Understanding the cost of welding electrodes per kilogram is a fundamental aspect for businesses and professionals in the welding industry. Welding electrodes are essential consumables, and their pricing can significantly impact both the budget and the quality of the welding projects. The price is not just a number—it reflects various factors like quality, material composition, intended use, and market dynamics.
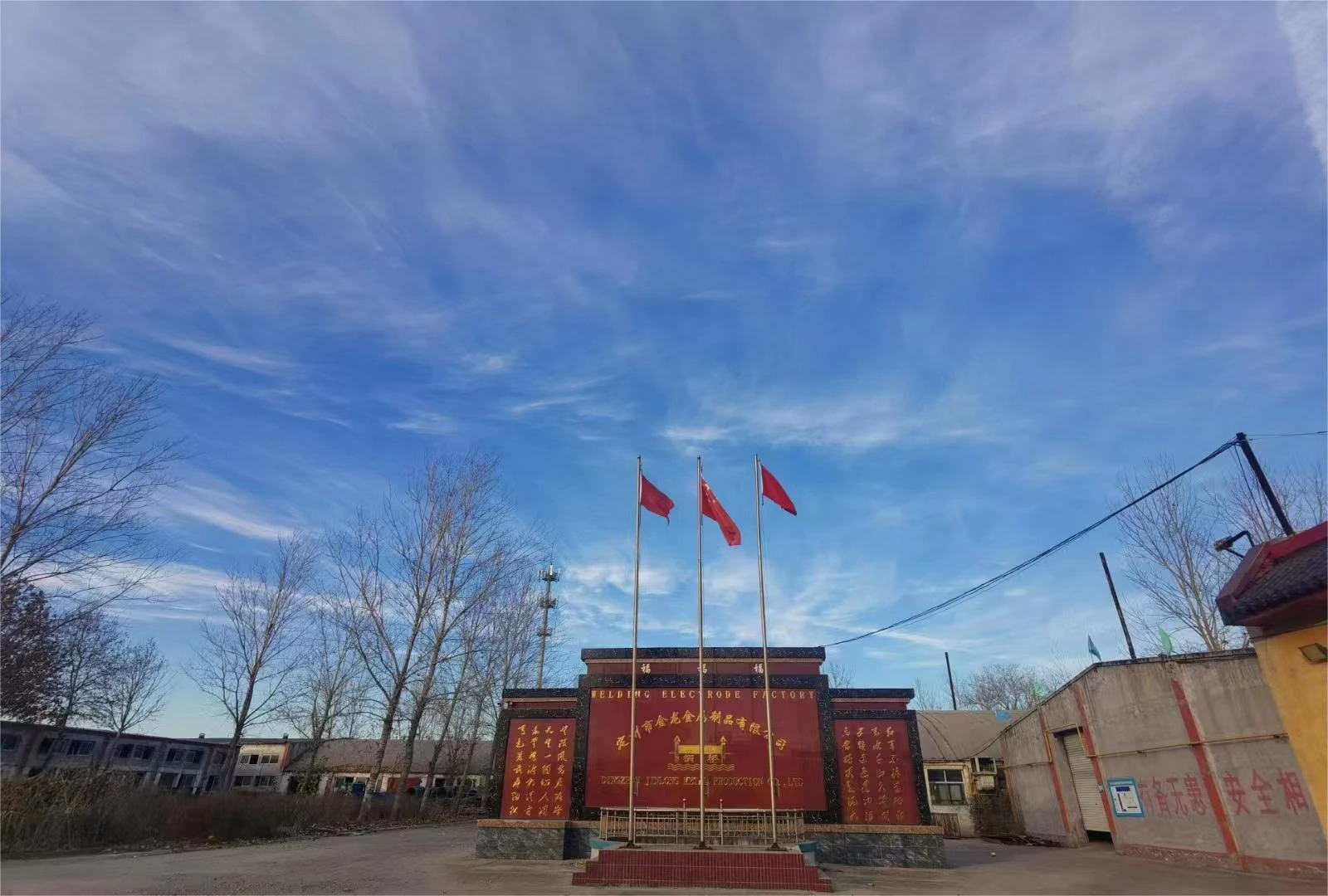
Firstly,
evaluating the quality of welding electrodes is crucial. High-quality electrodes often come with higher costs, yet they provide better performance, durability, and cleaner welds. Investing in superior electrodes leads to fewer defects, less rework, and enhanced productivity, ultimately bringing down the long-term operational cost. It is essential to check for certification and compliance with industry standards when assessing the cost, as these ensure the reliability and safety of the electrodes.
