Welding stainless steel to carbon steel can be a complex task, demanding careful precision and expertise to ensure a strong, durable bond. Using the right welding rod is crucial for achieving optimal results, and selecting the most suitable one involves understanding the distinct properties and needs of both materials involved in the process. Beyond mere adherence, these joints must withstand the mechanical demands and environmental conditions to which they are inevitably exposed.
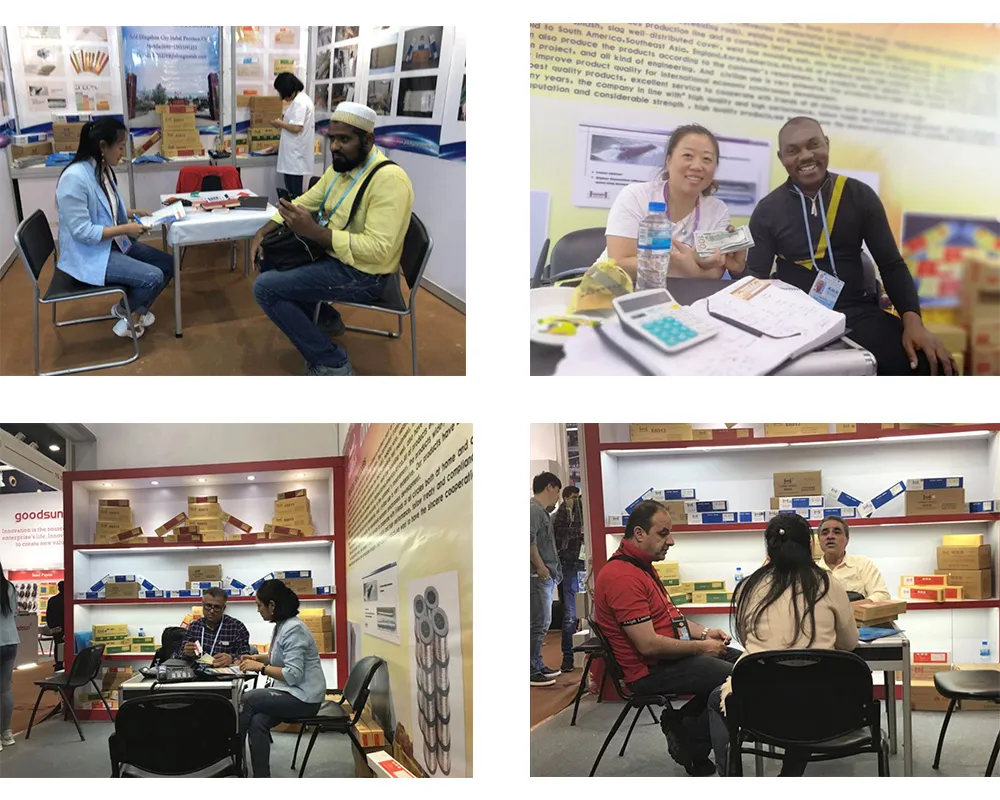
When discussing the choice of welding rods for joining stainless steel to carbon steel, the composition and characteristics of the electrodes play a pivotal role. Typically, stainless steel welding rods like the 309L electrode are recommended for this specific application. These rods are renowned for their ability to effectively manage the different expansion characteristics and mechanical properties of stainless and carbon steels. The 309L has a relatively high chromium and nickel content, attributes that help it create a robust, corrosion-resistant weld that ensures the longevity and integrity of the joint.
A paramount consideration in such welding tasks is the understanding of metallurgical properties. Carbon steel is prone to rust when exposed to moisture unless protected, while stainless steel's resistance to oxidation and rust is due to its chromium content. Welding these two dissimilar metals requires balancing these properties to ensure that the bond remains durable and resistant to corrosion. The high alloy composition in certain welding rods helps mitigate potential complications arising from thermal expansion differences, minimizing structural stress in the welded joint over time.
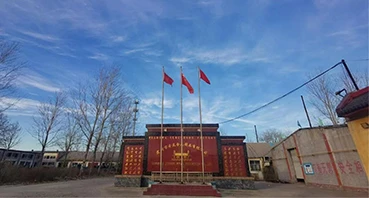
Expertise in welding techniques extends beyond just choosing the right rod. A skilled welder needs to recognize the importance of pre-weld preparations such as cleaning the metal surfaces to remove any dirt, oil, or rust that could compromise the weld. Additionally, they must be adept in employing proper heat inputs, particularly with stainless steel to prevent warping or compromising corrosion resistance. Techniques like back purging stainless steel with inert gases can be essential for maintaining the inner shielded atmosphere, protecting the weld's integrity from the root side.
stainless steel to carbon steel welding rod
Emphasizing authoritativeness, case studies from the industry reveal the successful application of welding rods specifically designed for dissimilar metal welding. For example, in industrial settings like petrochemical plants where such welds are commonplace, the reliability of these welding consumables is regularly tested under harsh conditions. Documentations show that welds made with rods like 309L consistently withstand pressure and corrosion challenges over extended periods, underscoring their dependability and reinforcing their recommended usage.
Trustworthiness in practice arises from following systematic protocols and adhering to industry standards. Certification of welding rods and adherence to regulatory standards by organizations such as the American Welding Society (AWS) provide a benchmark for quality assurance. Utilizing certified electrodes ensures not only compliance but also confidence in the weld quality and performance, essential for critical applications where failure is not an option.
From a procedural standpoint, maintaining consistency in welding parameters such as voltage, speed, and electrode angles further contributes to a successful weld. Welding professionals emphasize that deviation from these parameters can lead to suboptimal welding results, including porosity, poor penetration, and weakened joints — pitfalls that are avoidable with vigilant adherence to technique.
In summary, when welding stainless steel to carbon steel, it's essential to draw upon a comprehensive understanding that blends material science with technical skill. The choice of a suitable welding rod, preparation processes, and stringent adherence to welding best practices collectively facilitate the creation of enduring, high-quality welds. As industries evolve, continuous advancements in welding technologies and materials should be zealously pursued, ensuring that the methods and resources employed remain at the forefront of efficiency, safety, and reliability.