electrodes like E6010 or E6011, which are known for their deep penetration capabilities, making them excellent for welding dirty or rusty steel. Meanwhile, E7018 rods provide a smooth finish and are favored for their tensile strength and suitability in welding newer steel with minimal spatter.
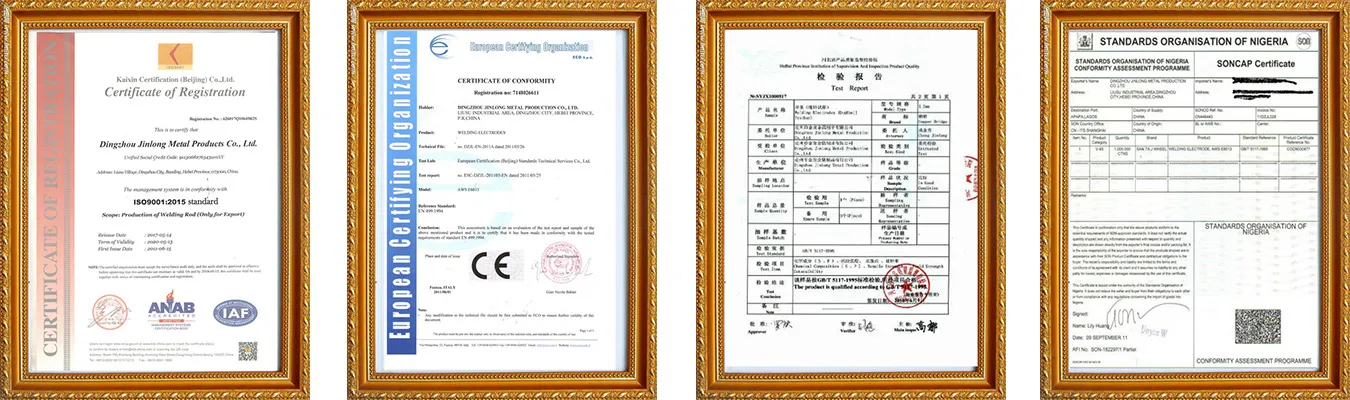
Expertise in welding not only derives from hands-on experience but also from a deep understanding of welding rod classification systems. These classifications, usually designated by a combination of letters and numbers like E6011 or E7018, provide vital information about the rod’s tensile strength, position usability, coating type, and current compatibility. A rod categorized as E6011, for example, indicates a tensile strength of 60,000 PSI, suitable for all positions, with a cellulosic coating ideal for alternating and direct currents.
basic welding rods
Authoritativeness in the realm of welding rods is backed by adherence to industry standards and certifications. Professional welders rely on rods that meet stringent standards such as those set by the American Welding Society (AWS). This not only ensures quality and reliability but also compliance with safety and performance regulations. Reputable manufacturers often provide rods that are rigorously tested and certified, offering assurance of their performance under specified conditions.
Trustworthiness in the selection of welding rods can also significantly affect the outcome of a welding job. It involves sourcing rods from credible manufacturers known for their consistency in quality. Unscrupulous sources may offer cheaper rods, but these often lead to inferior welds that may cause structural failures over time. Investing in high-quality rods from trusted brands ensures fewer defects, reduced rework, and overall cost savings in the long run.
In conclusion, the choice of basic welding rods should be informed by a combination of experience, expertise, authority, and trustworthiness. Whether for a large industrial application or a simple DIY project, understanding the nuances of welding rod selection is imperative to achieving a high-quality finish. Professionals in the industry must continually update their knowledge and skills, ensuring that they choose the most suitable and reliable welding rods for their needs, leading to safe, effective, and successful welding operations.