Welding electrodes are an integral component in the welding process, and choosing the right type is crucial for ensuring the quality and strength of the weld. With a myriad of choices available, understanding the different types of welding electrodes and their applications can significantly impact the final product's performance and longevity.
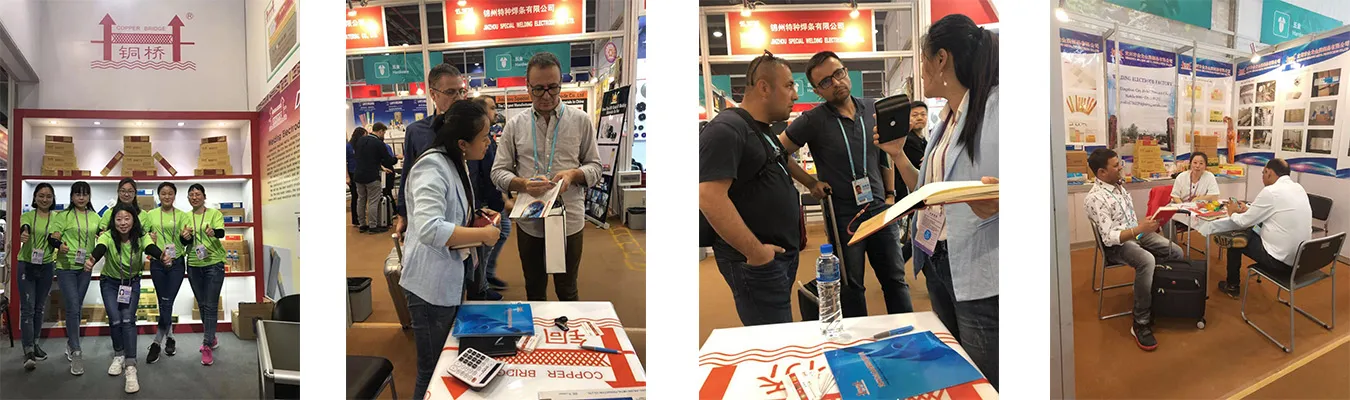
Experience and expertise in welding reveal that electrode selection is predominantly influenced by the base material being welded, the welding position, and the specific mechanical properties desired in the finished weld. These considerations ensure that the welds are robust, durable, and suitable for the intended application.
Among the most commonly used types, consumable electrodes, such as the E6010 and E7018, stand out. E6010 electrodes are renowned for their ability to penetrate deeply, making them ideal for use in situations where high-quality welds are required on dirty, rusty, or painted surfaces. Welders with substantial experience recognize E6010 for its forceful and consistent arc, making it indispensable in field and pipeline welding.
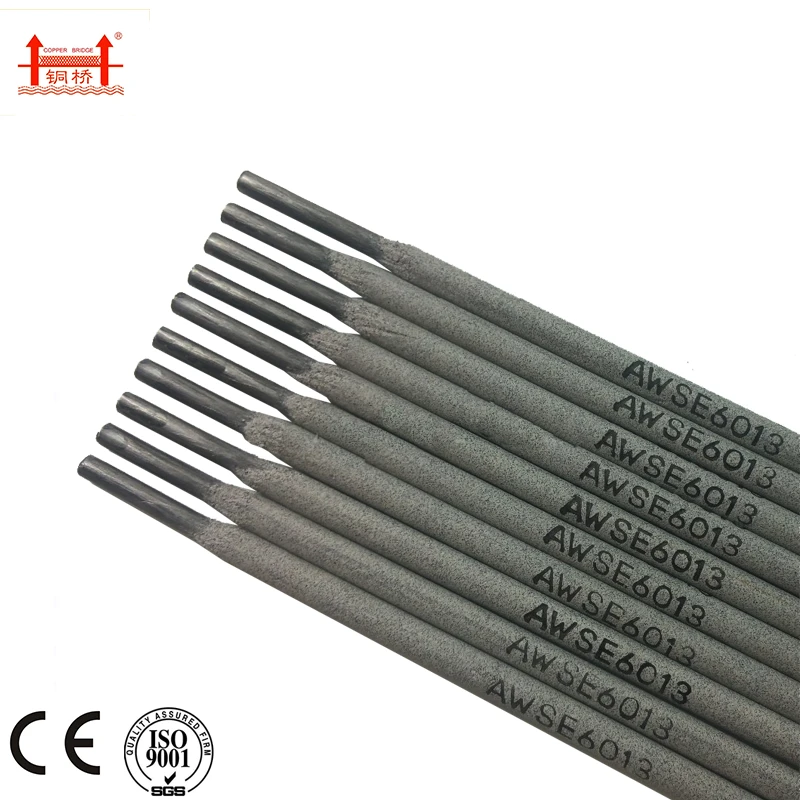
On the other hand,
E7018 electrodes offer a different set of advantages. Known for producing a strong, ductile weld with excellent impact properties, E7018 is frequently employed in construction projects. When leverage and tensile strength are imperative, these electrodes provide the necessary performance attributes, particularly in structural steel applications.
From an authoritative perspective, understanding the balance between deposition rates and the mechanical properties of the weld metal is essential. Low-hydrogen electrodes like E7018 fare exceptionally well in environments prone to cracking, thanks to their low moisture content. Furthermore, professional welders are aware that controlling hydrogen content is critical in preventing weld defects, which can lead to premature failure in stress-bearing joints.
welding electrodes types
In specialized applications, such as those involving cast iron or stainless steel, selecting the appropriate electrode type is pivotal. Nickel-based electrodes are frequently recommended for cast iron, offering compatibility and reducing the risk of cracking and other defects. For stainless steel, the use of austenitic stainless steel electrodes helps maintain the corrosion resistance typical of these alloys.
Authoritative and trustworthy information emphasizes that electrode storage conditions significantly affect their performance and longevity. Maintaining these electrodes in a dry and controlled environment prevents moisture absorption, which is crucial to preserving their mechanical and chemical properties. Manufacturers' guidelines often underscore the importance of proper storage to uphold the electrode's integrity and reliability.
In addition to these widely recognized types, advancements in technology and materials have introduced innovative options, such as flux-cored and metal-cored electrodes. Flux-cored electrodes, valued for their high deposition rates and the ability to weld through contaminants efficiently, have gained popularity in heavy industrial applications. Meanwhile, metal-cored electrodes, offering enhanced arc stability and reduced spatter, are increasingly prevalent in automated and robotic welding processes.
Furthermore, the integration of technology into the welding process, like real-time monitoring and automated parameter adjustments, has bolstered trustworthiness and precision in electrode usage. Skilled professionals now have access to data-driven insights, optimizing electrode performance and ensuring superior weld quality.
In conclusion, welding electrodes are more than just a consumable product; they are a transformative tool shaping the landscape of modern welding. By understanding the nuances of different welding electrode types and their optimal use, professionals can achieve welds of unmatched quality and endurance, meeting the rigorous demands of today's industrial standards.