Secondly, the material composition of welding electrodes plays a significant role in their pricing. Electrodes made from premium materials like stainless steel or those designed for specific purposes, such as low-hydrogen electrodes, tend to be more expensive than general mild steel electrodes. These specialized electrodes are engineered to tackle specific challenges—such as high strength, corrosion resistance, or working in extreme conditions—which ordinary electrodes may not manage effectively. Knowing the specific project requirement will help you choose the right electrode while justifying its cost per kilogram.
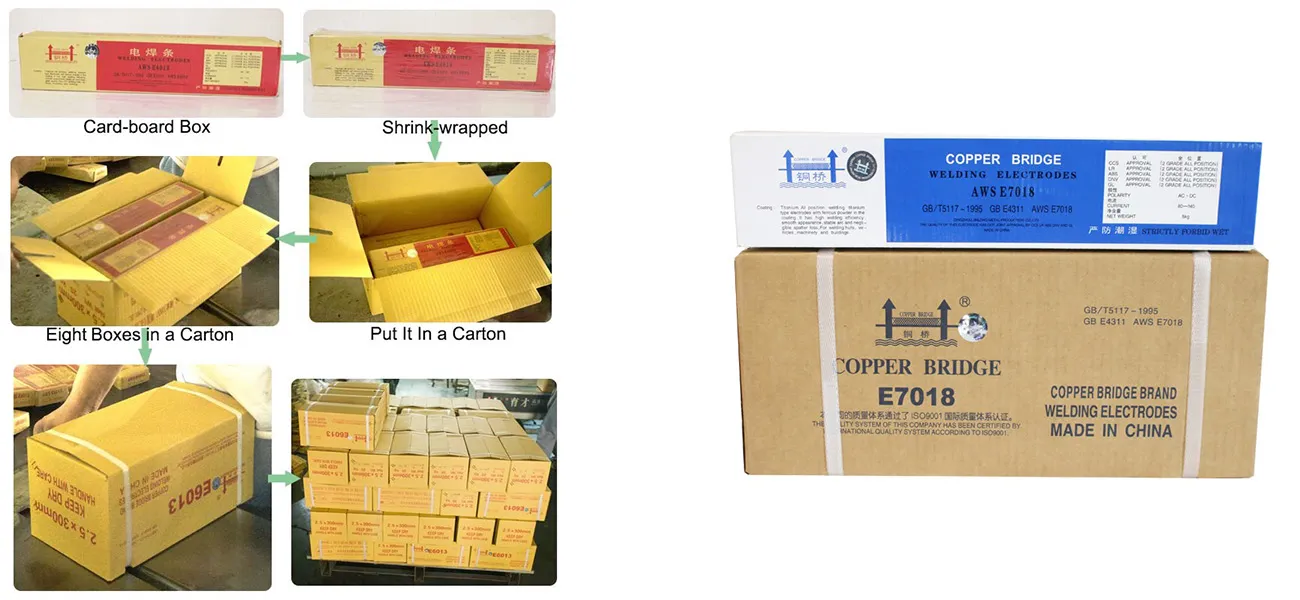
Moreover, intended usage is a vital determinant in electrode pricing. For instance, industrial applications that require robust mechanical properties and resistance to various environments will benefit from higher-priced electrodes. Conversely, routine welding tasks with lesser demands on mechanical properties may suffice with cost-effective options. Aligning the electrode choice with the project’s scope and requirements is key to optimizing cost without compromising on quality.
welding electrode cost per kg
Fluctuating raw material prices, transportation costs, and economic factors like tariffs and taxes also influence electrode prices. Market dynamics can lead to volatility in electrode costs, thus it is advisable to maintain strong relationships with suppliers and stay informed about the market trends. Anticipating these changes can help in strategic purchasing and bulk-buying decisions, ensuring you get the most value for your investment.
A recurring observation from seasoned welders is that cheaper electrodes, while appealing upfront, can lead to inconsistencies or failures that might result in additional costs. Trustworthy manufacturers and suppliers tend to offer better warranties and service support, which translates to greater assurance on the electrode investment. Betting on reputed brands often ensures fewer quality issues, reflecting the principle that trustworthiness and reliability in welding materials often accompany a reasonable cost.
Lastly, building expertise in electrode types and applications can help in making informed cost-effective decisions. Professionals should engage continuously in educational opportunities, certifications, and workshops. By enriching their understanding and keeping abreast of the latest technological advancements in welding, professionals can not only maximize electrode efficacy but also justify the procurement expenses as a strategic business advantage.
In conclusion, the cost of welding electrodes per kilogram is a multi-faceted consideration that goes beyond just price tags. It involves maintaining a balance between cost and quality—factoring in material, specific applications, and supplier credibility—while leveraging personal expertise to make informed choices. Being proactive and informed will result in more accurate forecasts and budgets, ensuring that the welding tasks not only meet but exceed quality expectations.