Selecting the appropriate welding rod size is a critical decision that impacts the quality and durability of your welding projects. Whether you are a professional welder or a hobbyist, understanding the factors that influence this decision can vastly improve your output. Drawing from extensive experience and recognized expertise, we delve into the key considerations you must keep in mind to make an informed decision.
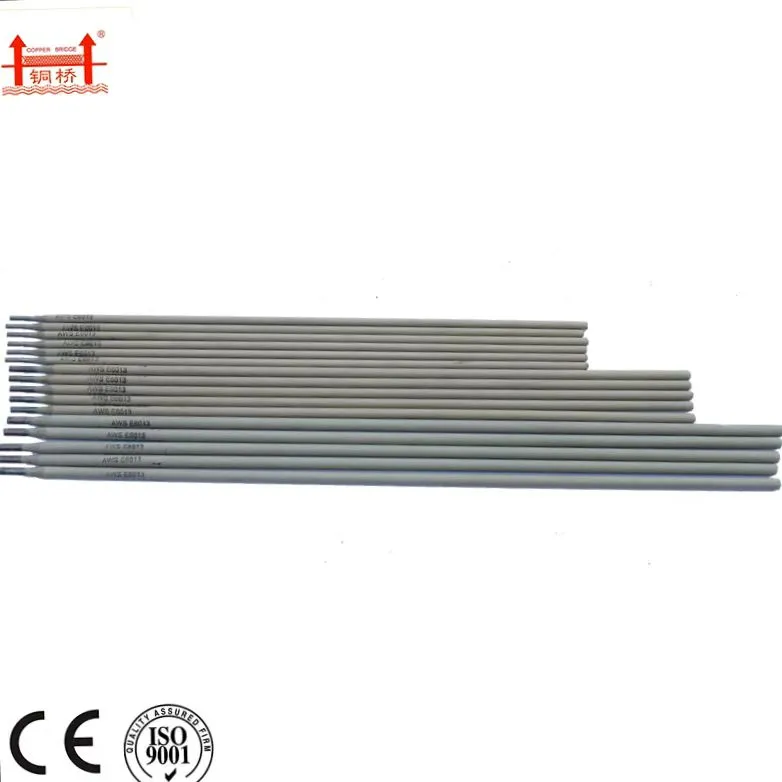
Welding rod size significantly affects the penetration and overall strength of the weld. A larger diameter rod provides deeper penetration, making it ideal for thicker materials, whereas a smaller diameter is suited for thinner materials, offering a smoother finish. Therefore, assessing the material thickness of the project is the first and foremost step in choosing the right size. For instance, a 1/8-inch rod is commonly suitable for general-purpose welding and serves a wide range of thicknesses efficiently. However, for sheet metals, going for a 3/32-inch rod could be more beneficial.
Material type also dictates rod size selection. Different metals respond uniquely to welding, and hence require different approaches. For example, aluminum demands rods that are specifically designed to handle its properties, usually smaller in size to manage heat distribution effectively. On the other hand, for cast iron or stainless steel, rods with specific coatings and diameters should be chosen to accommodate the distinct thermal characteristics and oxidation levels of these metals.
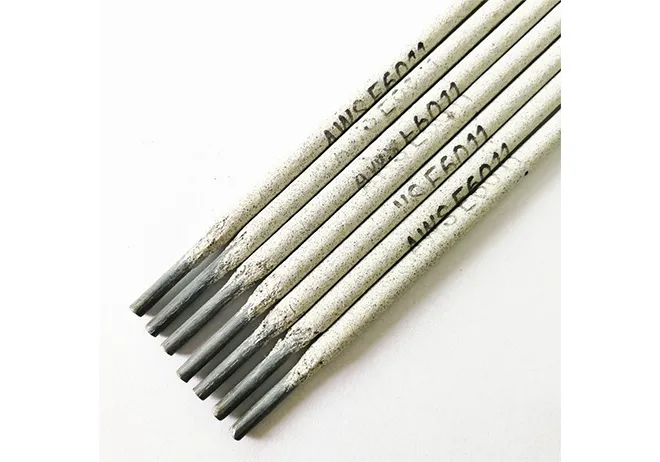
The type of welding process you engage in directly correlates to the choice of rod size. Stick welding, known for its versatility, often requires various rod sizes to accommodate different welding positions, such as flat, vertical, or overhead. Understanding the dynamics of your welding position can dramatically influence your choice. A simpler, yet crucial fact often overlooked is the welder’s comfort and control. Larger rods can be awkward in tight spaces; hence selecting a size that allows optimal maneuverability can enhance both safety and quality of the weld.
how to choose welding rod size
Moreover, consider the power source’s output compatibility with the rod. Every welding machine has its output range, and using a rod size inconsistent with this range can lead to poor arc stability and suboptimal welds. Generally, larger rods require higher amperage settings, and so it's essential to ensure your equipment can handle the specified range when opting for a thicker rod.
A unique, often understated aspect is the post-weld cleanup. Larger electrodes may result in increased slag, which requires additional cleanup and can affect the finish if not executed meticulously. Thus, sometimes choosing a slightly smaller size might benefit the overall presentation of the final work, especially in precision projects where aesthetics matter as much as structural integrity.
The latest advancements in welding technology and materials science have introduced rods with enhanced features. Some rods now offer advanced flux coatings that allow for varied size use across different applications with lesser cleanliness trade-offs. Keeping abreast with such innovations and understanding their application can offer welders a competitive edge in both industrial and artistic domains.
To optimize weld results, gathering firsthand accounts from experienced welders or joining professional forums can provide invaluable insights. The discussed parameters are essential, yet experience sharpens your decision-making process, ultimately refining your technique over time. In conclusion, the art of selecting the right welding rod size transcends simple guidance – it is a blend of technical understanding, project context, and evolving knowledge in weld science. Such a comprehensive approach ensures that welders can consistently achieve proficient and reliable results across various applications.